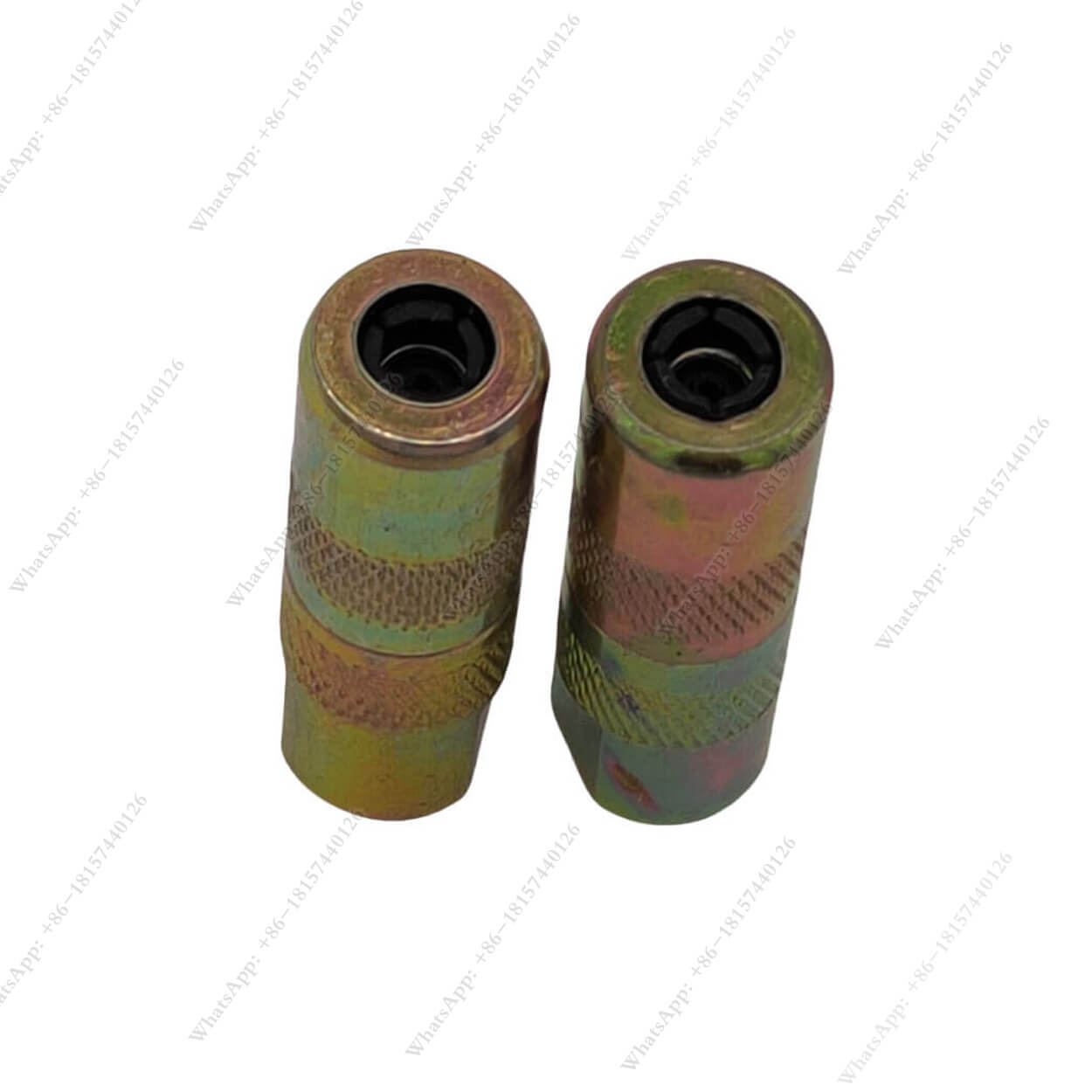
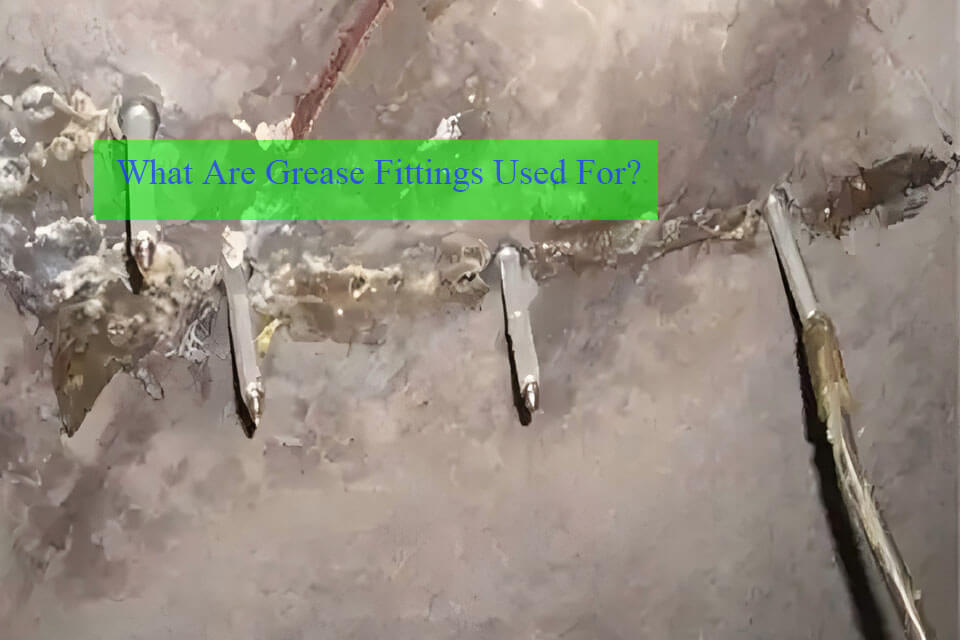
What Are Grease Fittings Used For?
