Chemical Grouting for Soil Stabilization: A Complete Guide to the Process and Benefits
Table of Contents
Chemical Grouting for Soil Stabilization
This article provides a step-by-step guide to the chemical grouting process, exploring its various types, benefits, and practical applications. Whether you’re a property owner, contractor, or engineer, understanding chemical grouting can offer significant advantages for projects involving foundation repair or void filling. Dive in to learn everything you need to know about this essential technique.
What Is Chemical Grouting and How Does It Work?
Chemical grouting is a technique for soil stabilization that involves injecting chemical grout into the soil or rock to solidify the ground. The process effectively reduces soil permeability, increases strength, and fills voids that might otherwise compromise the integrity of structures. This method is commonly used to support foundations, control water flow, and address soil erosion.
The materials used in chemical grouting vary depending on the specific needs of the project. Polyurethane, acrylate, and epoxy grouts are popular choices due to their versatile applications and strong binding properties. As the grout flows into soil pores or cracks, it creates a solid, water-resistant mass that stabilizes the surrounding area.
Why Is Chemical Grouting Used Today in Soil Stabilization?
Chemical grouting is a versatile and cost-effective solution for soil stabilization. Its ability to reduce permeability and improve load-bearing capacity makes it essential in construction projects where soil quality is poor or where water infiltration is a concern.
In situations where traditional compaction techniques may not be feasible, chemical grouting provides an alternative by improving soil without the need for excavation. This minimizes disruptions to nearby structures and saves time and labor costs.
Different Types of Chemical Grouting Explained
There are several types of chemical grouts, each suited for different applications:
- Permeation Grouting: Used to fill the gaps between soil particles without disturbing them.
- Compaction Grouting: Involves injecting grout to compact loose soil and enhance its density.
- Polyurethane Grouting: Ideal for water control due to its high resistance to moisture.
Each type has specific benefits, so it’s essential to select the right grout for your soil stabilization project based on your structural and environmental needs.
The Chemical Grouting Process: Step-by-Step Guide
The chemical grouting process generally follows these steps:
- Site Assessment: Soil is evaluated to determine the appropriate grouting solution.
- Preparation: Drilling holes into the ground to access the treatment area.
- Injection: Chemical grout is injected under pressure, filling voids and solidifying soil.
- Curing: The grout hardens, stabilizing the ground.
This step-by-step method ensures the stability and integrity of treated areas, making them suitable for construction and long-term durability.
Understanding Permeation Grouting for Soil Reinforcement
Permeation grouting involves injecting a low-viscosity grout, like a cement-based solution, into the soil. This grout permeates between soil particles without displacing them, filling voids and creating a denser, less permeable soil structure.
This type of grouting is especially useful for groundwater control and soil reinforcement under foundations. Permeation grouting is typically applied in areas where precise control over soil stability is required, as it provides long-term strength and water resistance.
Compaction Grouting vs. Chemical Grouting: Key Differences
While compaction grouting and chemical grouting both stabilize soil, they differ in approach and application. Compaction grouting is a displacement technique where the grout compacts loose soil around the injection point. In contrast, chemical grouting permeates the soil without displacing it, making it ideal for situations requiring minimal disturbance.
Understanding these differences is essential for choosing the best method based on your project requirements. Compaction grouting is suited for areas needing high load-bearing capacity, while chemical grouting offers permeability reduction and increased cohesion.
Benefits of Chemical Grouting for Construction and Repair Projects
Chemical grouting offers several advantages:
- Enhanced Soil Strength: Increases load-bearing capacity.
- Water Control: Creates a water-resistant barrier, useful in groundwater management.
- Versatility: Suitable for various soil types and structural needs.
Using chemical grouting can help extend the lifespan of structures by preventing soil erosion, addressing foundation cracks, and providing support for excavations and construction.
Applications of Chemical Grouting in Structural Engineering
Chemical grouting is widely used in construction, civil engineering, and underground projects. Common applications include:
- Foundation Repair: Provides additional stability to aging structures.
