How Do I Know What Size Grease Fitting I Need?
Table of Contents
Summary
But choosing the correct grease fitting size can be tricky, especially when considering thread types, metric versus SAE standards, and matching the right size to specific machinery. This guide covers everything you need to know about finding the right size grease fitting for your needs. Read on to make informed choices, avoid fitting mismatches, and improve the lifespan of your equipment!
Introduction to Grease Fittings
Grease fittings, also called zerk fittings or grease nipples, are essential for delivering lubrication directly to machine parts. Correctly sized grease fittings help prevent leaks, ensure efficient grease flow, and ultimately, protect machinery from wear and tear. This guide will help you understand the factors behind selecting the right size for your grease fittings.
What is a Grease Fitting?
A grease fitting is a small, threaded metal fitting that allows a grease gun to inject lubricant into machinery without allowing contaminants inside. These fittings come in various sizes, threads, and types, making it essential to select the appropriate one for each application.
Feature | Description |
Purpose | Facilitates lubrication injection into machinery |
Common Types | Standard, flush, button head, angled |
Applications | Bearings, hinges, gears, fifth wheels, and various heavy machinery parts |
Why is Choosing the Right Size Important?
Selecting the right grease fitting size is crucial for several reasons:
- Leak Prevention: A properly sized fitting creates a tight seal, preventing grease from leaking.
- Efficient Lubrication: The right size fitting ensures that grease flows smoothly and reaches critical areas.
- Machinery Longevity: Correctly fitted grease fittings help maintain proper lubrication, reducing wear and tear on parts.
Common Types of Grease Fittings
There are multiple types of grease fittings, each designed for specific applications:
- Standard Grease Fitting: Most common, available in various thread sizes.
- Flush Fitting: Ideal for flush-mount applications where fittings need to be nearly flat.
- Button Head Fitting: Larger head, commonly used in heavy-duty equipment.
- Angled Fitting: Allows access to hard-to-reach spots.
Type | Common Applications | Distinctive Feature |
Standard | General use | Common across various equipment |
Flush | Restricted spaces | Flat surface with no protrusions |
Button Head | Heavy-duty machinery | Larger head for higher grease volumes |
Angled | Hard-to-reach areas | Allows angled lubrication access |
How to Measure Grease Fitting Size
Accurate fitting measurement is essential for proper selection. Follow these steps:
- Identify Thread Type: Use a thread gauge to measure the thread pitch and determine if it’s metric or SAE.
- Measure Diameter: Measure the thread diameter to confirm fitting size.
- Check Thread Length: Ensure that the fitting’s thread length matches the machine’s requirements.
Measurement Step | Tool Needed |
Thread Type | Thread gauge |
Thread Diameter | Caliper |
Thread Length | Ruler or caliper |
Thread Types in Grease Fittings
Grease fittings are typically designed with different thread types to suit a variety of applications:
- NPT (National Pipe Thread): Often used in industrial applications in the U.S.
- BSP (British Standard Pipe): Common in Europe and other regions.
- Metric Threads: Used internationally, especially in newer machinery.
Selecting the correct thread type is essential for compatibility with your machinery.
Metric vs. SAE Fittings: What’s the Difference?
Metric and SAE fittings are differentiated by measurement standards and are not interchangeable. Here’s how to determine which you need:
- SAE (Society of Automotive Engineers): Measured in inches; common in American-made machinery.
- Metric: Measured in millimeters; commonly used in European and Asian equipment.
Type | Measurement Unit | Common Regions |
SAE | Inches | United States, Canada |
Metric | Millimeters | Europe, Asia, and other regions |
Pro Tip: If your equipment manual specifies a certain fitting, always choose that standard for best results.
How to Identify the Right Grease Fitting Thread Size
To identify the correct thread size, you’ll need to measure both thread pitch and diameter:
- Use a Thread Gauge: Measure thread pitch in either SAE or metric, depending on the equipment.
