Are There Different Size Grease Couplers? A Guide to Finding the Right Fit for Your Equipment
Table of Contents
Summary
From industrial machines to farm tractors and waterproofing industry, understanding grease couplers sizes and compatibility is crucial for anyone involved in equipment maintenance and crack injection. This guide will dive deep into different grease coupler sizes, types, and applications, helping you make the best choice for your tools and equipment. Whether you’re a mechanic or a DIY enthusiast, this article will provide insights into how to choose the right grease coupler for your needs.
What is a Grease Coupler?
A grease coupler is a small tool attached to the end of a grease gun and injection pump used to connect the grease gun to a grease fitting, also known as a zerk fitting. This coupler forms a seal over the grease fitting, allowing lubricant to be pumped directly into the machinery part without leaking. Couplers come in various designs, some with quick-release mechanisms, others built for high-pressure applications, to make grease application easier and cleaner.
Grease couplers are widely used in industries that require regular equipment maintenance, like construction, agriculture, and automotive repair. These tools make it possible to reach hard-to-access fittings and ensure that each part receives the necessary lubrication for optimal operation.
Why Are Grease Couplers Sizes Important?
Choosing the correct grease couplers size is crucial for efficient lubrication and effective maintenance. The wrong size may lead to improper sealing, resulting in leaks or under-lubrication. Here’s why size matters:
- Proper Sealing: The correct coupler size ensures a tight fit, preventing grease from leaking and ensuring all lubricant is delivered into the machinery.
- Efficiency: With the right coupler size, lubrication becomes quicker and easier, saving time and effort.
- Compatibility: Many machines have specific coupler and fitting requirements. Using the correct size ensures compatibility with standard zerk fittingsand other specialized fittings, such as button head fittings.
Common Sizes and Their Uses
- 1/8″ NPT: Commonly used in the automotive industry.
- 1/4″ NPT: Often used in industrial and heavy-duty equipment.
- 3/8″ and 1/2″ NPT: Found in larger machinery, typically with high grease requirements.
Comparing Zerk and Button Head Grease Couplers
Zerk fittings and button head fittings are two of the most common types, but they serve different purposes:
- Zerk Fittings: These are small and easy to access, making them ideal for general-purpose applications in automotive and small machinery.
- Button Head Fittings: These fittings are designed for high-pressure and high-volume applications, often found in heavy-duty equipment.
Choosing between these two types depends on your equipment’s requirements. For heavy-duty and construction equipment, button head fittings paired with a compatible grease coupler ensure efficient lubrication under high-pressure conditions.
Standard Sizes for Grease Fittings and Couplers
There are standard grease fitting and coupler sizes to ensure compatibility across a variety of tools and equipment. These are the most commonly used sizes:
Fitting Type | Standard Size (NPT) | Typical Applications |
Zerk Fittings | 1/8″ and 1/4″ | Automotive, general-purpose machinery |
Button Head | 3/8″ and 1/2″ | Heavy-duty, construction equipment |
Flush Fittings | 1/8″ | Low-profile machinery, hard-to-access areas |
Selecting the correct size ensures that your grease gun and fittings work effectively together, providing a secure and reliable connection
How to Choose the Right Grease Gun Coupler for Your Equipment
Choosing the right grease gun coupler involves evaluating several factors:
- Fitting Size: Determine if your equipment uses standard zerk fittings or larger button head fittings.
- Pressure Rating: Some applications require high-pressure couplers to avoid leaks or failure under stress.
- Coupler Design: Quick-release couplers make it easier to switch between fittings, while standard couplers work well for general-purpose use.
Considering these aspects can help ensure that you have the right coupler for smooth and efficient lubrication.
Advantages of Using High-Quality Grease Couplers
Investing in high-quality grease couplers provides several benefits:
- Durability: High-quality couplers are made from materials like stainless steel, offering long-lasting performance.
- Efficiency: Reliable couplers prevent leaks and ensure smooth grease flow, reducing wasted lubricant.
- Cost Savings: Although quality couplers may cost more upfront, their longevity and efficiency reduce overall maintenance expenses.
Using a high-quality coupler ensures that each lubrication session is efficient and effective, extending the life of both the coupler and your equipment.
Where to Buy Grease Couplers and Cost Considerations
Grease couplers can be purchased from industrial supply stores, automotive retailers, online marketplaces, the best way you can buy from factory directly, please contact us for direct source now. Here’s a quick cost breakdown:
- Standard Couplers: $5 – $10
- Quick-Release Couplers: $15 – $25
- Heavy-Duty Button Head Couplers: $20 – $35
When buying, consider both the quality and type of coupler that will best suit your equipment. For heavy-duty needs, a higher price often reflects better performance and durability.
