Button Head Grease Fittings: Essential for Construction, Heavy-Duty, and Waterproof Industry Applications
Table of Contents
Summary
In this guide, you’ll learn everything there is to know about button head grease fittings, their benefits over standard fittings, and why they’re a top choice for high-pressure applications. Whether you’re new to industrial maintenance or simply curious, this article will break down the details into simple terms and actionable tips.
What Is a Button Head Grease Fitting?
A button head grease fitting is a specialized component designed for delivering lubrication to heavy machinery under high pressure. Known for its larger, flatter head, this fitting provides a secure, tight seal that prevents grease from leaking. Unlike standard Zerk fittings, button head fittings are highly effective for heavy-duty and industrial use.
Button head fittings are commonly used in construction, mining, and other industries where machinery endures constant, intense wear and tear. This fitting ensures that all components are properly lubricated, helping to avoid damage and costly repairs.
Why Choose Button Head Grease Fittings Over Standard Zerks?
Button head grease fittings offer unique advantages, particularly in high-pressure situations. Unlike standard Zerk fittings, button heads provide a stronger, more resilient connection, which is ideal for industrial and heavy-duty machinery.
Key Advantages
- Durability:Button head fittings withstand extreme pressures, making them suitable for heavy equipment.
- Leak Prevention:Their design minimizes the chance of grease leakage, which is common with Zerk fittings in high-stress environments.
- Ease of Use:Button heads are easier to engage with grease guns, as the larger head offers a reliable connection point.
How Do Button Head Grease Fittings Work?
The button head grease fitting functions by creating a direct channel for grease to flow into machinery components. The flat, broad head allows a grease gun to easily attach and pump lubricant, ensuring that grease reaches all necessary parts without excessive buildup.
Lubrication Process
- Attach the grease gun to the button head fitting.
- Press and hold to ensure a firm seal.
- Pump the grease into the fitting until the required amount has been delivered.
- Release and wipe away any excess grease.
By allowing controlled grease flow, button head fittings help prevent over-lubrication, which can cause pressure buildup and potential damage.
Types of Button Head Grease Fittings
Button head grease fittings come in various types to match specific machinery and application needs. Here are the main types:
- NPT (National Pipe Thread):Commonly used in the U.S., NPT fittings are threaded to provide a tight, secure connection. They’re ideal for industrial settings.
- Giant Button Head Fittings:These are larger and suitable for heavy machinery with higher grease requirements.
- Lubo Button Head Fittings: A trusted brand known for durable, high-quality fittings, lubo’s button heads are widely used in industries with rigorous lubrication needs and injection requirements.
Each type is designed for specific requirements, so understanding which fitting suits your machine is essential.
Benefits of Button Head Grease Fittings
Using button head grease fittings over other options provides several key benefits:
- Extended Equipment Life:Proper lubrication is critical for the longevity of machinery. Button head fittings help deliver consistent grease flow, reducing friction and wear.
- Increased Efficiency:Regular lubrication with button head fittings ensures smooth operation, which can enhance equipment efficiency and performance.
- Reduced Maintenance Costs:By preventing over-lubrication and reducing wear, button head grease fittings lower the frequency of costly repairs.
Applications of Button Head Grease Fittings
Button head grease fittings are commonly found in:
- Heavy Industrial Machinery:Used in construction, mining, and factory equipment, where high-pressure lubrication is essential.
- Automotive Applications:For vehicles that operate in rugged conditions, such as off-road vehicles and trucks.
- Marine Equipment:Ensures smooth operation and durability in harsh marine environments where corrosion and wear are prevalent.
These fittings are invaluable in any setting that requires frequent and high-pressure lubrication.
Choosing the Right Button Head Grease Fitting
Routine maintenance helps keep grease fittings in top shape. Here are some tips:
- Inspect Regularly: Check for wear, clogs, or damage.
- Clean Before and After Use: Wiping the fittings keeps contaminants out.
- Replace as Needed: Worn fittings can cause leaks and should be replaced promptly.
Keeping your grease fittings well-maintained ensures effective lubrication and long-lasting machinery performance.