- Measure Thread Diameter: This can be done with a caliper. Confirm whether the diameter matches the specifications of your machinery.
Step | Tool | Measurement Type |
Measure Thread Pitch | Thread gauge | SAE or metric |
Check Diameter | Caliper | Inch or millimeter |
Choosing the Right Grease Gun Fitting
A grease gun fitting is essential for connecting the grease gun to the fitting. Here’s what to consider:
- Compatibility: Ensure the grease gun fitting matches the thread type of the grease fitting.
- Ease of Use: Select a grease gun fitting that is easy to attach and remove.
- Seal Quality: A good fitting provides a leak-proof seal, which is important for efficient lubrication.
FAQs on Grease Fitting Sizes
How can I tell if a grease fitting is metric or SAE?
Check the thread pitch and diameter. Metric fittings are measured in millimeters, while SAE fittings are in inches.
Do I need a special tool to measure grease fitting threads?
A thread gauge and caliper are recommended to accurately measure the thread pitch and diameter.
What happens if I use the wrong size grease fitting?
Using the wrong size can cause leaks, improper lubrication, and even damage to the fitting or machinery.
Summary of Key Points
- Grease fittings, or zerks, are essential for effective machinery lubrication.
- Choosing the correct size, thread type, and standard(SAE or Metric) is crucial for compatibility.
- Measure the thread pitch and diameteraccurately to ensure a proper fit.
- Use the appropriate grease gun fittingfor effective and leak-free lubrication.
- Regular maintenance and checking fittings for wear can extend machinery life and improve performance.
By understanding these essentials, you’ll be equipped to select the right grease fittings for your equipment, helping ensure optimal performance and longevity of your machinery.
Comments
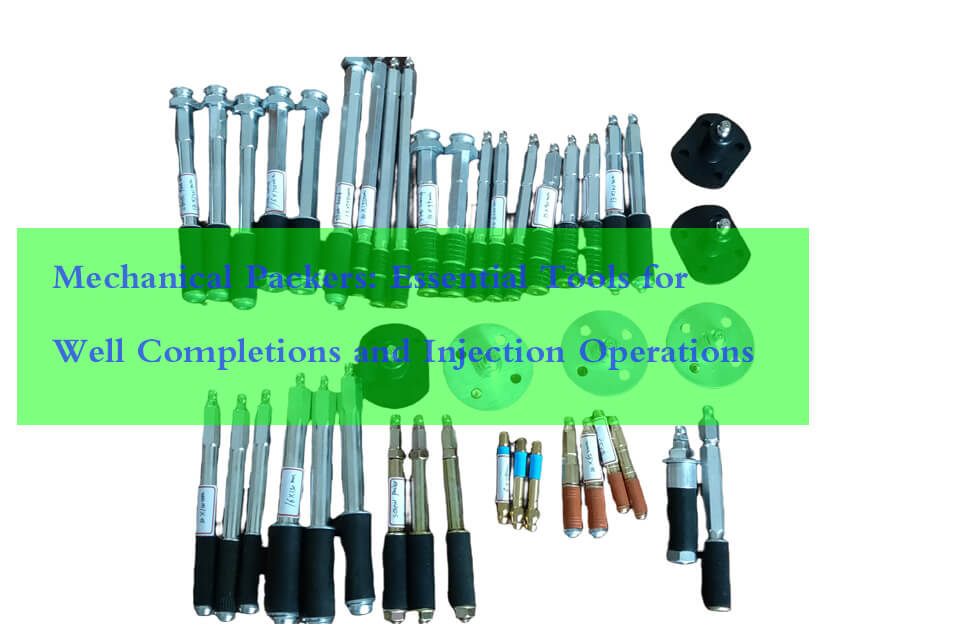
Mechanical Packers: Essential Tools for Well Completions and Injection Operations
Mechanical packers play a crucial role in well completions and injection operations across various industries.
