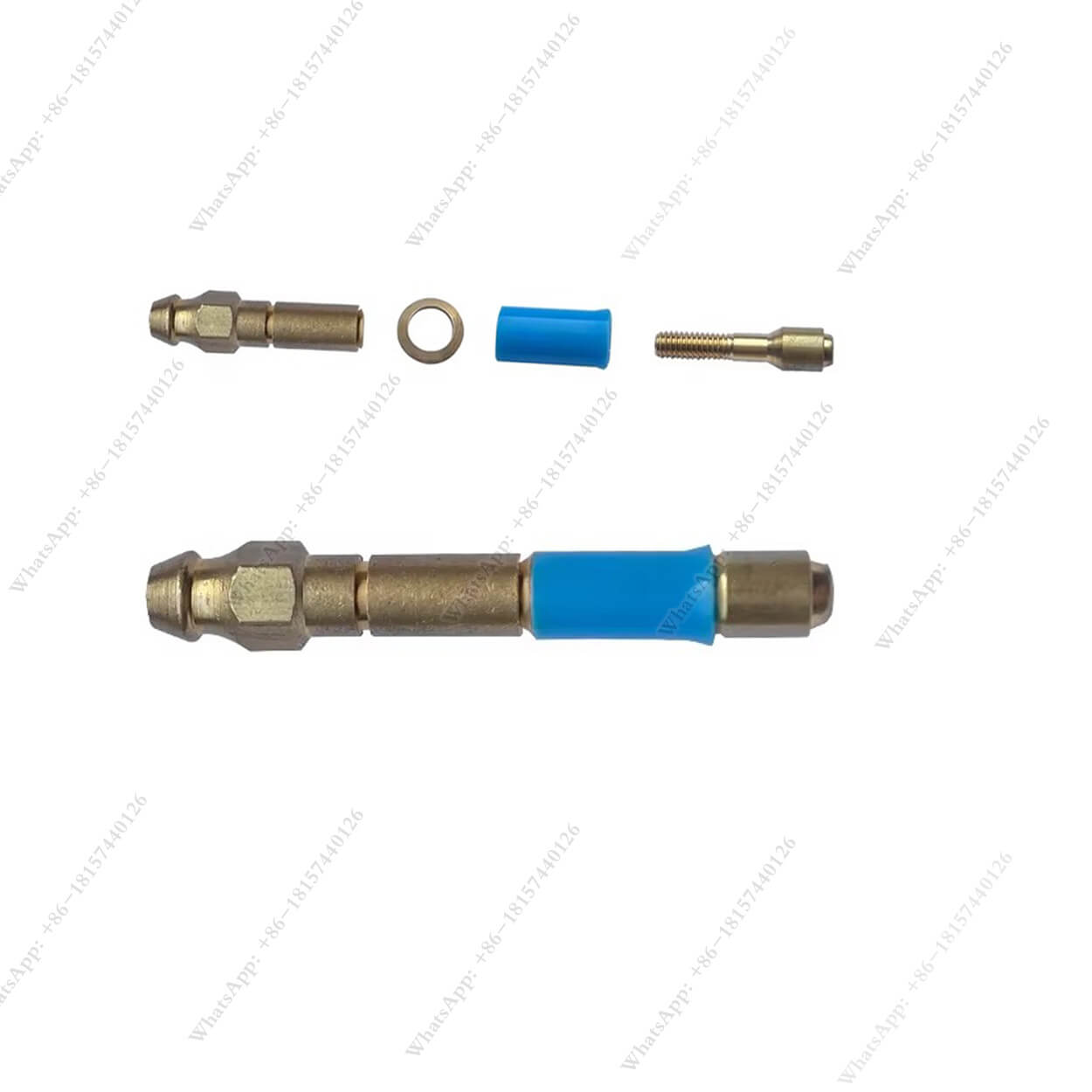
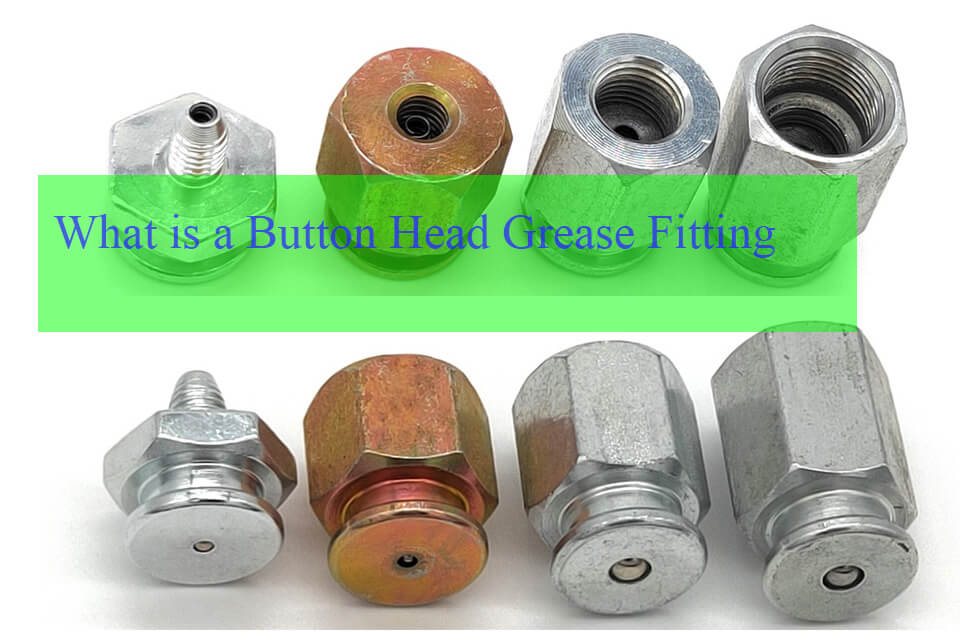
Engrasadores de cabeza abotonada: esenciales para aplicaciones industriales de construcción, de servicio pesado y a prueba de agua
En el mundo del mantenimiento de maquinaria pesada, garantizar un funcionamiento sin problemas y una larga vida útil es esencial. Un componente clave que ayuda a lograr esto son los engrasadores de cabeza abotonada.