Installation Process for Button Head Grease Fittings
Step-by-Step Guide
- Preparation:Ensure the fitting port is clean and free of debris.
- Alignment:Align the fitting with the threaded port on your machinery.
- Tighten:Screw the fitting into the port, tightening securely to prevent leaks.
Testing: After installation, attach a grease gun to confirm the connection and ensure smooth grease flow
Common Mistakes to Avoid
- Avoid over-tightening, as it may damage the threads.
- Ensure compatibility between the fitting and the machinery to prevent poor lubrication.
Maintenance Tips for Button Head Grease Fittings
Regular maintenance extends the lifespan of button head grease fittings and keeps machinery running efficiently.
Key Maintenance Practices
- Cleaning and Inspection:Regularly clean the fitting to prevent buildup that may cause clogging.
- Lubrication Schedule:Follow a lubrication schedule based on the machinery’s operating conditions.
- Troubleshooting Common Issues:If grease fails to flow, check for clogs or leaks and replace damaged fittings promptly.
Routine checks and timely replacement prevent unexpected machinery downtime.
Popular Brands and Sizes of Button Head Grease Fittings
Several brands provide high-quality button head grease fittings in various sizes to fit different machinery needs.
Brand | Fitting Type | Sizes Available |
Lubo | Standard and Giant | 1/4″, 3/8″, 1/2″ |
NPT | National Pipe Thread | 1/8″ – 1″ |
Giant | High-capacity fittings | 1/4″, 3/4″ |
Each brand brings unique features, so consider your equipment’s specific requirements when choosing.
Where to Buy Button Head Grease Fittings and Cost Overview
You can find button head grease fittings from reputable suppliers like Amazon, Lubo, and McMaster-Carr. Prices vary based on brand, type, and size. Typically, fittings range from $5 to $20 per fitting, with some high-end models reaching up to $50.
For bulk purchases, consider reaching out to specialized industrial suppliers, such as Lubo, which may offer discounted rates for large orders.
Summary of Key Points
- Button head grease fittings are essential for heavy-duty machinery and high-pressure applications.
- They offer better durability and efficiency over standard Zerk fittings.
- There are various types, including NPT, Giant, each suited to different needs.
- Regular maintenance and correct installationare vital to maximizing their effectiveness.
- Available from multiple brands and suppliers, with prices based on size and type.
For anyone maintaining industrial equipment, understanding button head grease fittings can make a significant difference in performance and lifespan. Proper use and maintenance keep machinery running smoothly, saving time and money in the long run.
Comments
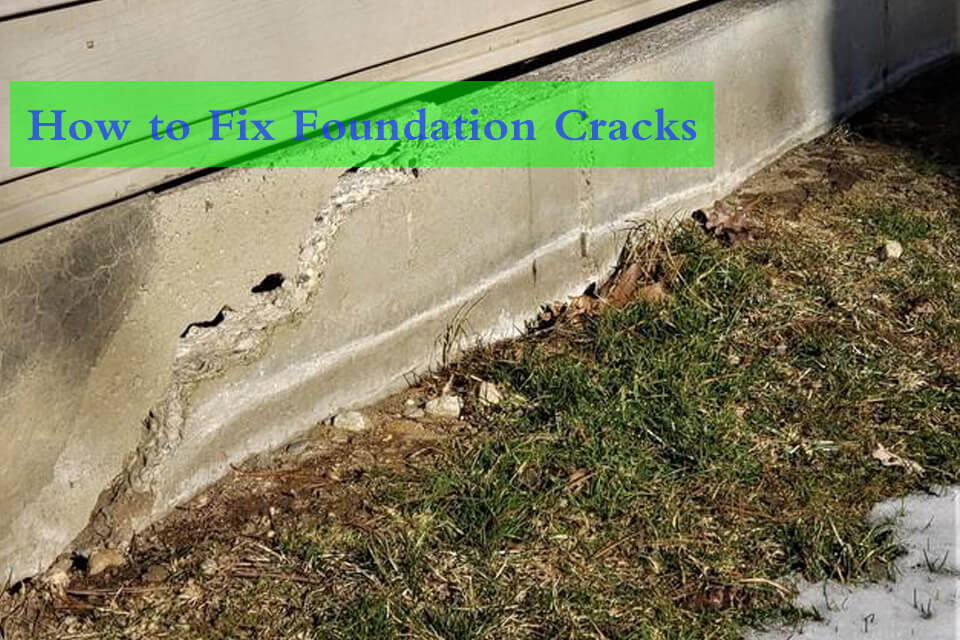
How to Fix Foundation Cracks: A Comprehensive Guide
Foundation cracks can jeopardize the structural integrity of any building, posing a risk to both property and safety.