Summary of Key Points on Grease Coupler Sizes and Selection
- Importance of Fit: Choosing the correct size ensures efficient lubrication and prevents leaks.
- Types and Sizes: From standard zerk couplers to larger button head fittings, each type serves a unique purpose.
- Measurement and Compatibility: Accurately measure fittings and verify compatibility before purchasing a coupler.
- Quality Matters: High-quality couplers save money in the long run by preventing leaks and providing efficient lubrication.
By selecting the right grease coupler size and type, you can ensure your equipment runs smoothly, efficiently, and with minimal maintenance.
Comments
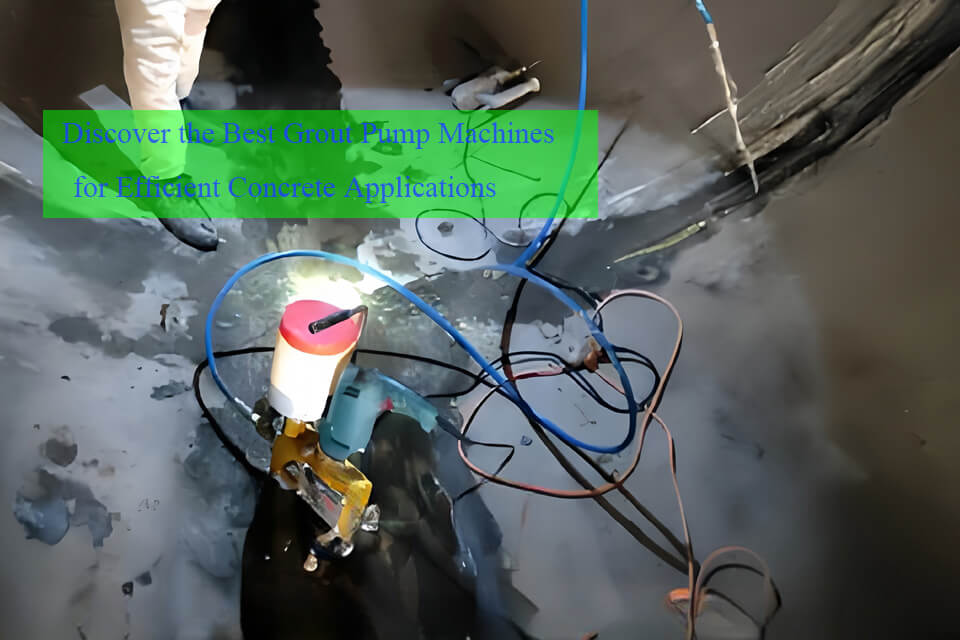
Discover the Best Grout Pump Machines for Efficient Concrete Applications
Grout pump machines are essential tools in construction, helping workers fill gaps and strengthen structures.
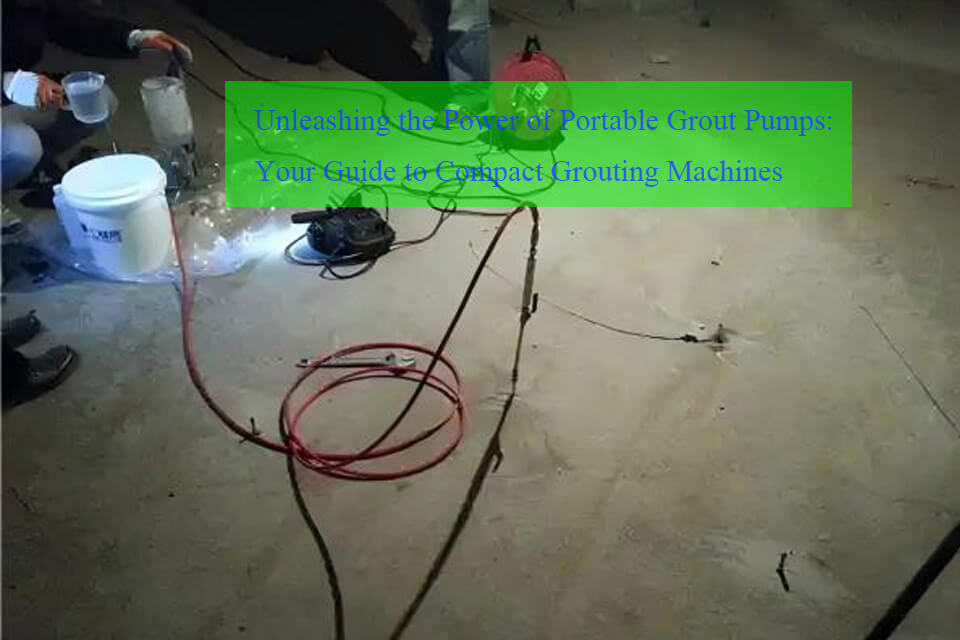
Unleashing the Power of Portable Grout Pumps: Your Guide to Compact Grouting Machines
Looking to tackle a construction project that involves grouting but worried about heavy equipment? Discover how portable grout pumps can revolutionize your work!
