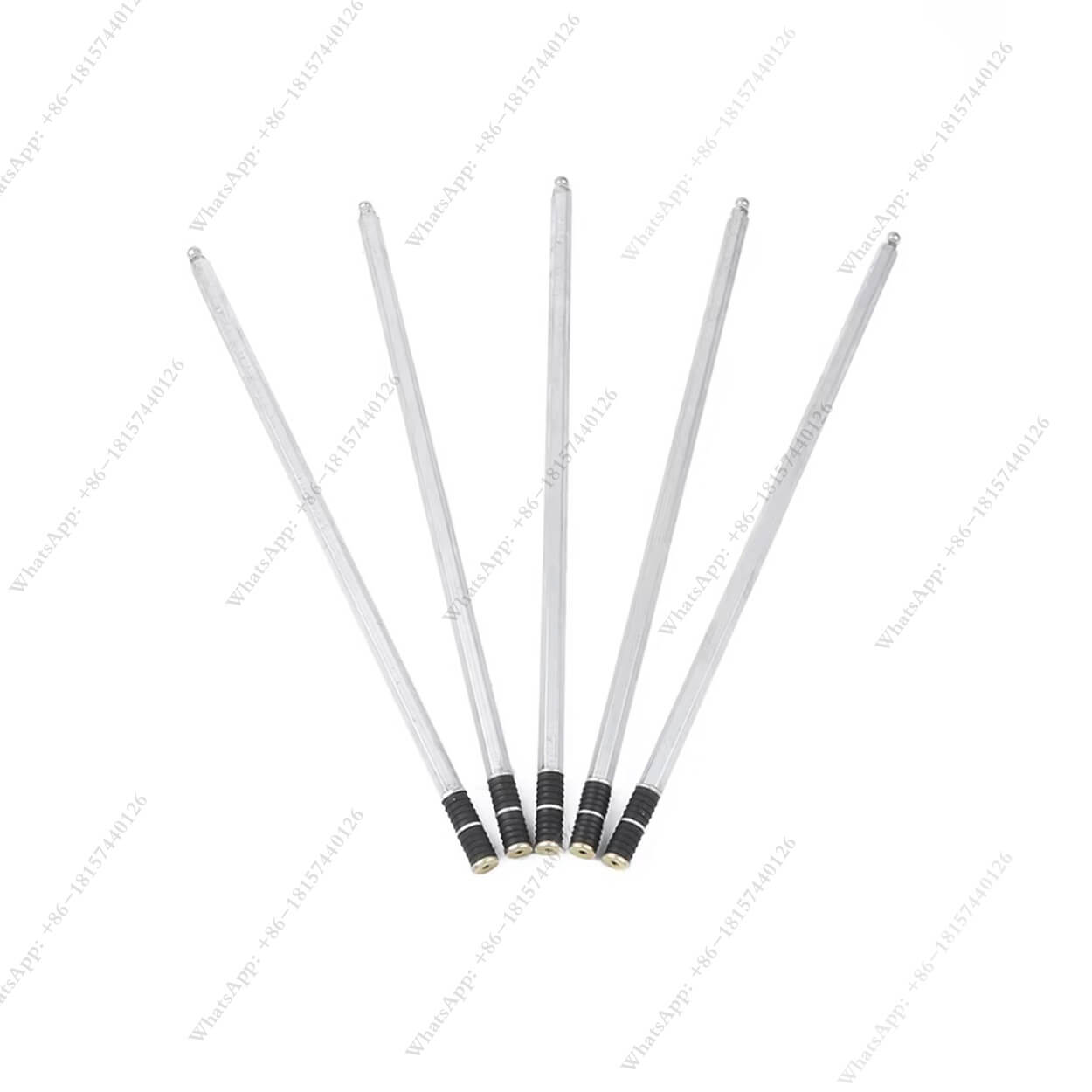
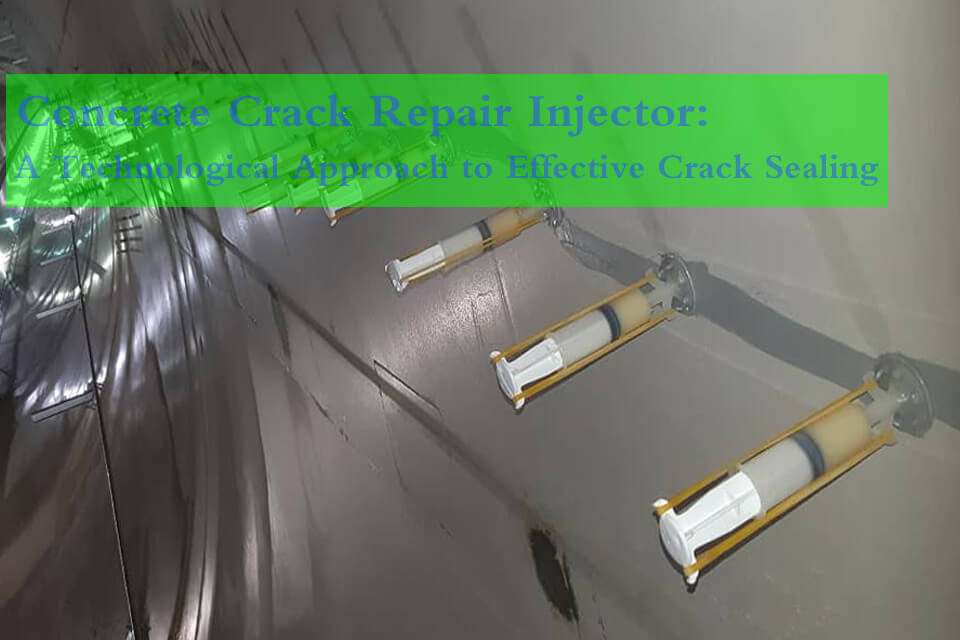
Reparación de hormigón: el innovador inyector para reparar grietas en el hormigón
El inyector de reparación de grietas de hormigón es un dispositivo autónomo de alta eficiencia diseñado específicamente para la reparación de grietas en estructuras de hormigón.