- Tunnel Sealing: Prevents water ingress in tunnels and other underground spaces.
- Slope Stabilization: Protects against landslides in hilly or unstable areas.
These applications showcase the adaptability of chemical grouting in various environments, from urban infrastructure projects to remote, challenging sites.
How to Choose the Right Grouting Solution for Your Needs
Selecting the best chemical grout requires consideration of soil composition, environmental factors, and structural requirements. Different grouts offer distinct benefits, so consulting with experts can help tailor a solution to fit your needs.
For instance, polyurethane grouts are ideal for high-moisture areas, while epoxy grouts are favored for their strength and durability. Analyzing these factors helps ensure that the chosen grouting solution will effectively support your project.
Contact Us Today for Expert Grouting Services
For expert advice and customized grouting solutions, contact us today. Our team has extensive experience in soil stabilization, void filling, and foundation repair. We’re here to help you navigate the complexities of chemical grouting and ensure your project’s success with our professional grouting tools.
Conclusion:Key Takeaways on Chemical Grouting
- Versatile Solution: Suitable for soil stabilization, foundation support, and water control.
- Multiple Grout Types: Choose from permeation, compaction, and polyurethane grouting for specific needs.
- Cost-Effective: Reduces excavation and labor, saving time and expenses.
- Long-Lasting Benefits: Increases soil stability, reduces permeability, and enhances structural integrity.
For more information on how chemical grouting can benefit your project, feel free to reach out and get started with a tailored solution.
Comments
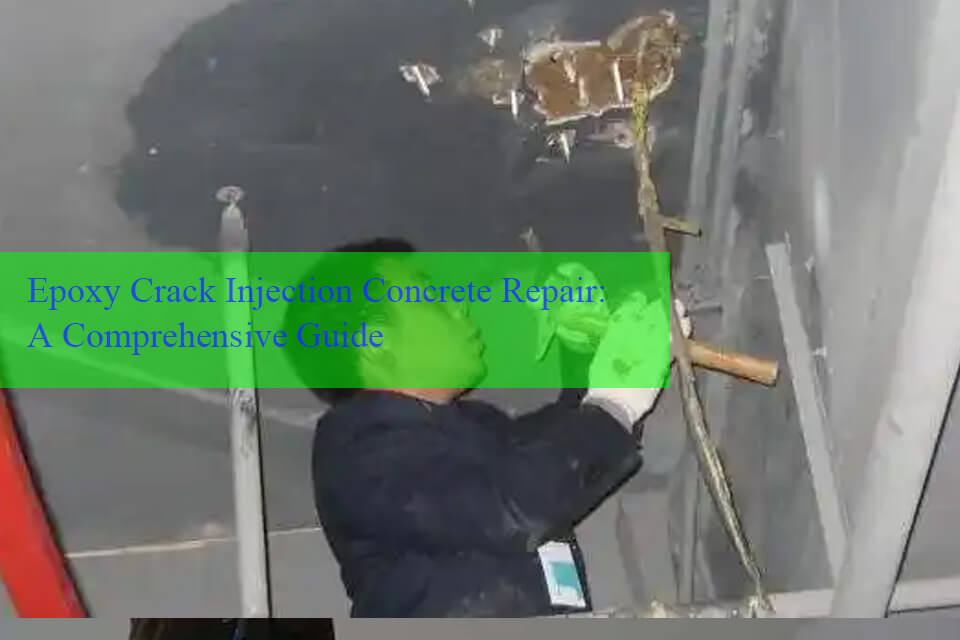
Comprehensive Guide of Epoxy Crack Injection Concrete Repair
Epoxy crack injection is a reliable and scientifically advanced method for repairing concrete structures, particularly those suffering from cracks.
