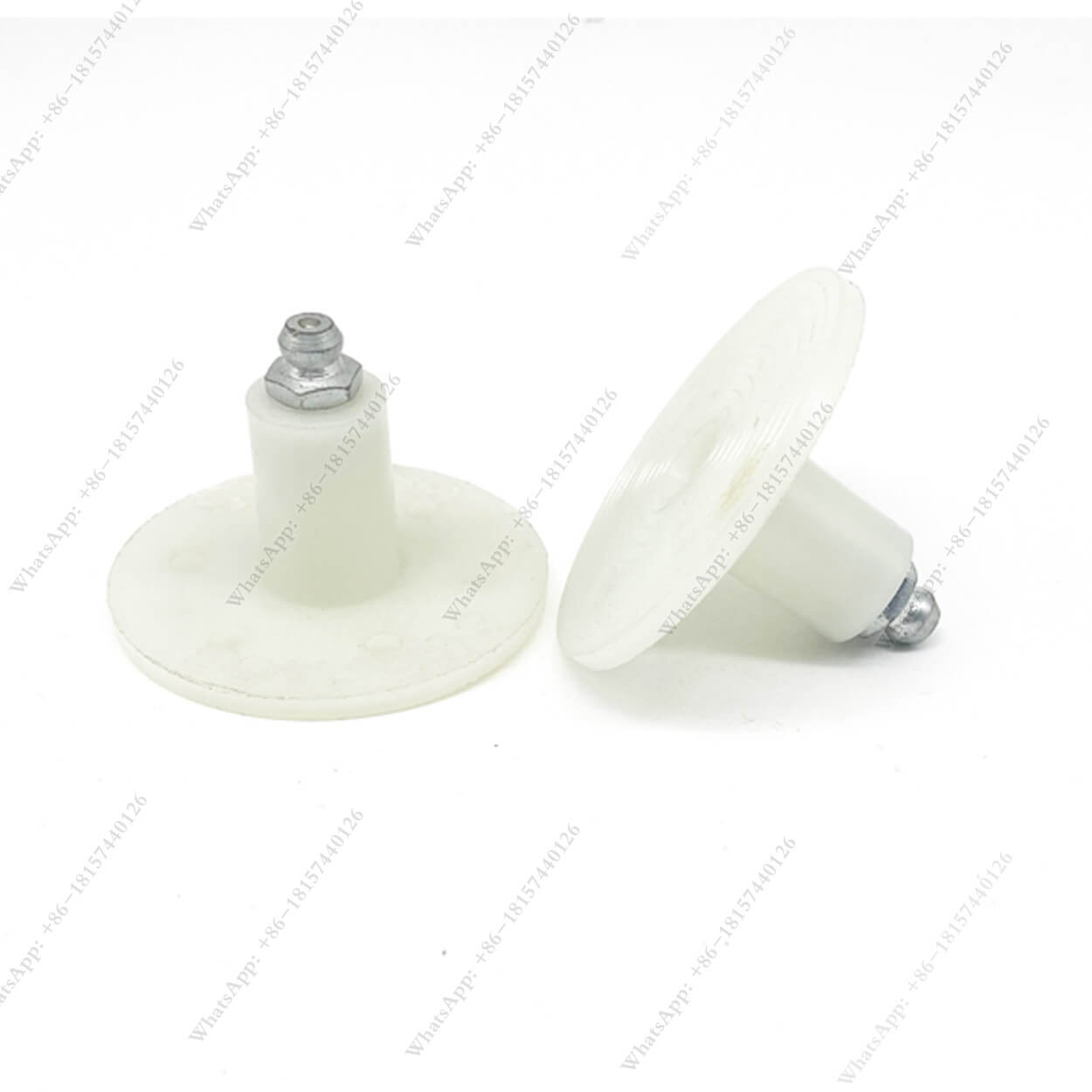
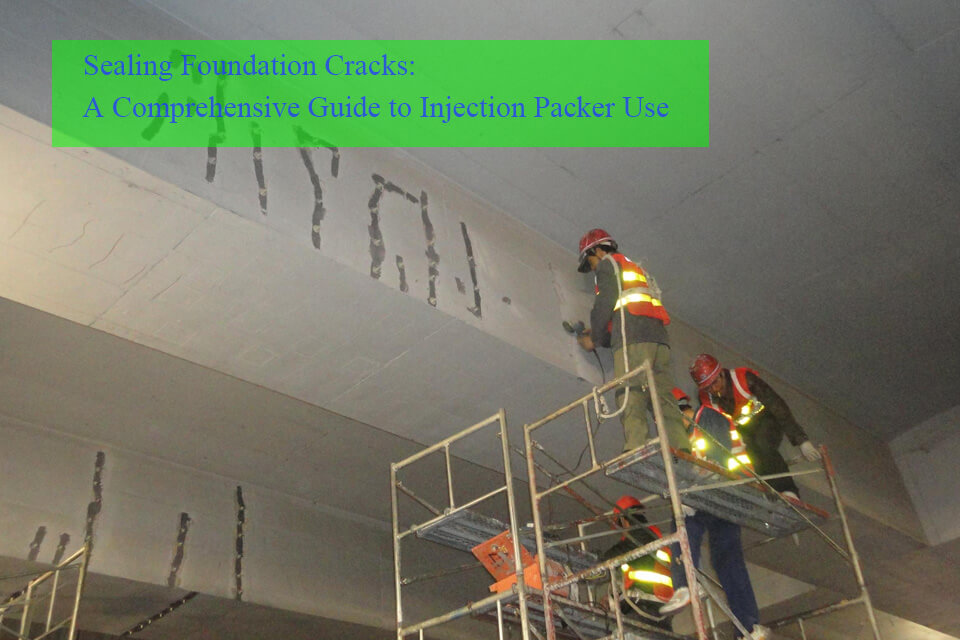
Sealing Foundation Cracks: A Comprehensive Guide to Injection Packer Use
Foundation cracks are a homeowner’s nightmare, potentially leading to structural damage, water leaks, and costly repairs.