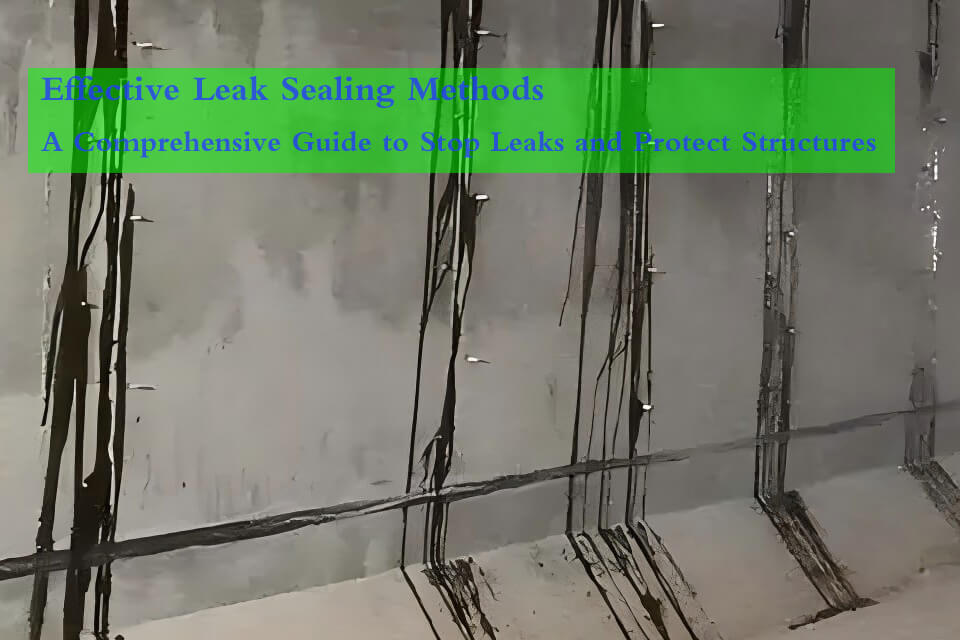
Effective Leak Sealing Methods: A Comprehensive Guide to Stop Leaks and Protect Structures
Leaks can occur in a wide range of environments, from commercial buildings to homes, and even industrial facilities.
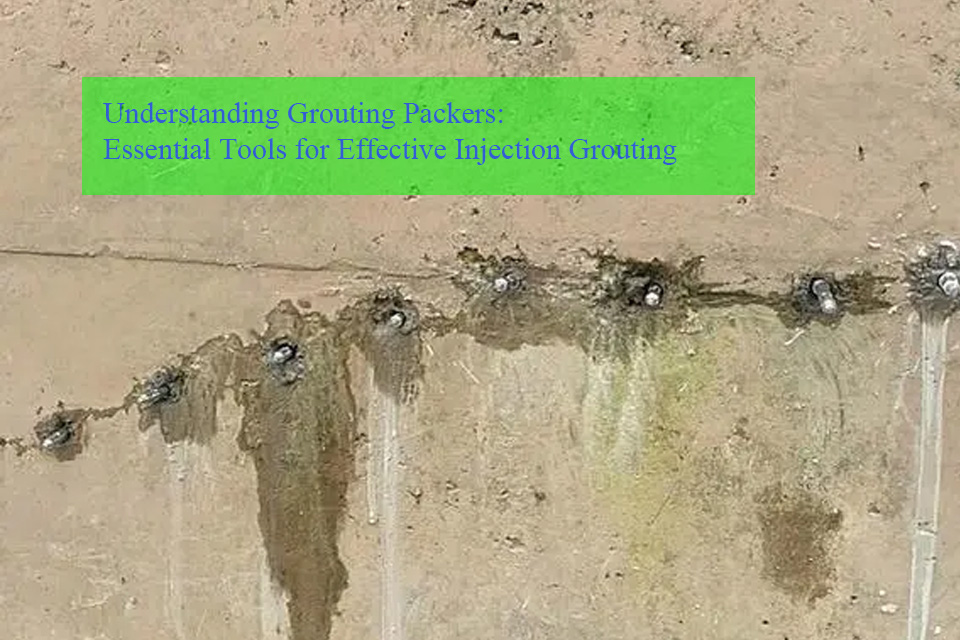
Understanding Grouting Packers: Essential Tools for Effective Injection Grouting
Injection packers play a vital role in the grouting process, enabling precise injection of grouting materials into cracks, joints, and voids within structures.
