What Size are Injection Packers? A Complete Guide to Mechanical Injection Packers and Their Uses
Table of Contents
Summary
Choosing the correct packer size affects the efficiency, pressure, and distribution of repair materials like epoxy and polyurethane. This article will guide you through selecting the right injection packer for various applications, enhancing the effectiveness of your injection processes.
What is an Injection Packer?
An injection packer, often called a mechanical packer, is a small tool inserted into a drilled hole within concrete to facilitate the controlled injection of repair materials. Injection packers are essential in structural repair because they provide a secure, leak-proof channel through which epoxy or polyurethane can be injected under pressure, ensuring deep penetration into cracks
Why is the Size of Injection Packers Important?
Packer size influences how deeply materials penetrate and how well they fill the voids within cracks. Choosing the correct diameter ensures the packer fits the drilled hole snugly, avoiding leaks and pressure drops. An undersized packer may cause insufficient injection, while an oversized packer could damage the crack edges, leading to further structural issues.
Types of Mechanical Injection Packers
Packers are available in a range of materials, each suited for specific pressure levels and environments:
- Plastic Packers: Ideal for low-pressure applications, such as small cracks in non-structural areas.
- Steel Packers: Known for durability, these are best for high-pressure injections.
- Aluminum and Zinc Packers: Lightweight but durable, these packers provide a balance between performance and affordability.
How Do Mechanical Injection Packers with Zerk Fittings Work?
Zerk fittings are small components on packers that allow for easy lubrication, which is critical in high-pressure environments. Packers with these fittings are reusable, making them a cost-effective option for large projects requiring repeated injections.
Common Sizes and Diameters of Injection Packers
The following table outlines the common sizes of injection packers and their recommended uses:
Diameter (mm) | Material | Use Case |
10 | Plastic | Fine cracks, low pressure |
13 | Steel | Standard cracks |
16 | Aluminum | Heavy-duty applications |
The Role of Packers in Epoxy and Polyurethane Injection
Epoxy and polyurethane injection rely on packers to evenly distribute the material. Packers ensure that these substances penetrate deeply, fully sealing cracks for lasting structural integrity.
Steel vs. Plastic vs. Aluminum Packers: Which to Use?
Each material has its advantages:
- Steel packersare the top choice for high-pressure injections.
- Plastic packersare a budget-friendly option for less intense repairs.
- Aluminum packersstrike a balance between durability and cost.
Comparing Mechanical and Plastic Packers
While mechanical packers are often reusable and suited for high-pressure settings, plastic packers tend to be single-use but are ideal for smaller, simpler projects.
Injection Ports and Nipples: What You Need to Know
Injection packers often come with ports and nipples designed to control material flow. Some include Zerk-type nipples, which enhance maintenance and provide better control during injection.
Selecting the Right Injection Packers for Your Project
Consider the following when selecting a packer:
- Crack Width: Smaller cracks require finer packers.
- Material: Choose plastic, steel, or aluminum based on your project’s pressure needs.
- Injection Pressure: High-pressure jobs benefit from steel or aluminum packers.
Conclusion
- Select the Right Size: Properly sized packers are essential for effective crack sealing.
- Material Matters: Steel and aluminum offer durability, while plastic is suitable for smaller tasks.
- Use Zerk Fittings: Zerk fittings enhance reusability, particularly in high-pressure settings.
- Understand Injection Needs: The packer type significantly impacts the effectiveness of epoxy or polyurethane distribution.
This guide has provided insights into choosing the correct injection packer for any job. Proper selection leads to better outcomes, reduced costs, and increased efficiency in concrete repair and waterproofing tasks.