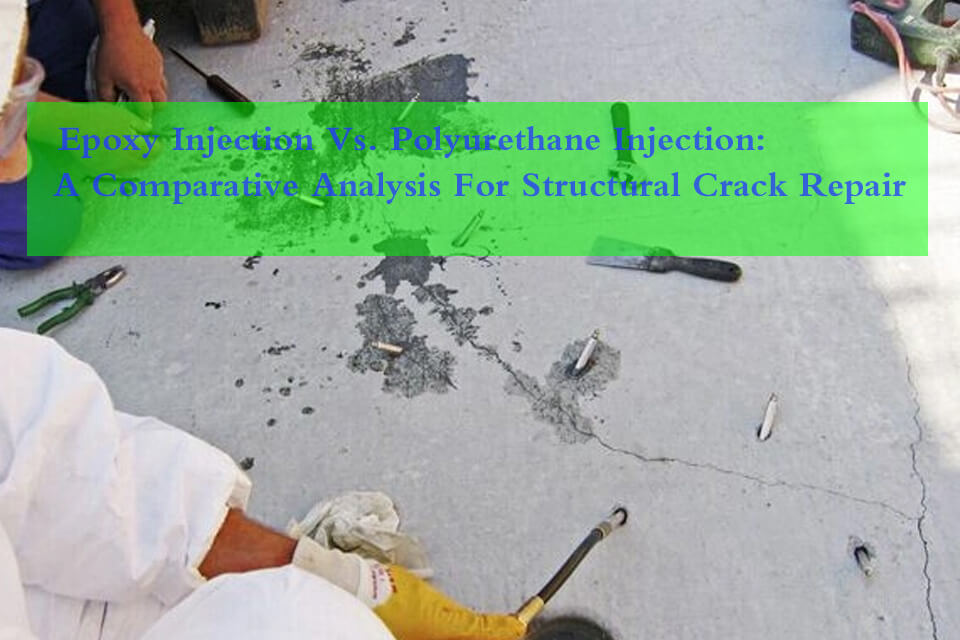
Epoxy Injection vs. Polyurethane Injection: A Comparative Analysis for Structural Crack Repair
Epoxy injection and polyurethane injection are two widely used methods for repairing cracks in concrete structures, each distinguished by its unique chemical properties and applications.
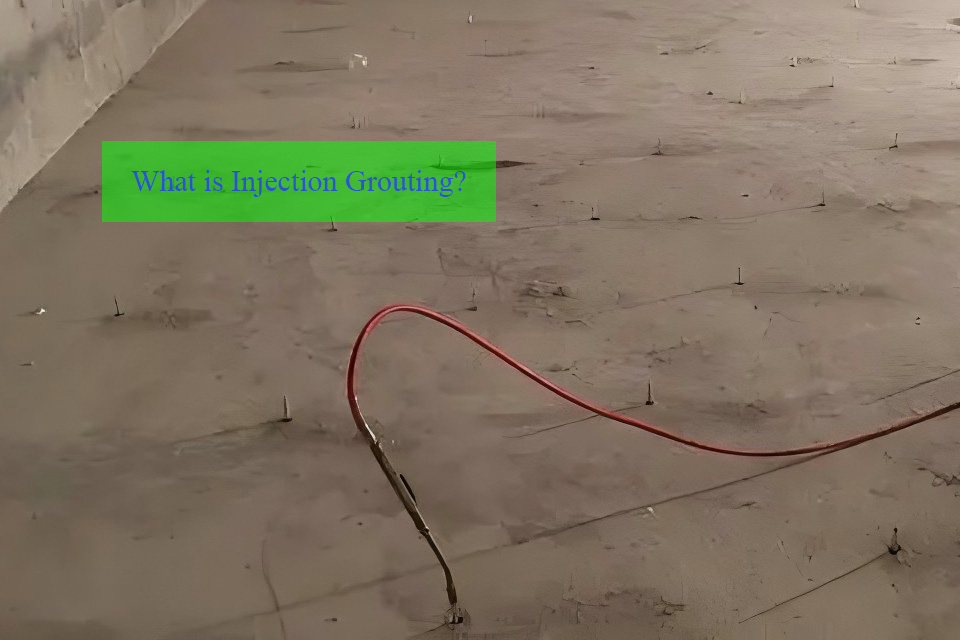
What is Injection Grouting? A Comprehensive Guide to its Benefits, Techniques, and Applications
Injection grouting is an essential process in construction and civil engineering, used to strengthen structures, waterproof surfaces, and fill voids.