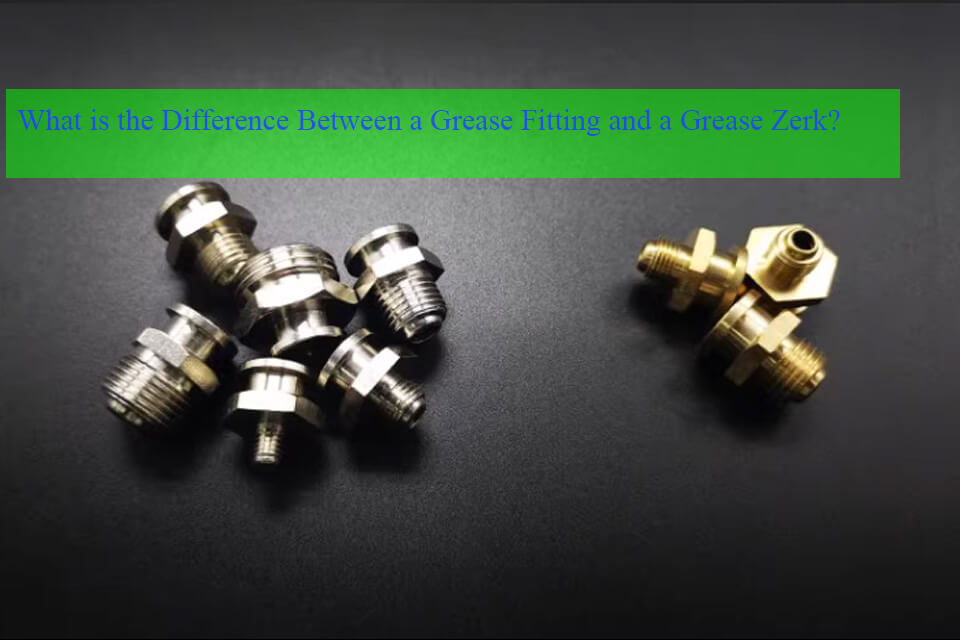
What is the Difference Between a Grease Fitting and a Grease Zerk?
If you’re in the world of machinery maintenance, you’ve likely come across the terms “grease fitting” and “grease zerk.”
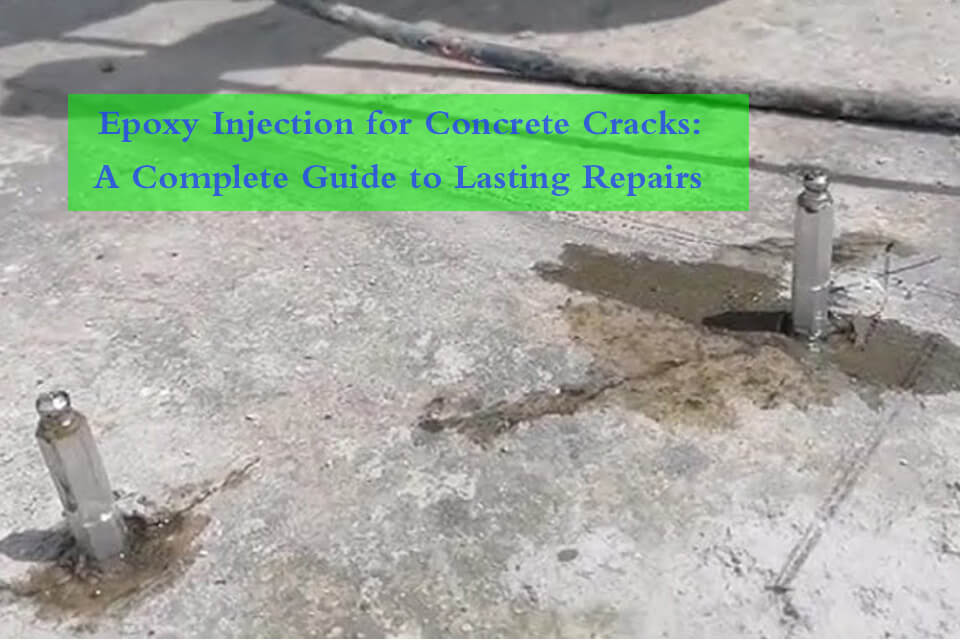
Epoxy Injection for Concrete Cracks: A Complete Guide to Lasting Repairs
In this article, learn how epoxy injection effectively restores structural integrity to cracked concrete, providing a durable, lasting solution.