Comments
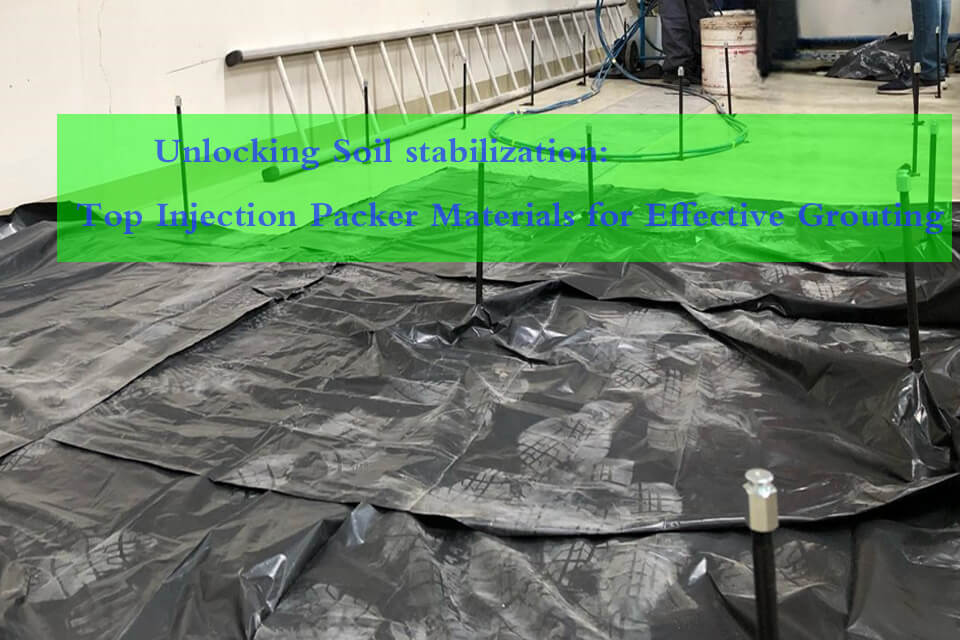
Unlocking the Secrets of Soil Stabilization: A Comprehensive Guide
Soil stabilization is a crucial process in construction and civil engineering that can make or break a project’s success.
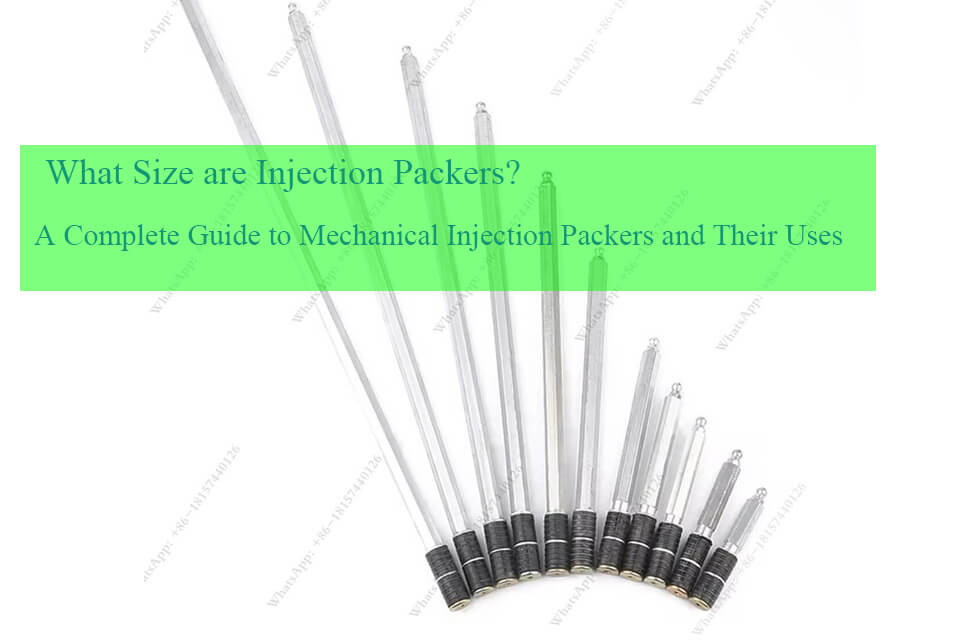
What Size are Injection Packers? A Complete Guide to Mechanical Injection Packers and Their Uses
When it comes to crack injection and waterproofing, the size and type of mechanical injection packers you use can make all the difference.