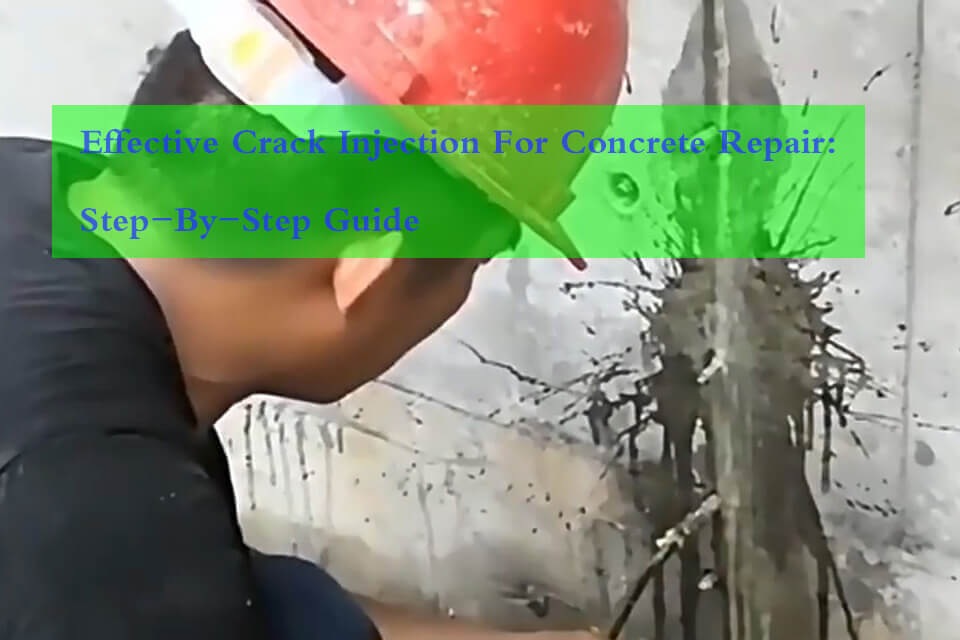
Inyección eficaz de grietas para la reparación del hormigón: guía paso a paso
Las grietas en el hormigón son un problema común en muchas estructuras y suelen provocar filtraciones que pueden causar daños importantes si no se sellan correctamente. La inyección de grietas es una técnica muy eficaz para reparar estas grietas y detener la infiltración de agua.
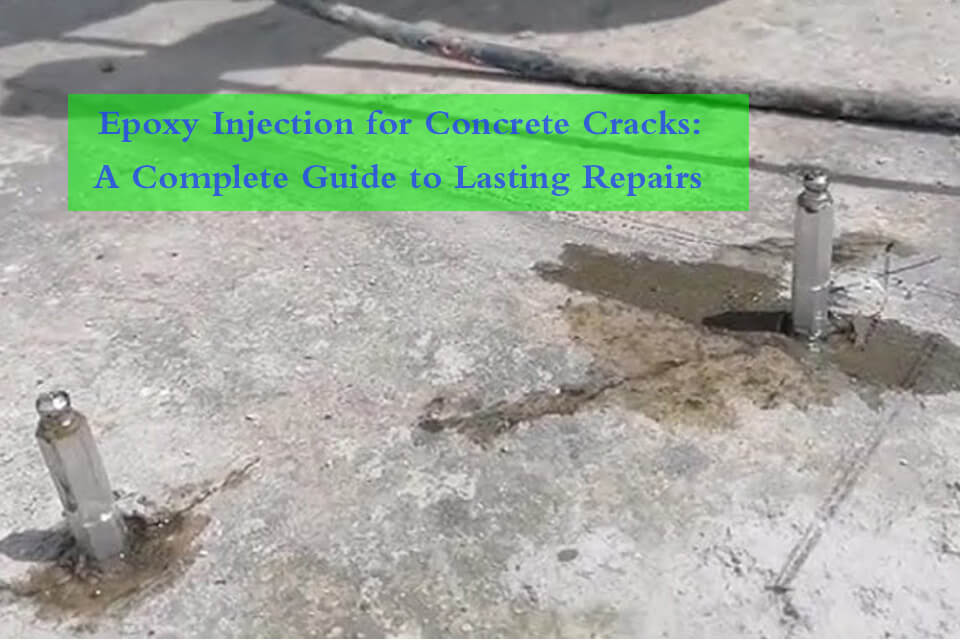
Inyección de epoxi para grietas en hormigón: una guía completa para reparaciones duraderas
En este artículo, aprenda cómo la inyección de epoxi restaura eficazmente la integridad estructural del concreto agrietado, proporcionando una solución duradera y resistente.