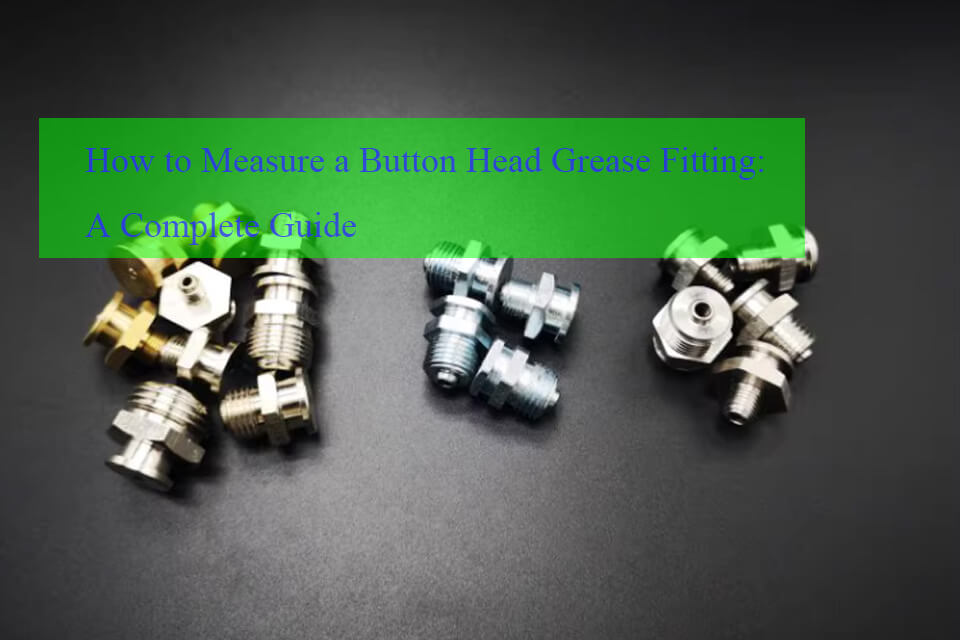
How to Measure a Button Head Grease Fitting: A Complete Guide
Button head grease fittings are widely used in heavy machinery and industrial applications, ensuring that grease is delivered effectively to vital components.
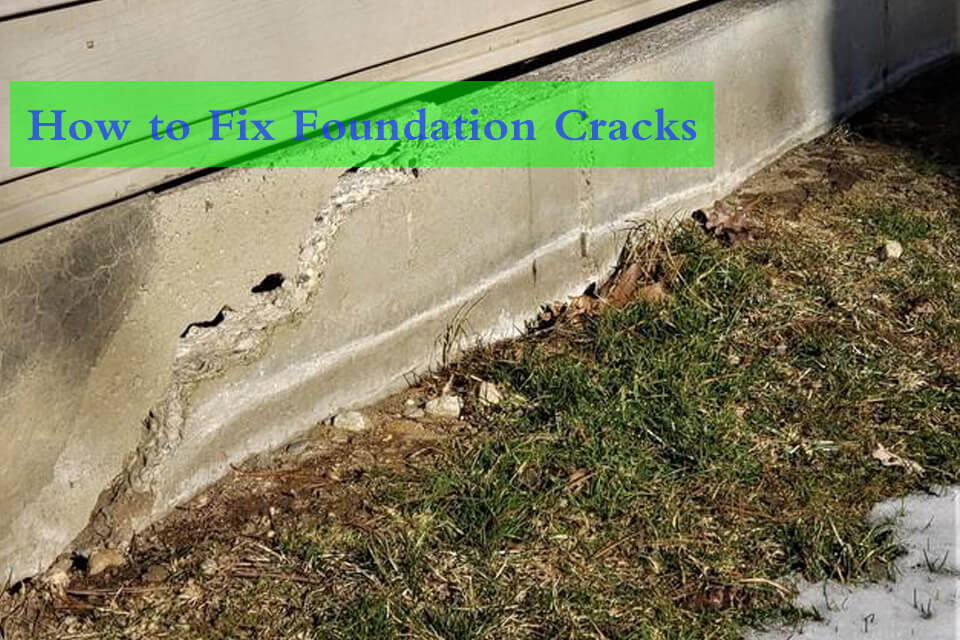
How to Fix Foundation Cracks: A Comprehensive Guide
Foundation cracks can jeopardize the structural integrity of any building, posing a risk to both property and safety.