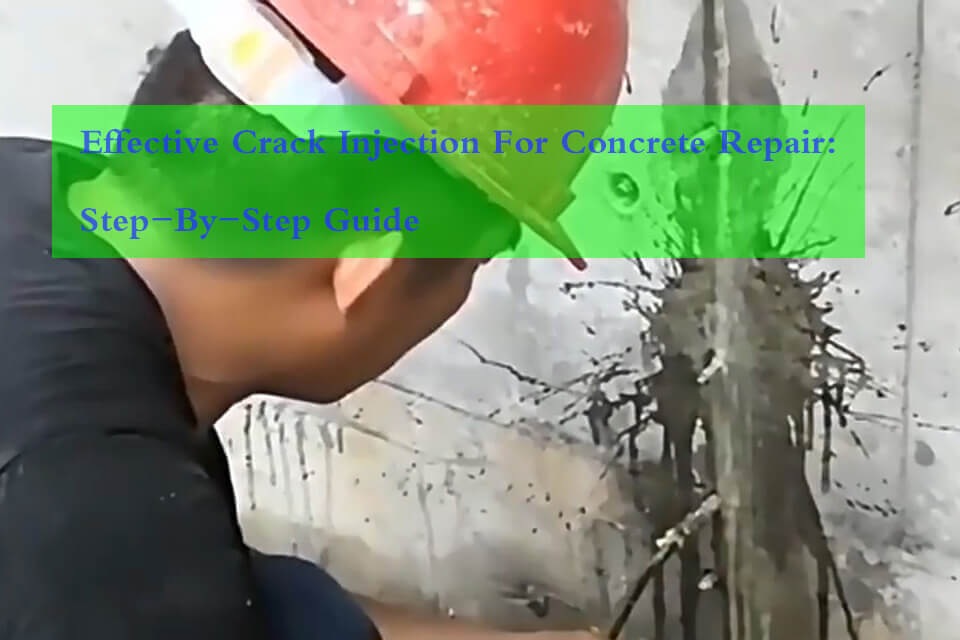
Effective Crack Injection for Concrete Repair: Step-by-Step Guide
Concrete cracks are a common issue in many structures, often leading to leaks that can cause significant damage if not properly sealed. Crack injection is a highly effective technique for repairing these cracks and stopping water infiltration.
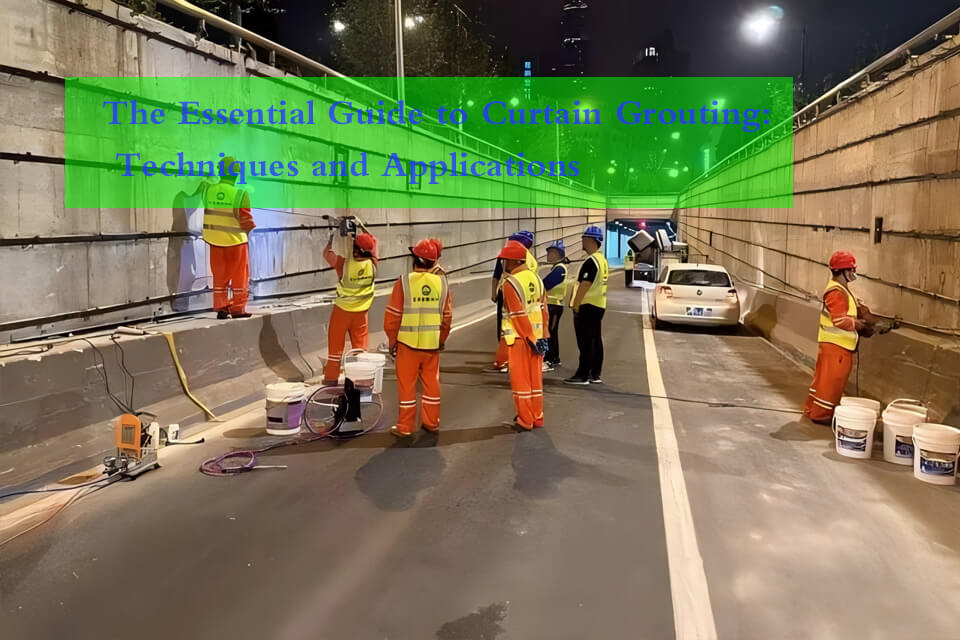
The Essential Guide to Curtain Grouting: Techniques and Applications
Curtain grouting is a revolutionary technique in the construction industry, particularly vital for preventing leaks and reinforcing structures.