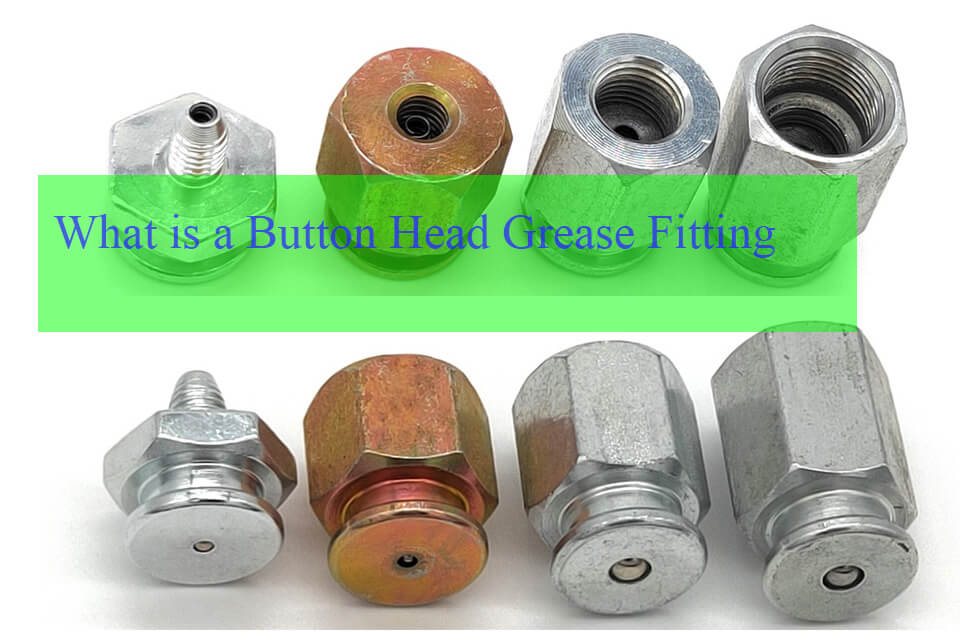
Button Head Grease Fittings: Essential for Construction, Heavy-Duty, and Waterproof Industry Applications
In the world of heavy machinery maintenance, ensuring smooth operation and longevity is essential. One key component that helps achieve this is the button head grease fittings,
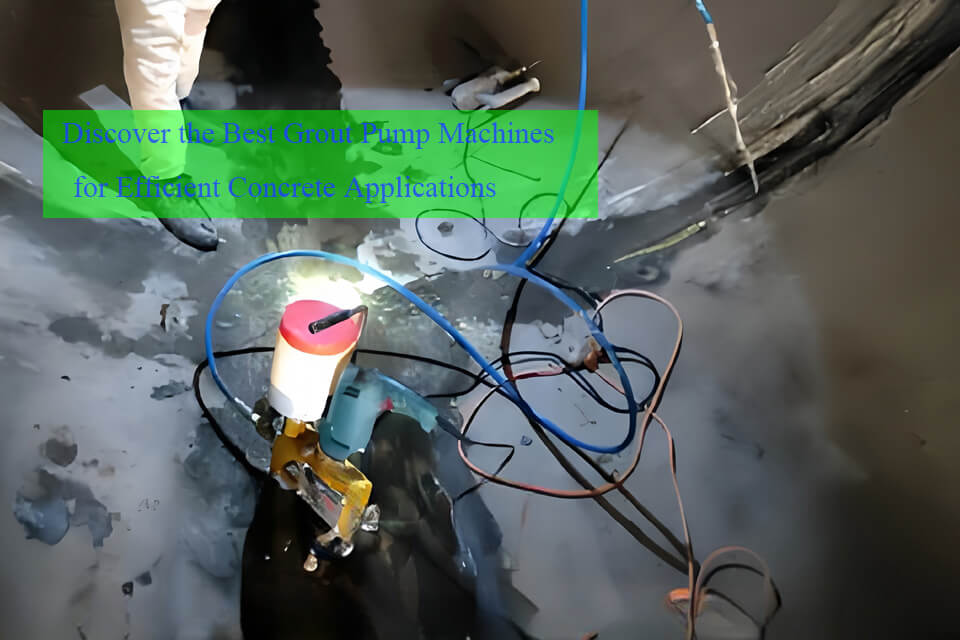
Discover the Best Grout Pump Machines for Efficient Concrete Applications
Grout pump machines are essential tools in construction, helping workers fill gaps and strengthen structures.