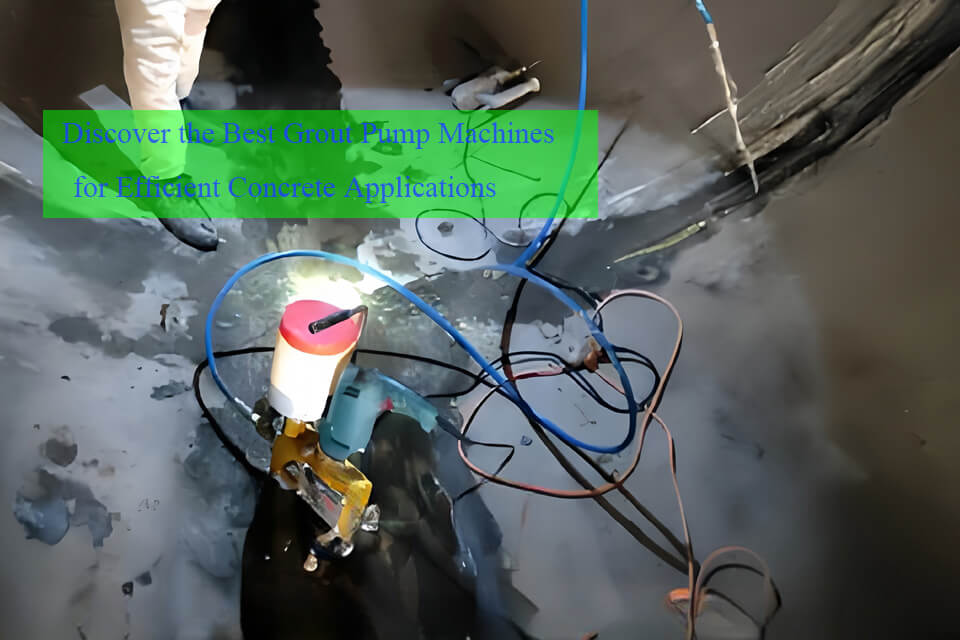
Discover the Best Grout Pump Machines for Efficient Concrete Applications
Grout pump machines are essential tools in construction, helping workers fill gaps and strengthen structures.