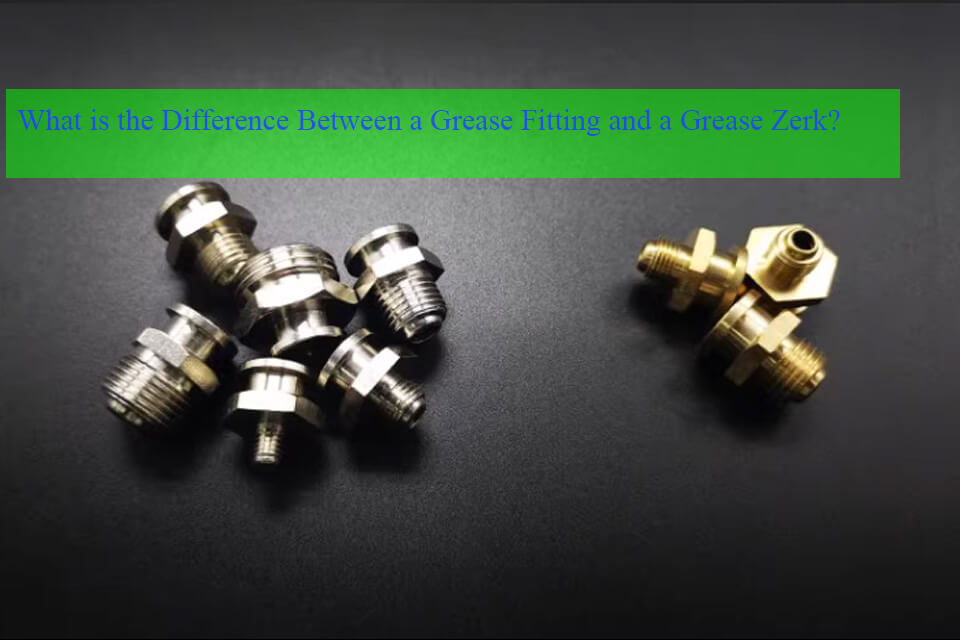
What is the Difference Between a Grease Fitting and a Grease Zerk?
If you’re in the world of machinery maintenance, you’ve likely come across the terms “grease fitting” and “grease zerk.”
- [email protected]
- +86 18157440126
- Mon-Sun 8:00-21:00
Tags
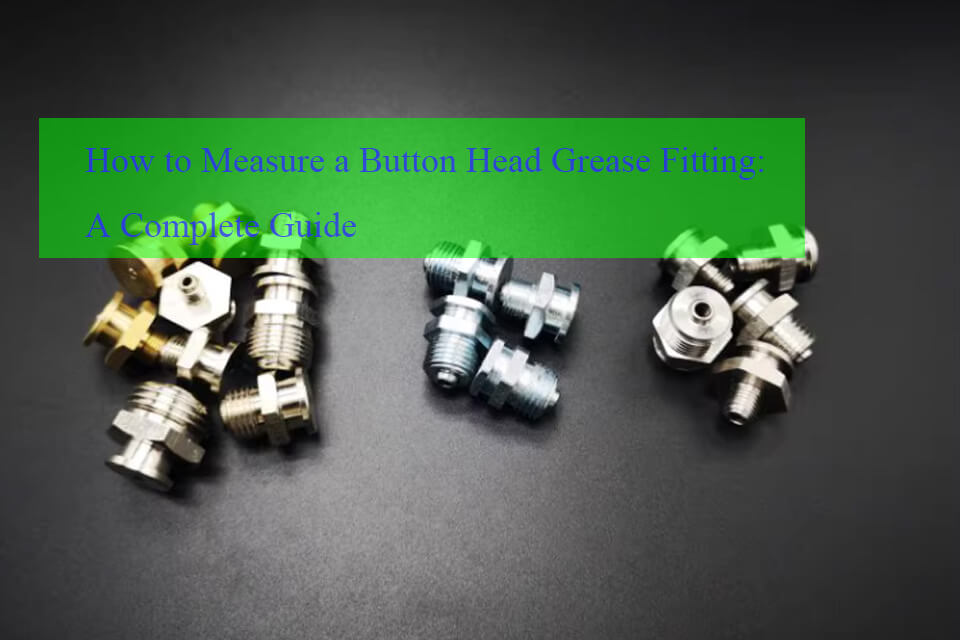
How to Measure a Button Head Grease Fitting: A Complete Guide
Button head grease fittings are widely used in heavy machinery and industrial applications, ensuring that grease is delivered effectively to vital components.