- [email protected]
- +86 18157440126
- Mon-Sun 8:00-21:00
Tags
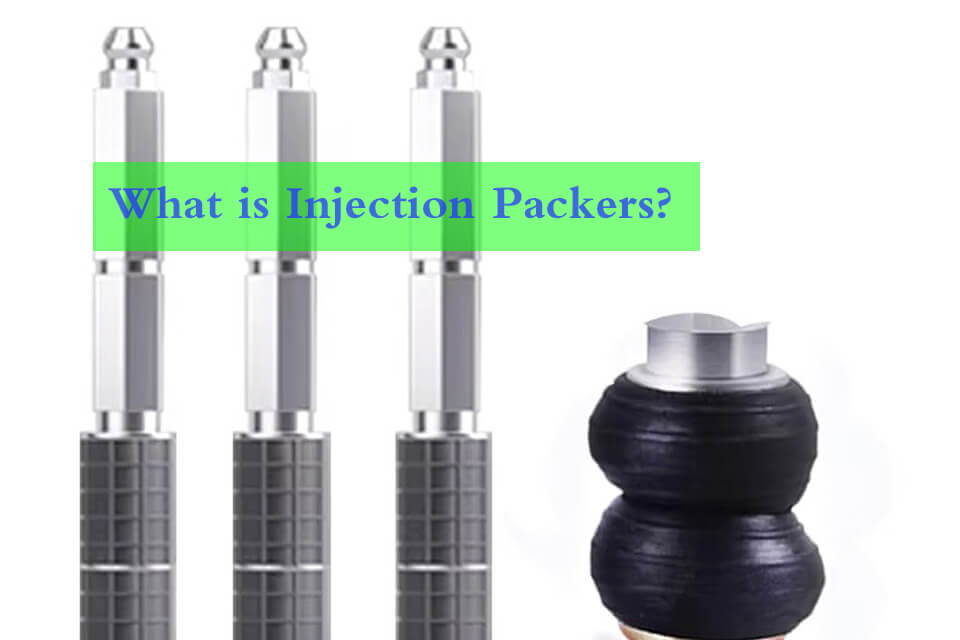
What Is Injection Packer
Injection packers are vital tools in both construction and maintenance sectors, designed to address critical issues related to sealing and waterproofing.
