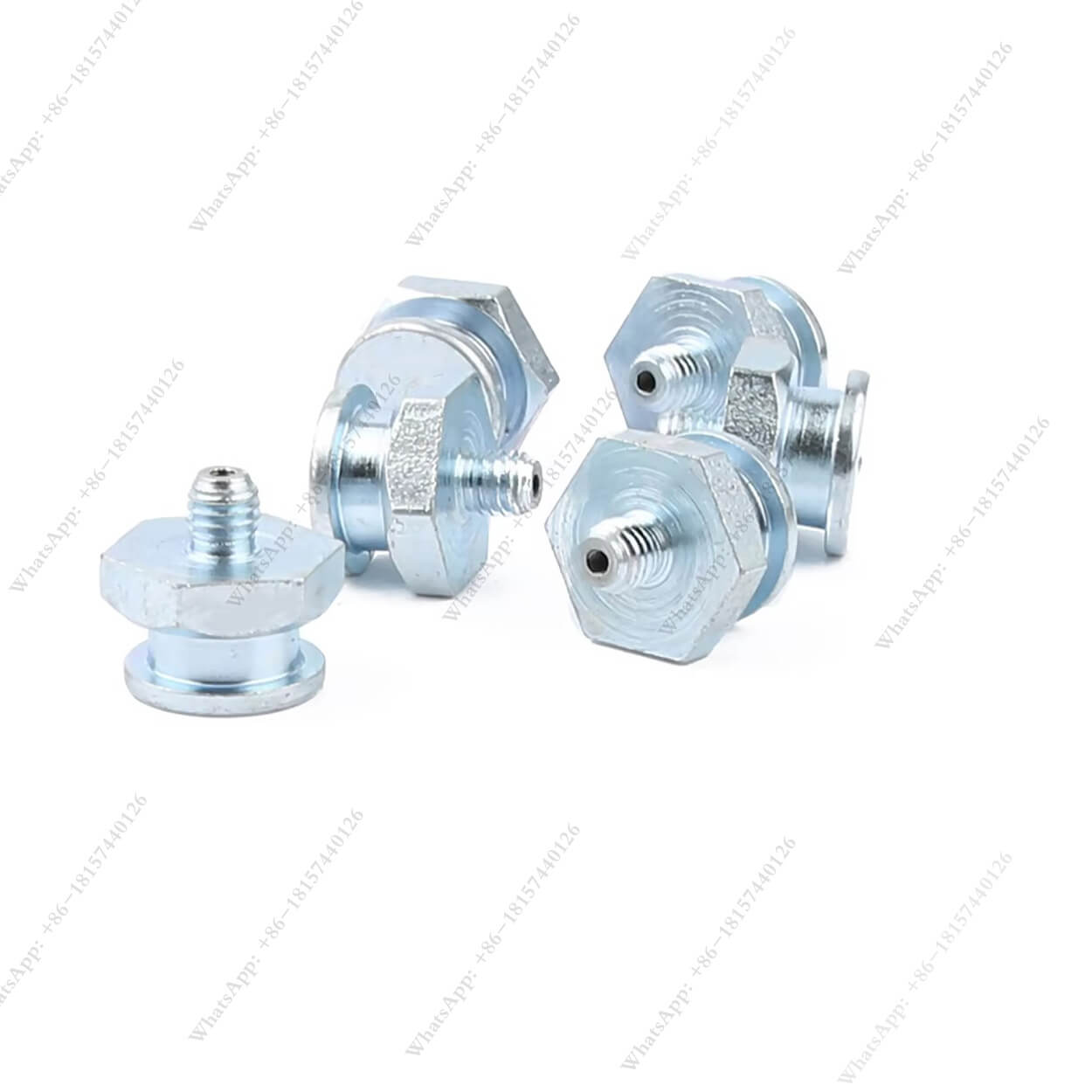
Lorem ipsum dolor sit amet, consectetur adipiscing elit, sed do eiusmod Lorem ipsum dolor sit amet consectetur adipiscing elit, sed do eiusmod lorem ipsum
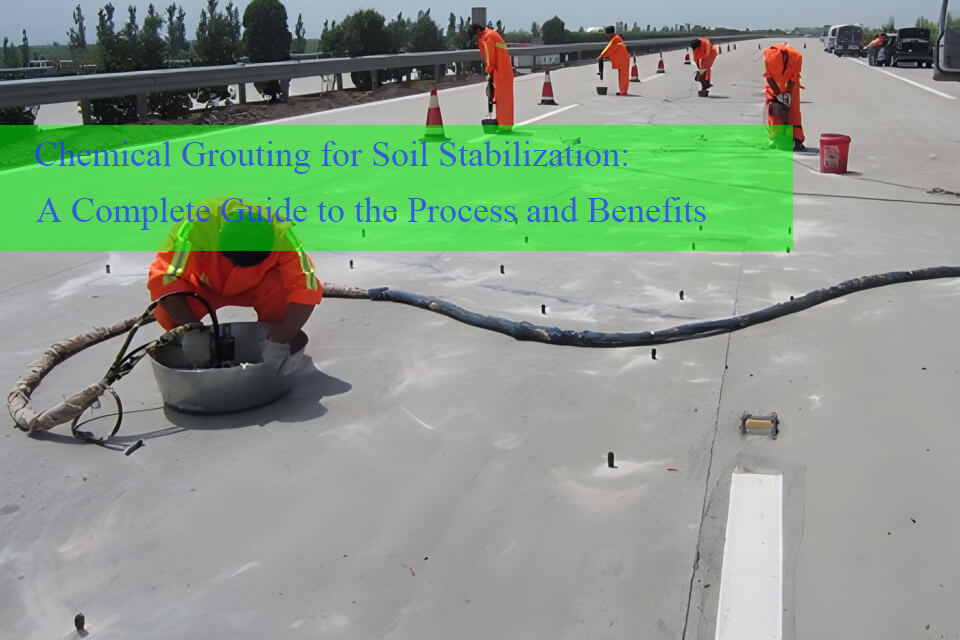
Inyección química para estabilización de suelos: guía completa sobre el proceso y sus beneficios
La lechada química es un método eficaz para la estabilización de suelos y el fortalecimiento de estructuras en la construcción y la ingeniería civil.