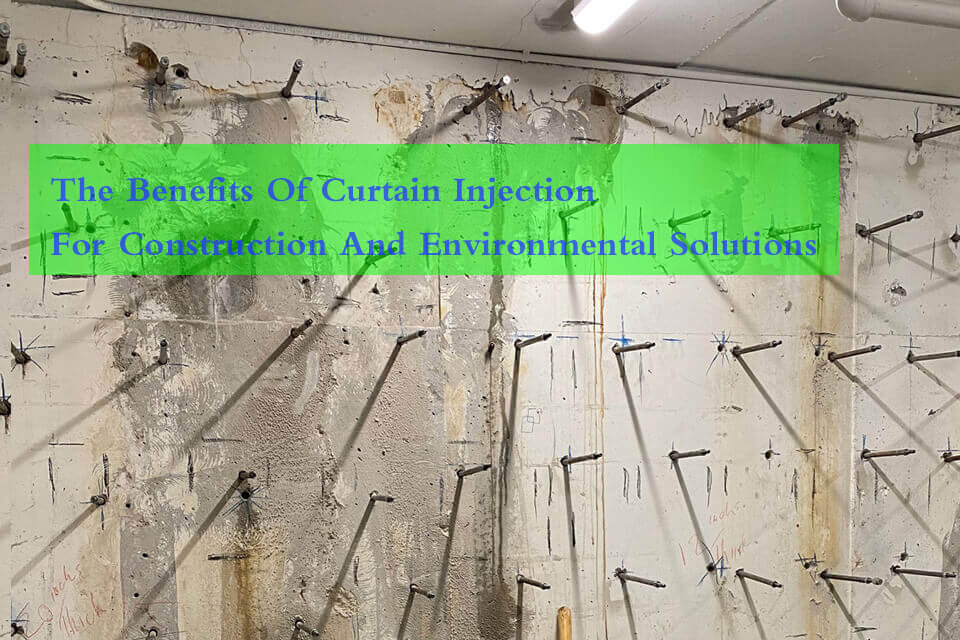
The Benefits of Curtain Injection for Construction and Environmental Solutions
Curtain injection, also known as curtain grouting or curtain wall injection, is an innovative technique widely used in construction, geotechnical engineering, and environmental protection.
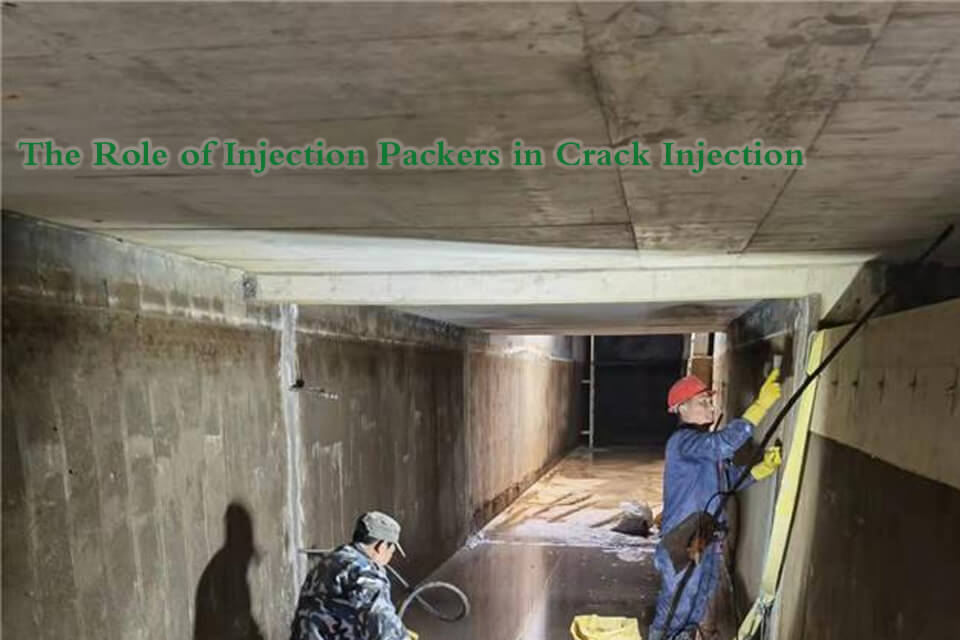
The Role of Injection Packers in Crack Injection and Structural Repair
Crack injection is a critical method used in the restoration and strengthening of concrete structures. It involves injecting an adhesive chemical grout or resin into the cracks of a foundation, slab, or wall to seal and restore structural integrity.