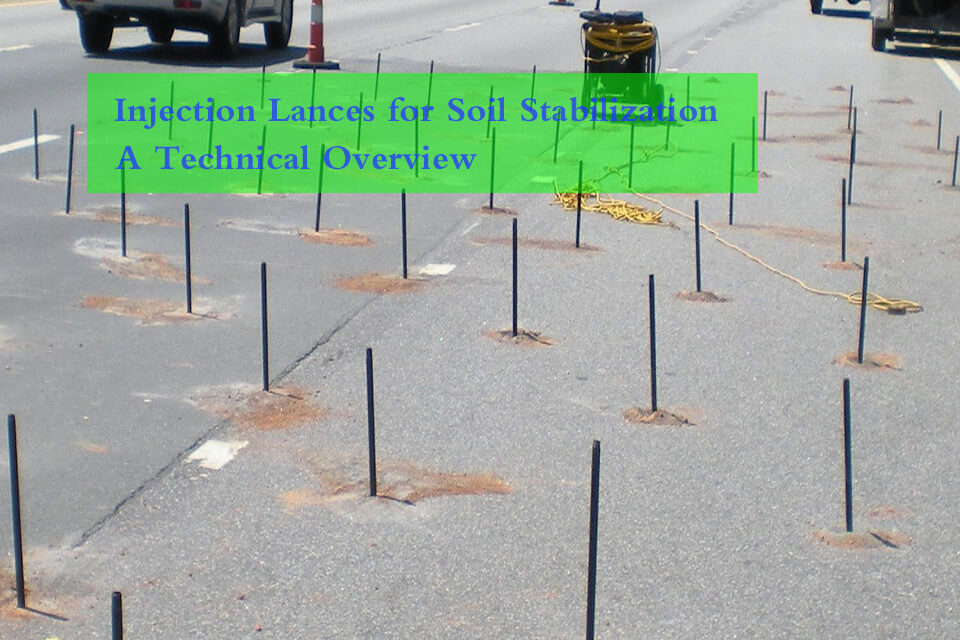
Injection Lances for Soil Stabilization: A Technical Overview
Injection lances are essential tools for soil stabilization and ground reinforcement, designed to improve the structural integrity of the soil by injecting stabilizing agents at precise depths.
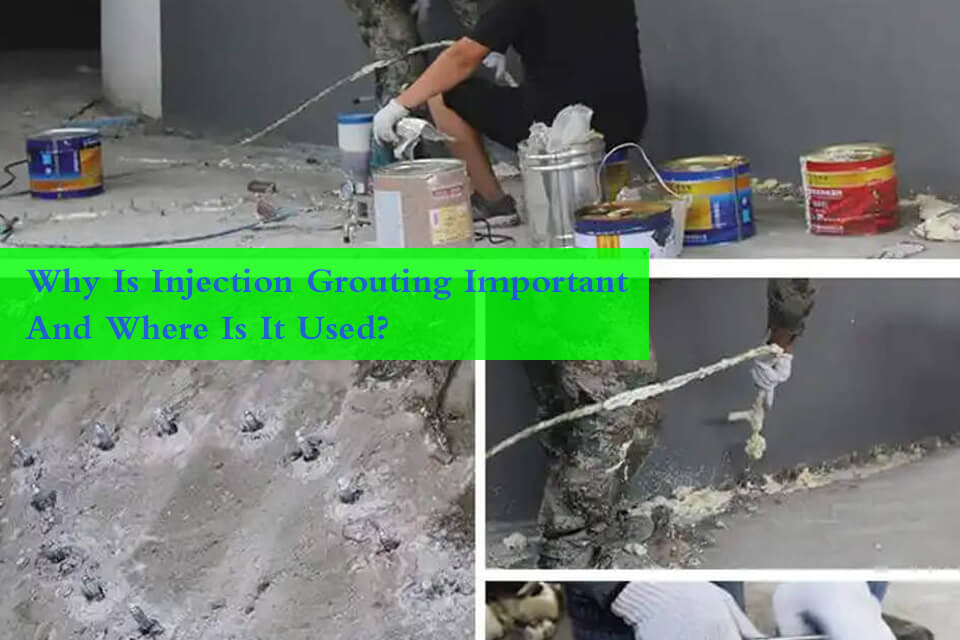
Why Is Injection Grouting Important and Where Is It Used?