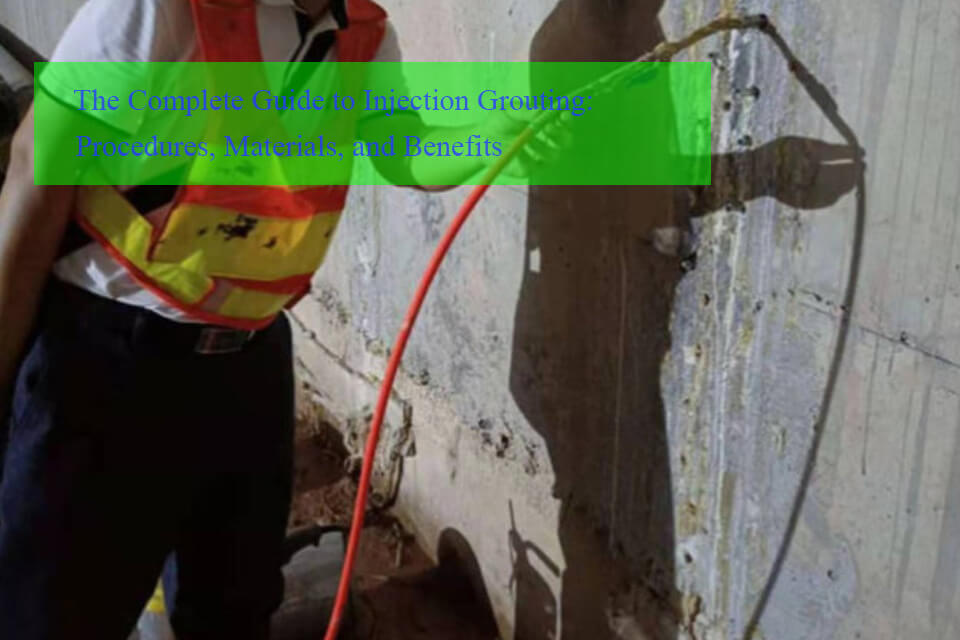
¿Qué es el procedimiento de inyección de lechada? Una guía detallada para reparaciones de hormigón y mampostería
La inyección de lechada es una técnica crucial utilizada en la construcción y el mantenimiento para reparar y reforzar estructuras de hormigón y mampostería.
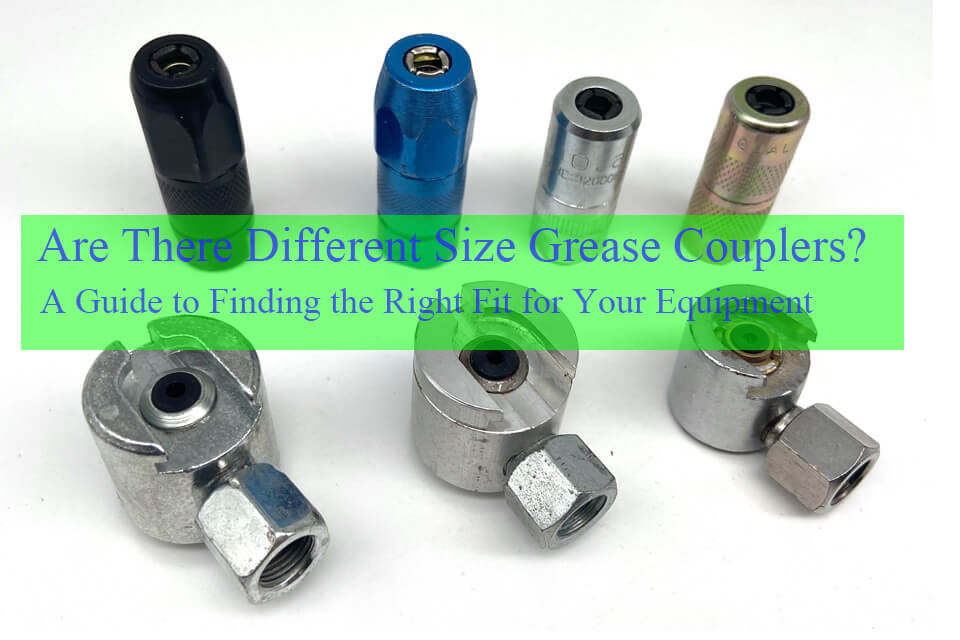
¿Existen acopladores de grasa de distintos tamaños? Guía para encontrar el adecuado para su equipo
Los acopladores de grasa son herramientas esenciales en el mantenimiento de la maquinaria y la inyección de grietas, garantizando que la lubricación llegue a todas las partes críticas que mantienen el equipo funcionando sin problemas.