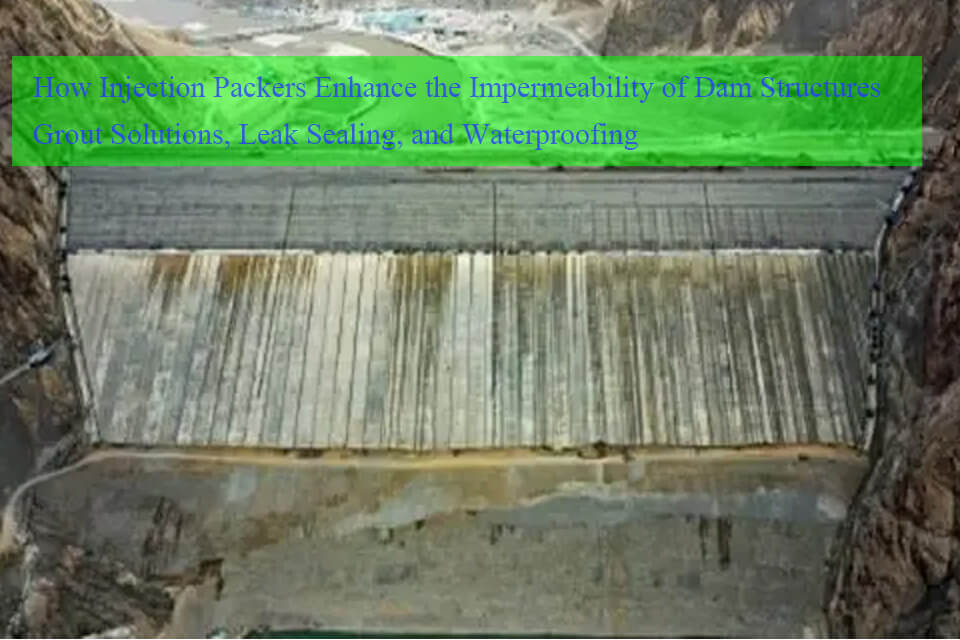
How Injection Packers Enhance the Dam Structures Impermeability
Keeping a dam waterproof is essential for maintaining its structural integrity and preventing water erosion.
- [email protected]
- +86 18157440126
- Mon-Sun 8:00-21:00
Tags
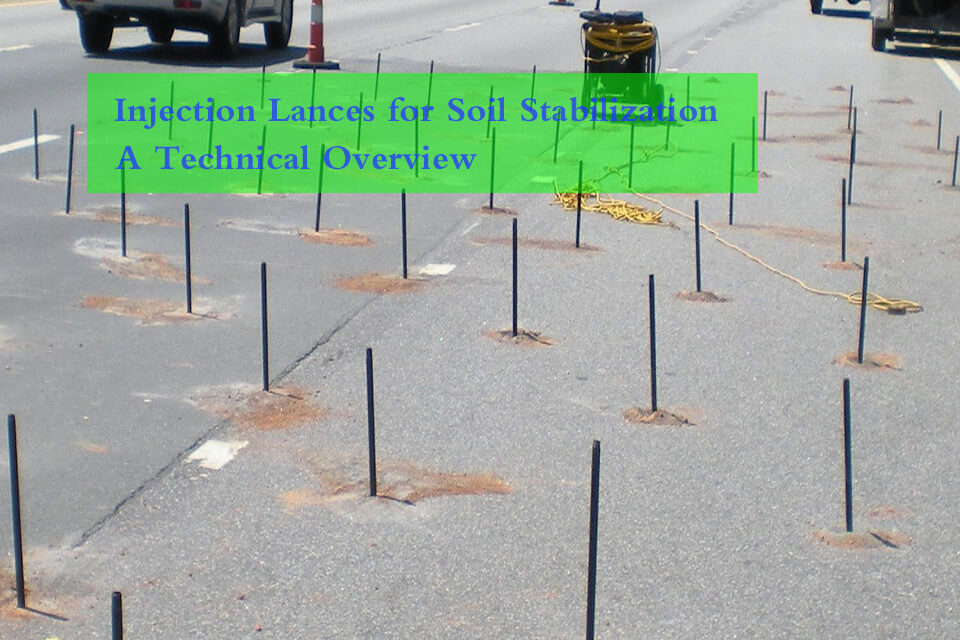
Injection Lances for Soil Stabilization: A Technical Overview
Injection lances are essential tools for soil stabilization and ground reinforcement, designed to improve the structural integrity of the soil by injecting stabilizing agents at precise depths.