Grease fittings, also known as zerk fittings, are small but critical components in the world of machinery maintenance and waterproof industry.
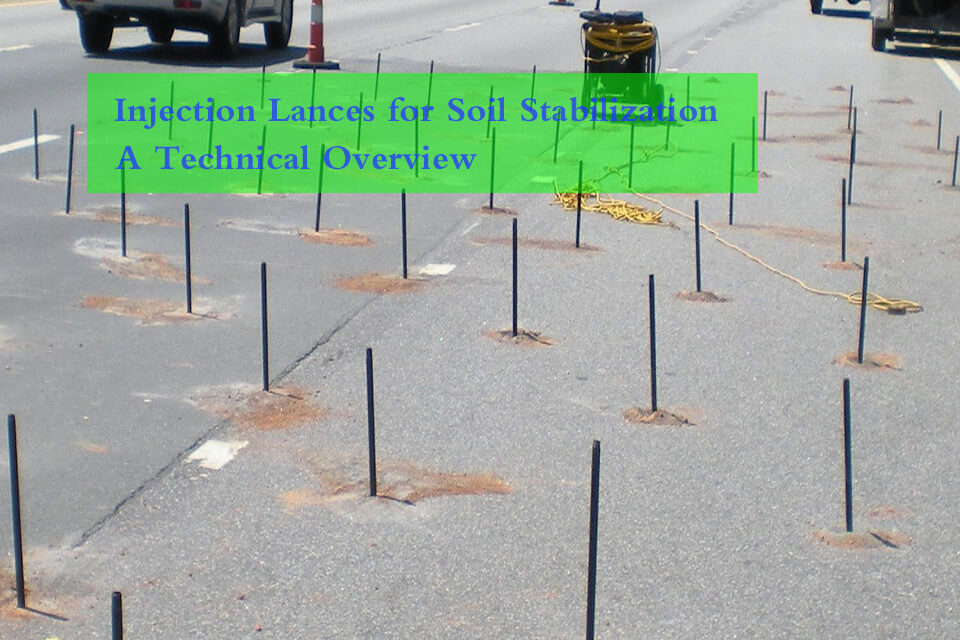
Injection Lances for Soil Stabilization: A Technical Overview
Injection lances are essential tools for soil stabilization and ground reinforcement, designed to improve the structural integrity of the soil by injecting stabilizing agents at precise depths.
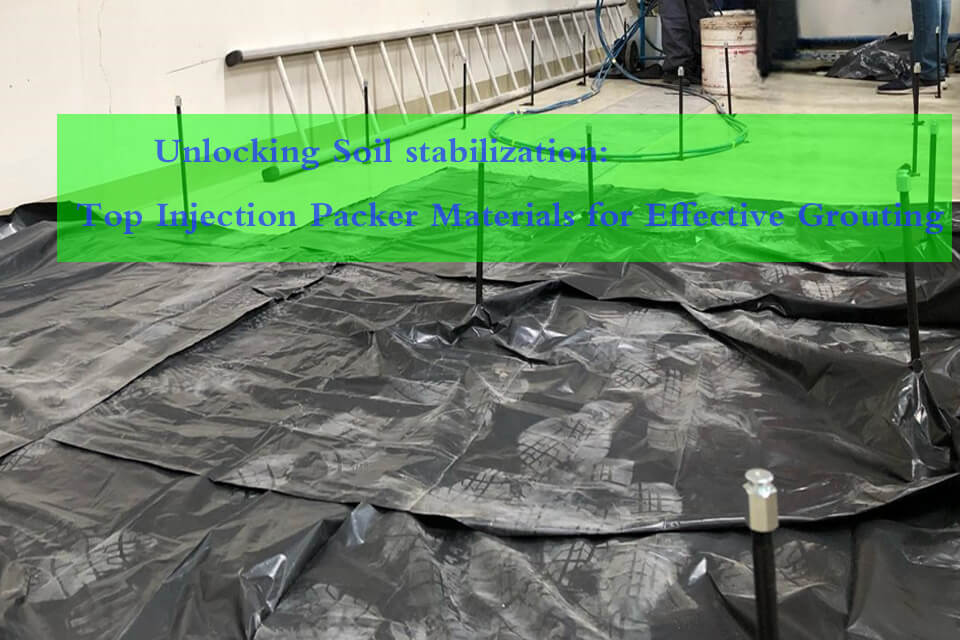
Unlocking the Secrets of Soil Stabilization: A Comprehensive Guide
Soil stabilization is a crucial process in construction and civil engineering that can make or break a project’s success.