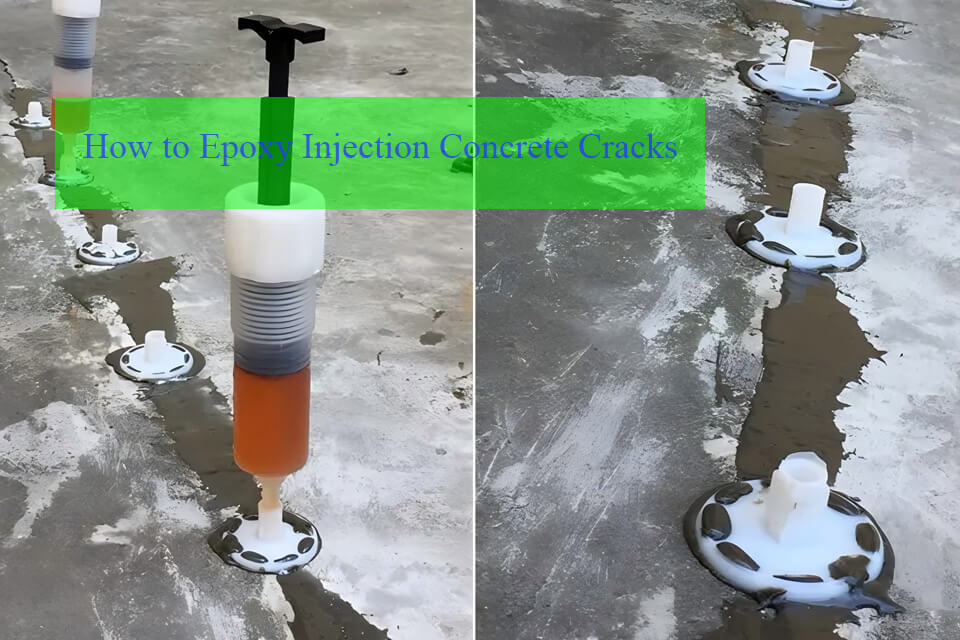
How to Epoxy Injection Concrete Cracks: A Comprehensive Guide
Concrete structures are prone to cracking over time due to various factors such as natural settling, temperature changes, and heavy loads.
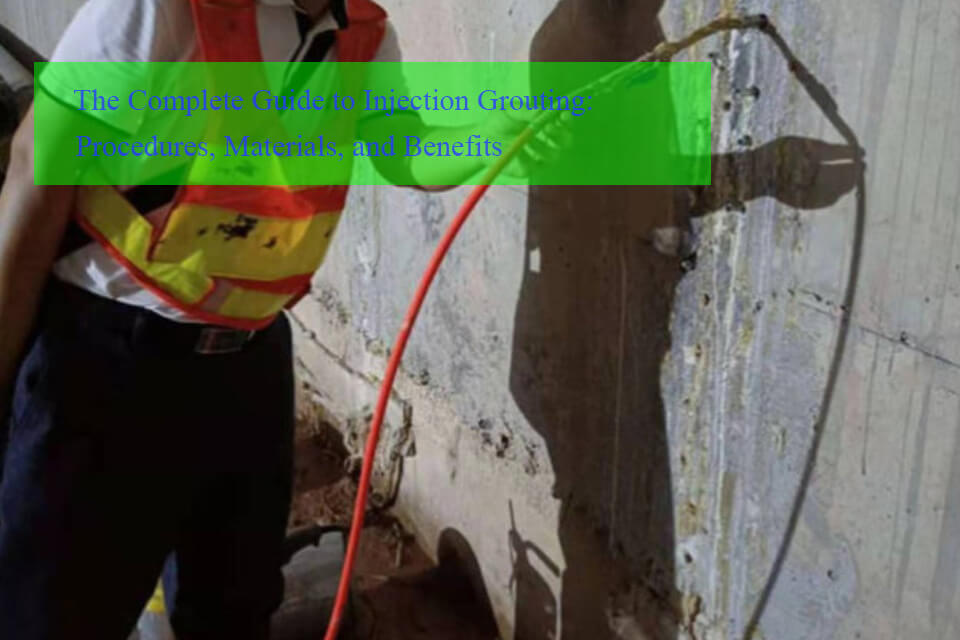
What is the Injection Grouting Procedure? A Detailed Guide to Concrete and Masonry Repairs
Injection grouting is a crucial technique used in construction and maintenance for repairing and reinforcing concrete and masonry structures.