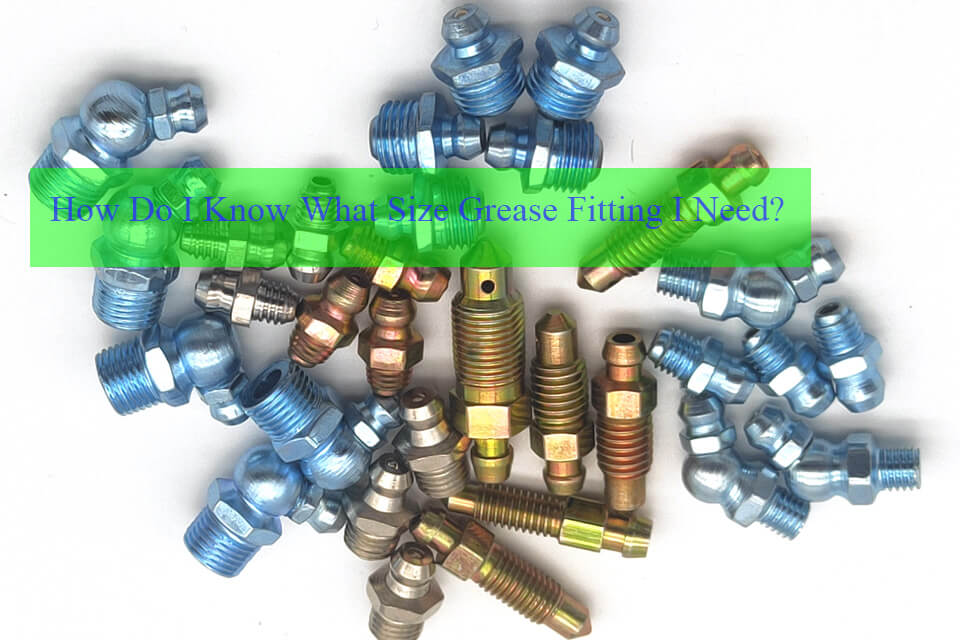
How Do I Know What Size Grease Fitting I Need?
Grease fittings are small but crucial components in machinery maintenance, helping keep equipment running smoothly by allowing grease to reach vital parts.
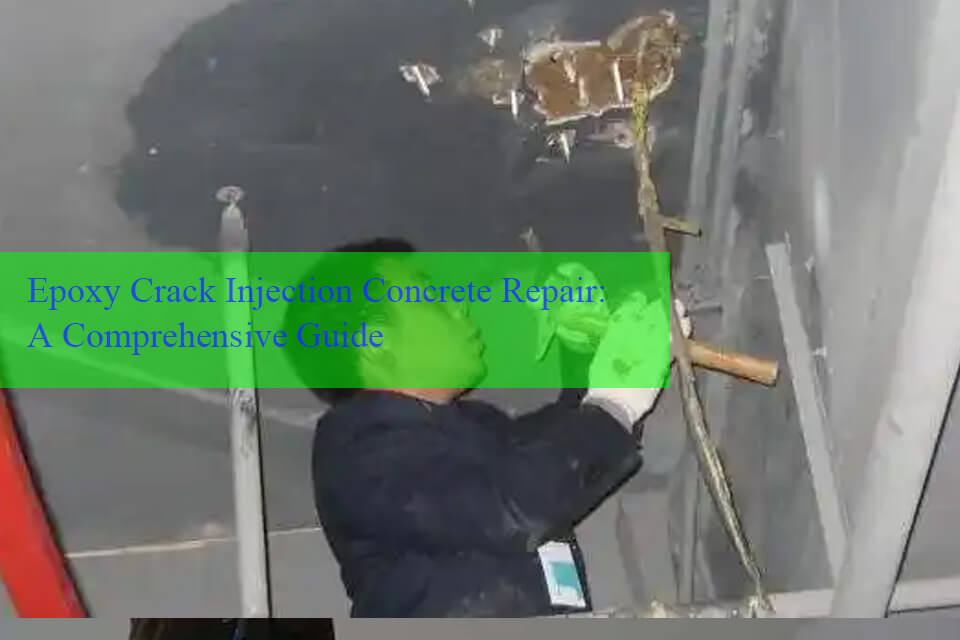
Comprehensive Guide of Epoxy Crack Injection Concrete Repair
Epoxy crack injection is a reliable and scientifically advanced method for repairing concrete structures, particularly those suffering from cracks.