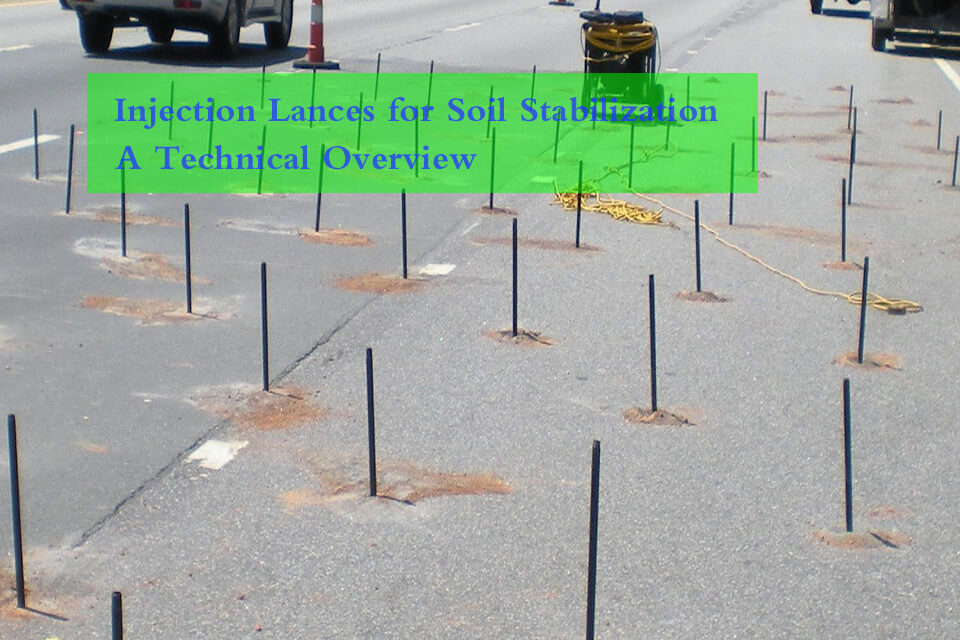
Lanzas de inyección para estabilización de suelos: descripción técnica
Las lanzas de inyección son herramientas esenciales para la estabilización y el refuerzo del suelo, diseñadas para mejorar la integridad estructural del suelo inyectando agentes estabilizadores a profundidades precisas.
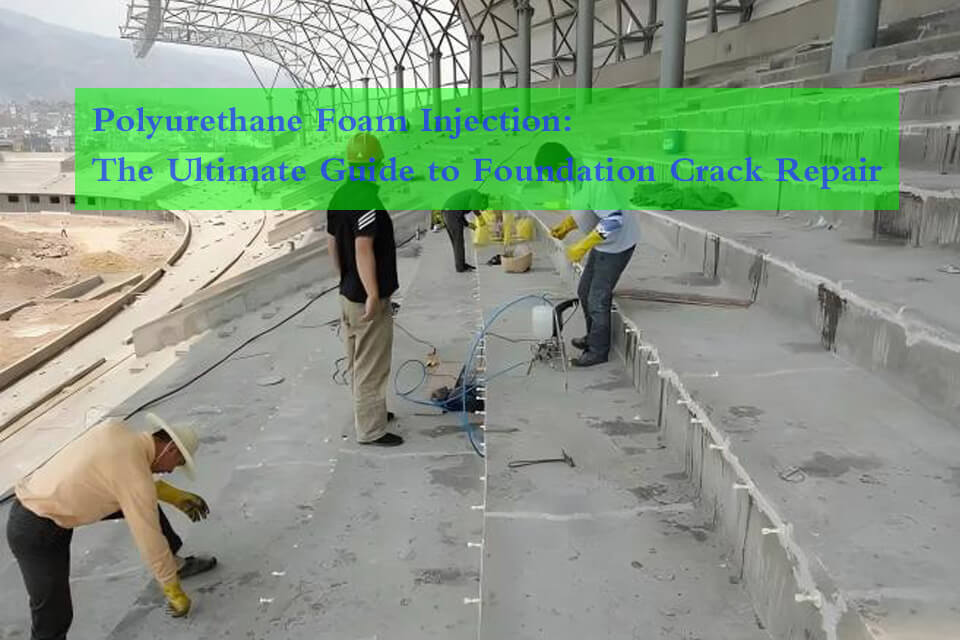
Inyección de espuma de poliuretano: la guía definitiva para reparar grietas en cimientos
¿Tiene problemas con las molestas grietas en los cimientos que no desaparecen? ¡No busque más! Esta guía completa le mostrará la solución innovadora de la inyección de espuma de poliuretano para reparar grietas.