Injection grouting is a vital process in construction and repair, designed to enhance the durability and integrity of concrete and masonry structures.
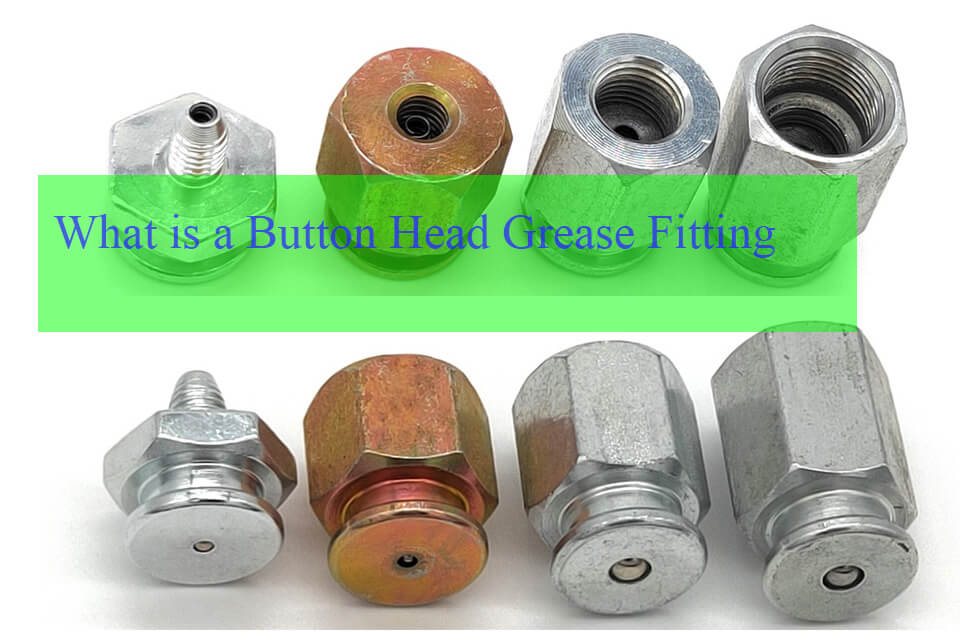
Button Head Grease Fittings: Essential for Construction, Heavy-Duty, and Waterproof Industry Applications
In the world of heavy machinery maintenance, ensuring smooth operation and longevity is essential. One key component that helps achieve this is the button head grease fittings,
- [email protected]
- +86 18157440126
- Mon-Sun 8:00-21:00
Tags
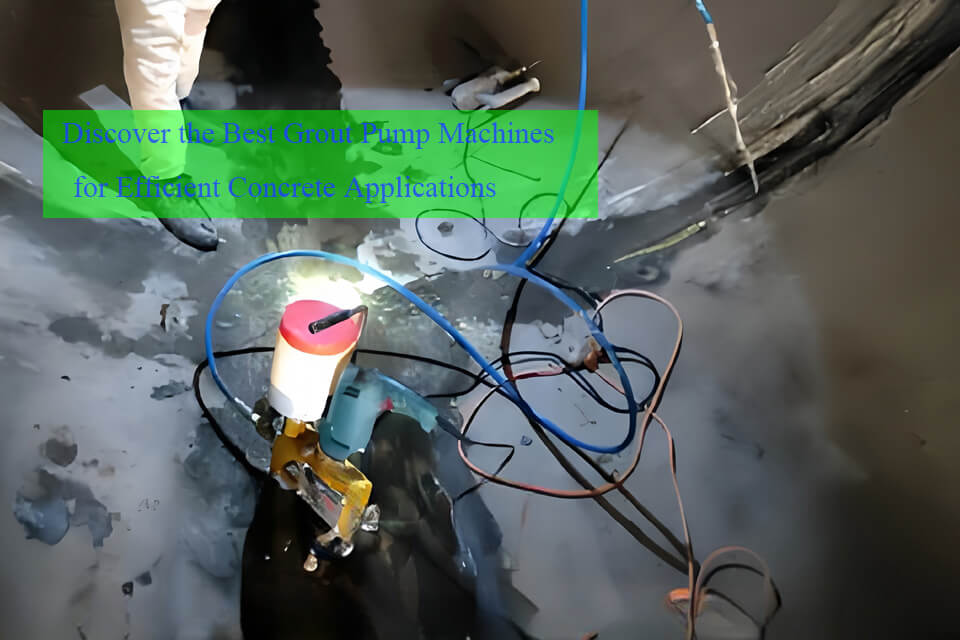
Discover the Best Grout Pump Machines for Efficient Concrete Applications
Grout pump machines are essential tools in construction, helping workers fill gaps and strengthen structures.