- [email protected]
- +86 18157440126
- Mon-Sun 8:00-21:00
Tags
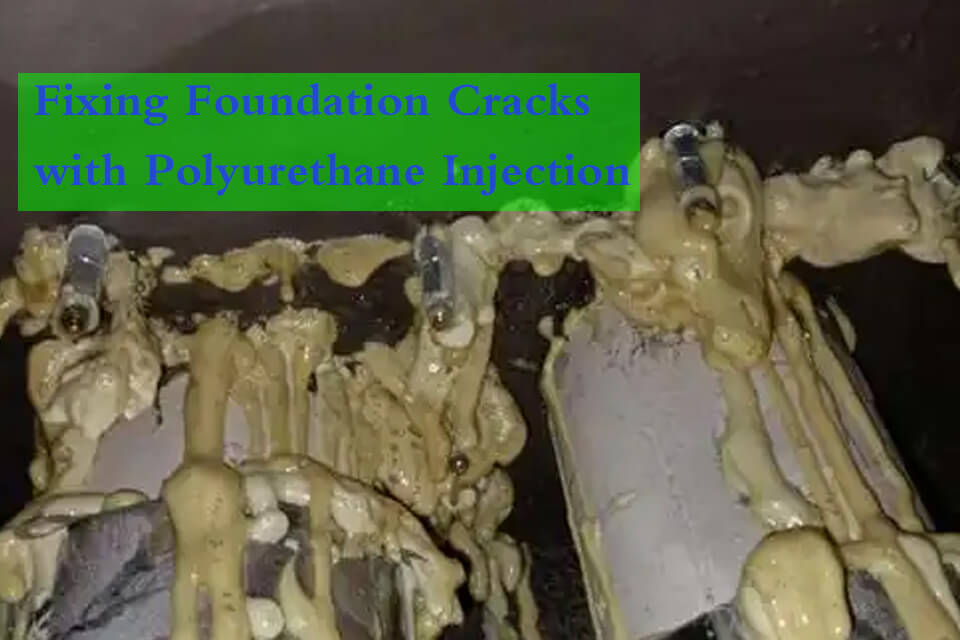
Comprehensive Overview of Polyurethane Crack Injection
Polyurethane crack injection is a versatile and highly effective method for sealing cracks in concrete structures.
