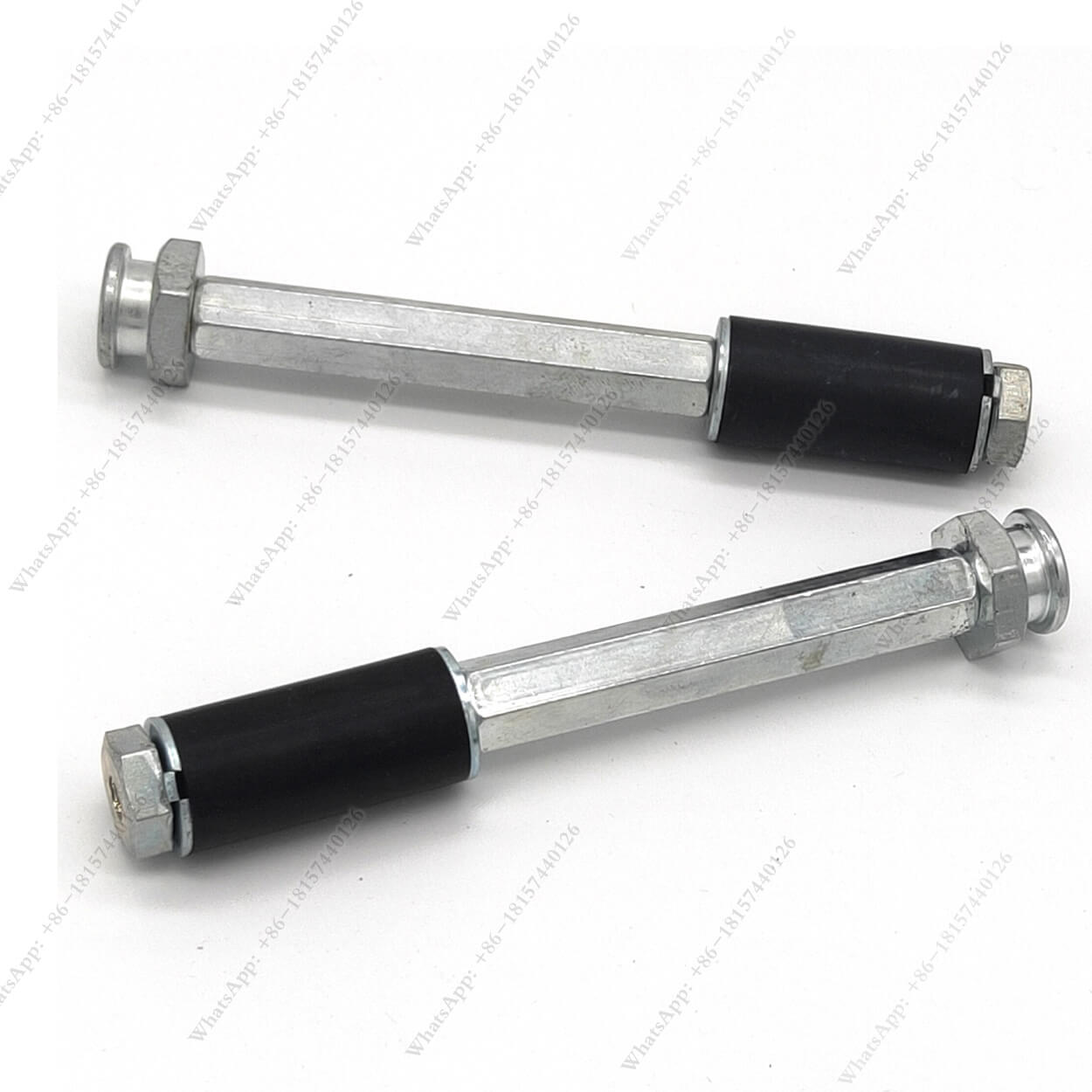
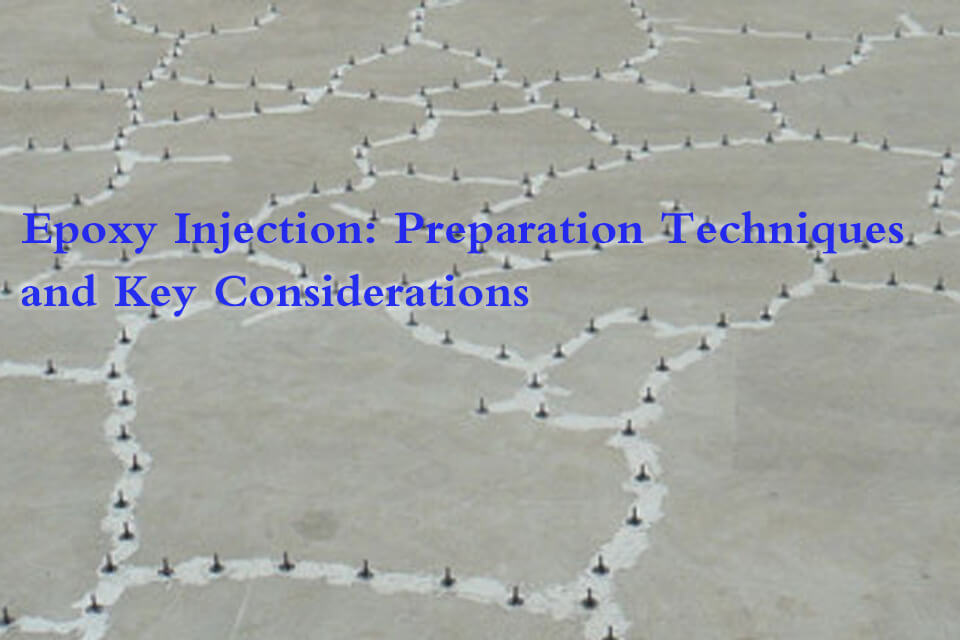
Inyección de epoxi: técnicas de preparación y consideraciones clave
La inyección de epoxi es una técnica sofisticada que se emplea en la restauración de estructuras de hormigón mediante la aplicación de una resina epoxi de alta resistencia y baja viscosidad en las grietas.