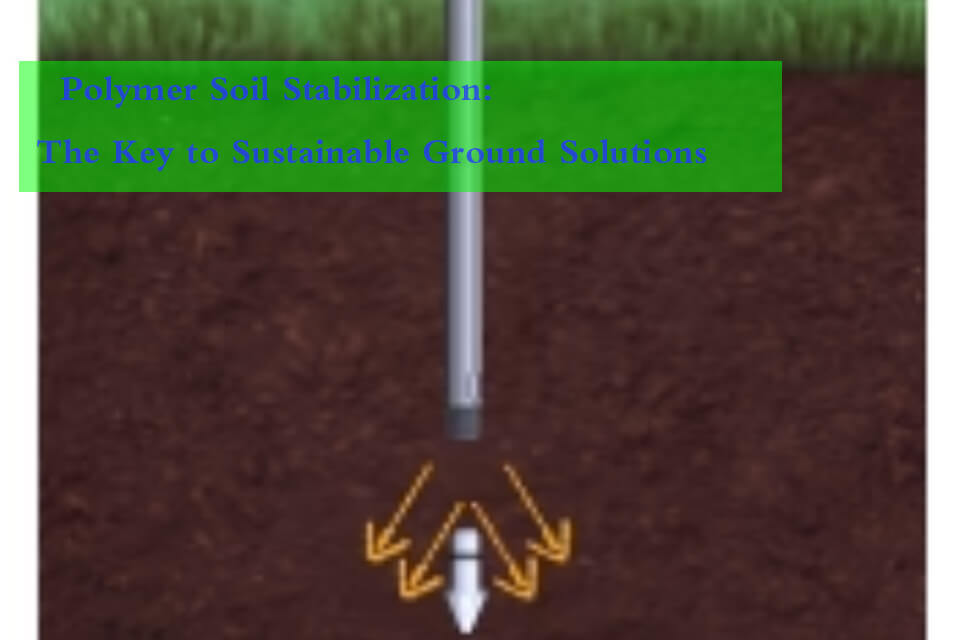
Polymer Soil Stabilization: The Key to Sustainable Ground Solutions
Soil stabilization is vital in construction and civil engineering, particularly for enhancing soil properties and ensuring durable infrastructure.
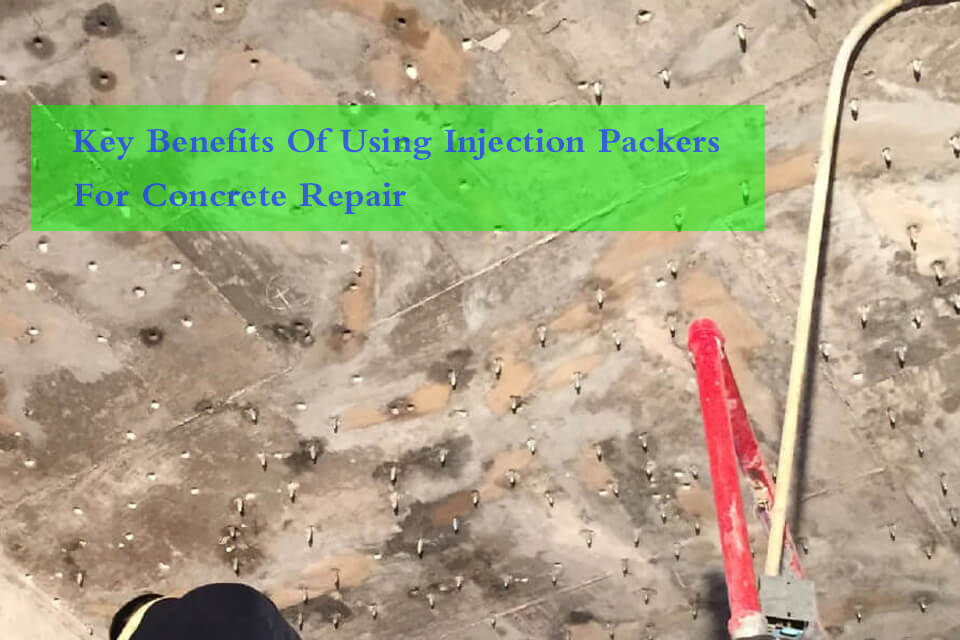
Key Benefits of Using Injection Packers for Concrete Repair
Injection packers are an essential tool for addressing cracks and structural deficiencies in concrete. These devices allow for precise application of repair materials