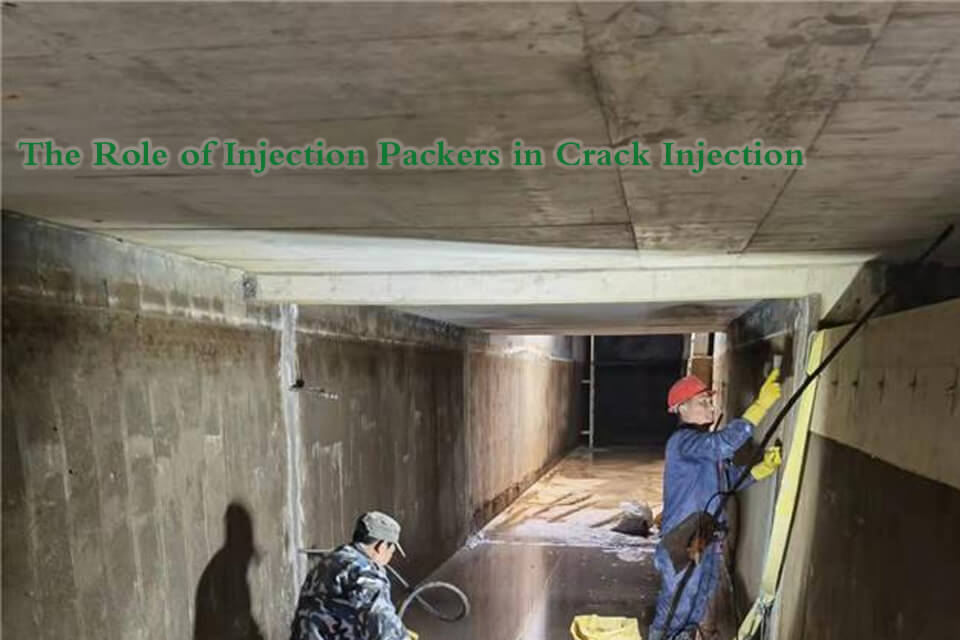
The Role of Injection Packers in Crack Injection and Structural Repair
Crack injection is a critical method used in the restoration and strengthening of concrete structures. It involves injecting an adhesive chemical grout or resin into the cracks of a foundation, slab, or wall to seal and restore structural integrity.
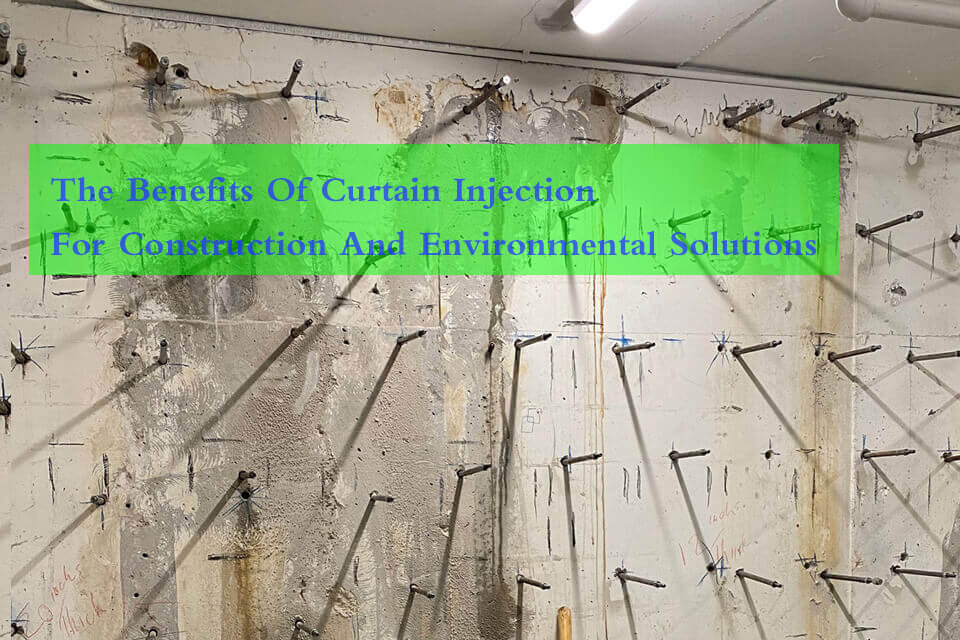
The Benefits of Curtain Injection for Construction and Environmental Solutions
Curtain injection, also known as curtain grouting or curtain wall injection, is an innovative technique widely used in construction, geotechnical engineering, and environmental protection.