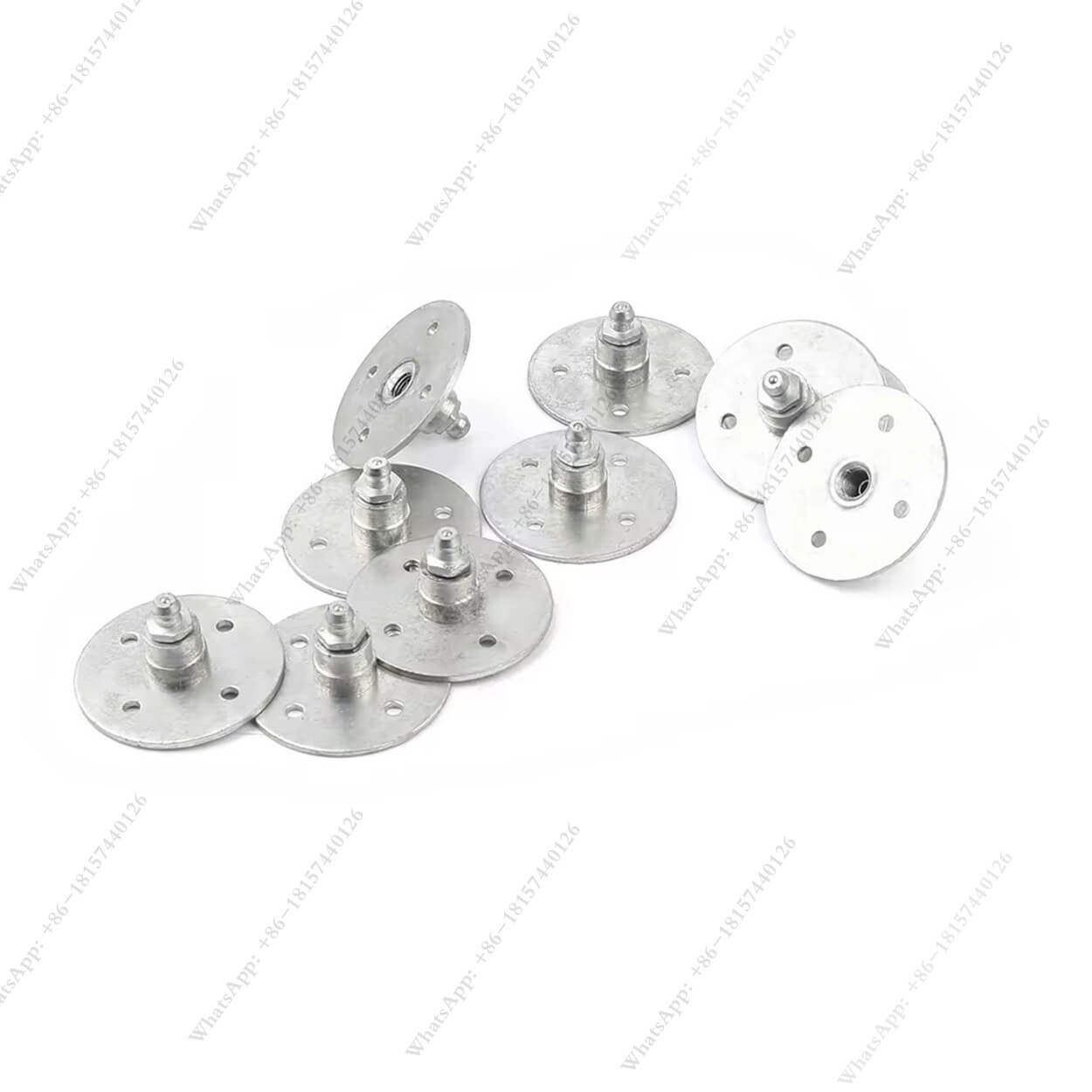
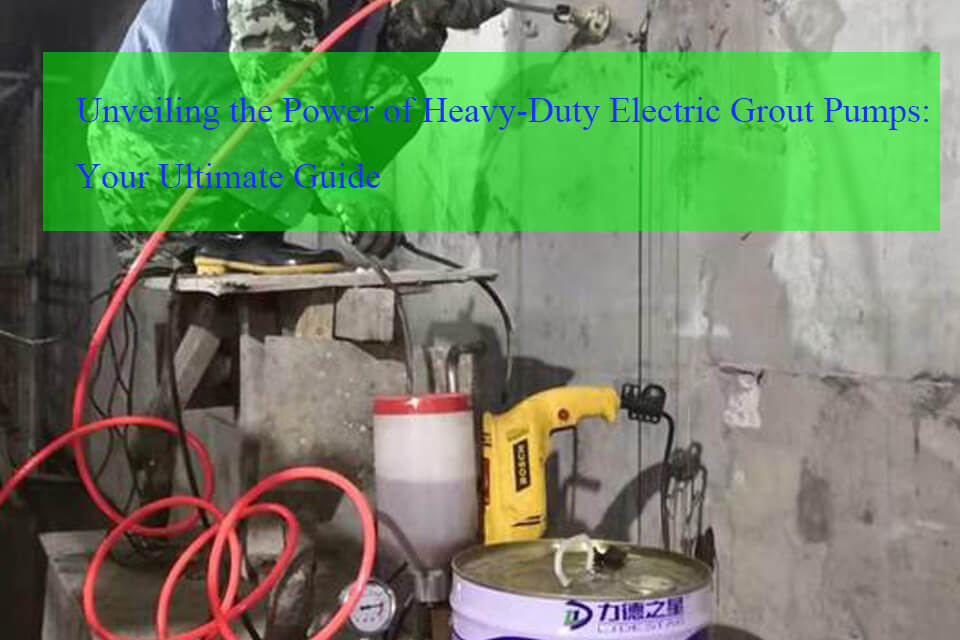
Die Leistungsfähigkeit leistungsstarker elektrischer Mörtelpumpen entdecken: Ihr ultimativer Leitfaden
Haben Sie sich schon einmal gefragt, wie große Strukturen stabil und intakt bleiben? Das Verfugen spielt eine Schlüsselrolle!