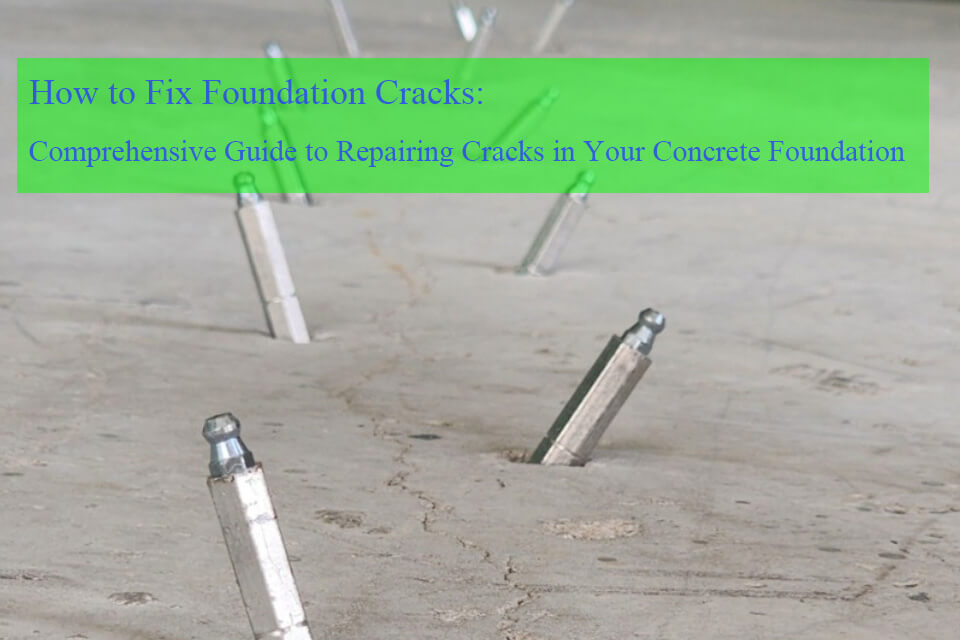
Cómo reparar grietas en cimientos: guía completa para reparar grietas en cimientos de hormigón
Las grietas en los cimientos pueden ser una vista alarmante, pero comprender cómo abordarlas puede ahorrarle tiempo, dinero y preocupaciones.
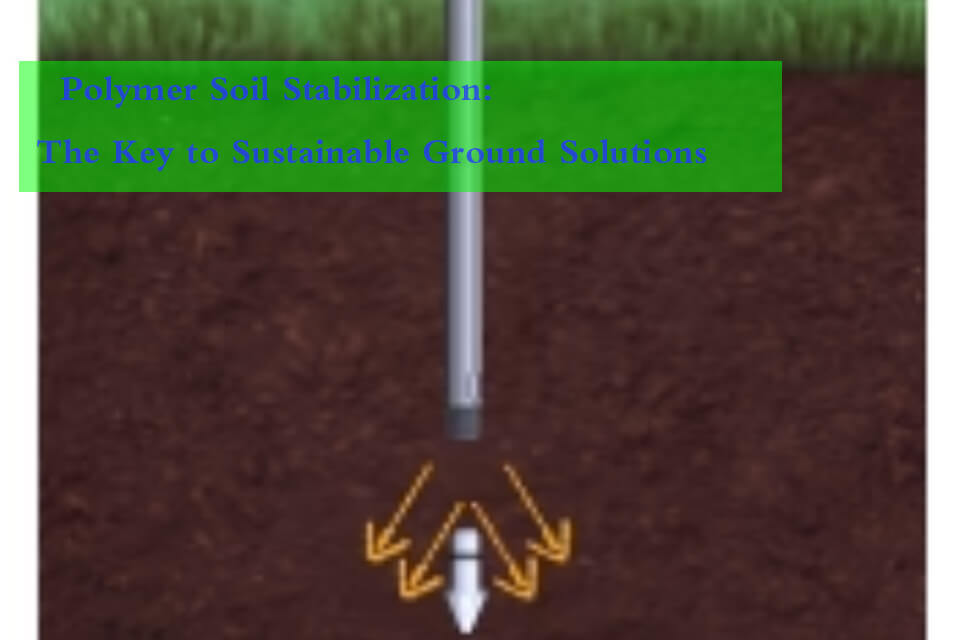
Estabilización de suelos mediante polímeros: la clave para soluciones terrestres sostenibles
La estabilización del suelo es vital en la construcción y la ingeniería civil, particularmente para mejorar las propiedades del suelo y garantizar una infraestructura duradera.