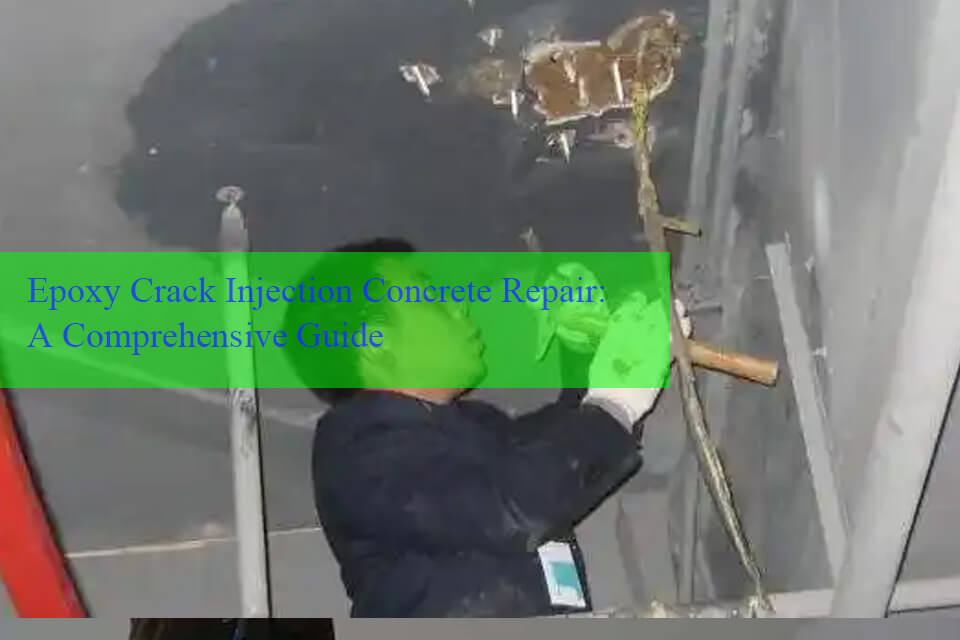
Comprehensive Guide of Epoxy Crack Injection Concrete Repair
Epoxy crack injection is a reliable and scientifically advanced method for repairing concrete structures, particularly those suffering from cracks.
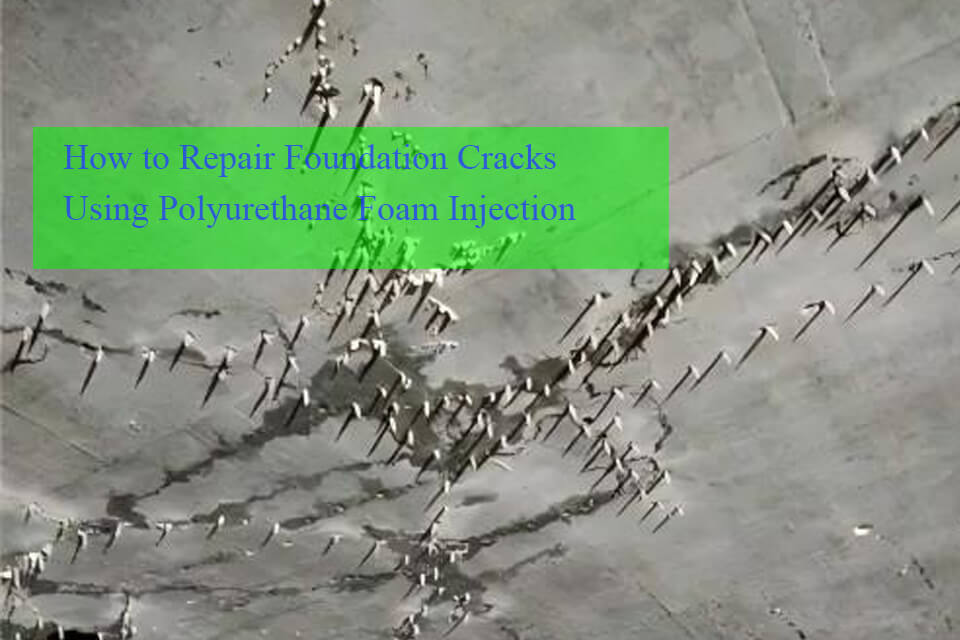
How to Repair Foundation Cracks Using Polyurethane Foam Injection
Foundation cracks can lead to serious structural issues if left unaddressed.