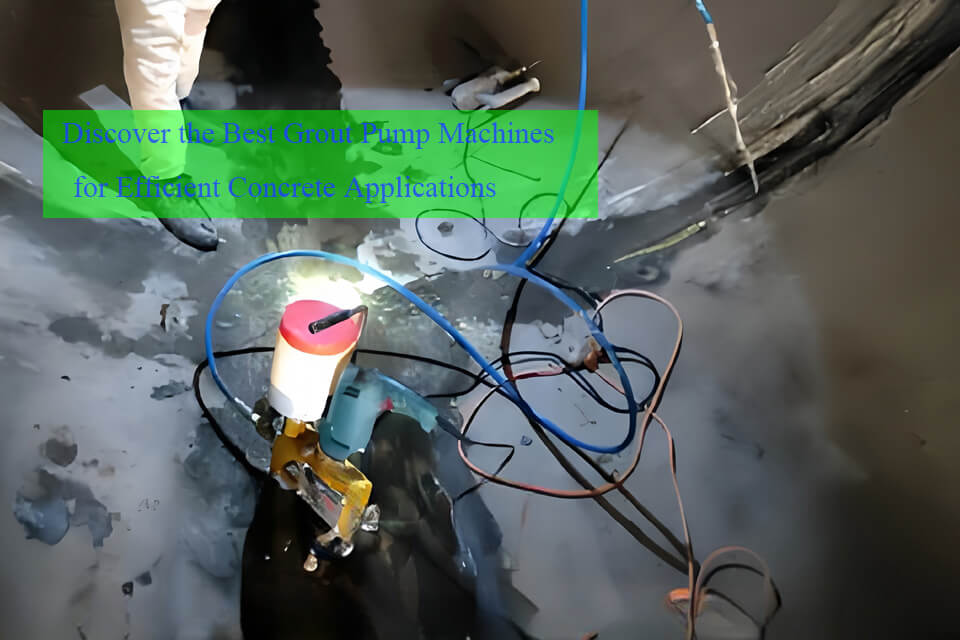
Entdecken Sie die besten Mörtelpumpen für effiziente Betonanwendungen
Mörtelpumpen sind im Baugewerbe unverzichtbare Werkzeuge. Sie helfen den Arbeitern, Lücken zu füllen und Strukturen zu verstärken.
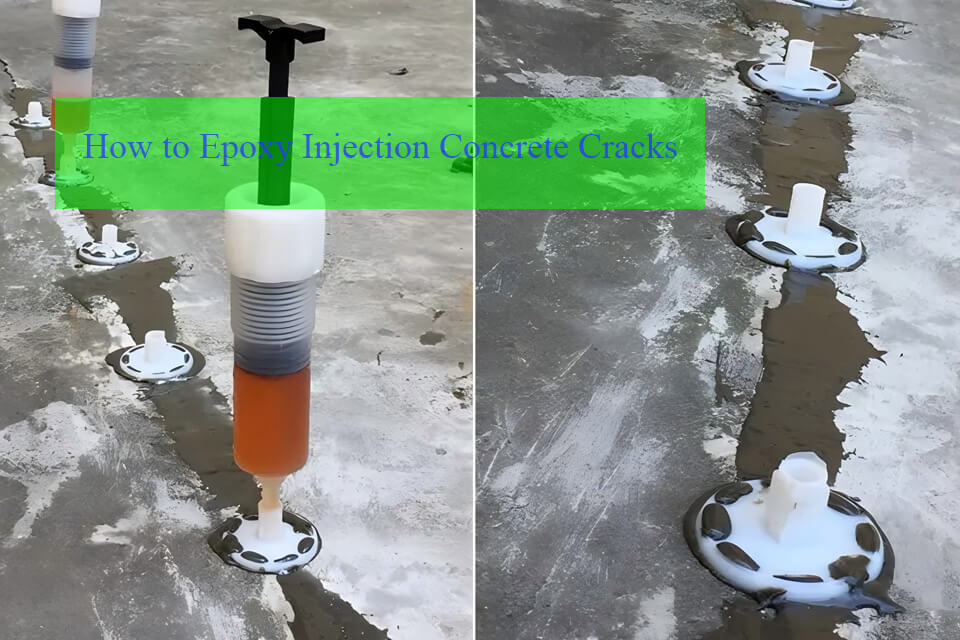
So injizieren Sie Betonrisse mit Epoxidharz: Eine umfassende Anleitung
Betonkonstruktionen neigen aufgrund verschiedener Faktoren wie natürlicher Setzung, Temperaturschwankungen und hoher Belastung dazu, im Laufe der Zeit Risse zu bilden.