What Are Grease Fittings Used For?
Table of Contents
What Are Grease Fittings Used For?
Whether you work in automotive repair, heavy equipment maintenance, industrial manufacturing, or waterproofing filed, understanding how grease fittings work and their importance can save you time and money in repairs. This article will explore what grease fittings are, their uses, and why they are indispensable in daily machinery maintenance.
In this guide, we’ll break down the function of grease fittings, explain how they work with a grease gun, and discuss how they help keep your equipment running smoothly. If you’re wondering how to choose the right grease for different applications, or how to maintain and troubleshoot grease fittings, this article has got you covered. Keep reading to ensure you’re using grease fittings effectively for your machinery’s needs.
What Are Grease Fittings and What Are They Used For?
Grease fittings, also known as grease zerks, are small metal parts that allow grease to be pumped into machinery to lubricate moving components. These fittings are commonly found in places where parts experience friction, such as hinges, joints, or bearings in vehicles, construction equipment, or industrial machinery.
The main purpose of grease fittings is to reduce friction between moving parts, prevent rust and corrosion, and extend the lifespan of equipment by ensuring smooth operation.
Why You Need Grease Fittings?
- Improved Performance: By providing constant lubrication, grease fittings reduce wear and tear on mechanical parts.
- Prevents Corrosion: Regular lubrication keeps metal parts from rusting or getting damaged due to moisture or chemicals.
- Increases Equipment Lifespan: Lubricating the right parts at the right intervals helps avoid costly repairs and downtime.
How Do Grease Fittings Work?
Grease fittings work by allowing grease to be pumped into the lubrication points of machinery. They are installed on equipment where regular lubrication is needed, typically using a grease gun to inject grease into the fitting. The grease then flows into the internal parts, reducing friction and providing the necessary lubrication to keep the machine running efficiently.
Once the grease is applied, the fitting usually has a valve mechanism (like the ball check valve found in zerk fittings) that helps trap the grease inside, preventing it from leaking out.
How the Process Works
- Attach the Grease Gun: The first step is to attach a grease gun nozzle to the grease fitting.
- Pump the Grease: Once the nozzle is connected, you pump the grease gun, which forces grease into the machinery’s internal parts.
- Seal the Fitting: After the grease is applied, the fitting closes, preventing leakage and ensuring that the grease remains in the machinery.
What is the Role of a Grease Gun in Grease Fittings?
A grease gun is a tool used to apply grease into grease fittings. It works in tandem with the fitting, allowing for easy and controlled lubrication. There are different types of grease guns available, including manual, pneumatic, and electric versions. Each type can be used depending on the size of the machinery, the volume of grease needed, and the frequency of use.
Grease guns make the lubrication process much easier and more efficient, providing a convenient method for applying consistent amounts of grease to machinery.
Benefits of Using a Grease Gun
- Consistency: Ensures that the right amount of grease is applied to the fitting.
- Convenience: Allows quick and easy lubrication without disassembling parts.
- Prevents Over-greasing: Helps avoid excessive lubrication, which could damage seals or create leaks.
How Do You Choose the Right Grease Fitting for Your Equipment?
Choosing the right grease fitting is crucial for effective lubrication. Factors such as the type of machinery, the operating environment, and the specific lubrication needs must be considered. Grease fittings come in different sizes, materials, and thread types, and selecting the correct one ensures that grease can be properly applied and retained.
Considerations When Choosing a Grease Fitting
- Size and Thread: Make sure the size and thread of the fitting match your machinery’s requirements.
- Application Type: Some machinery may require straight, angled, or button-head grease fittings depending on accessibility.
- Grease Compatibility: Different machines may require specific types of grease, such as high-temperature or high-pressure grease.
What Is the Difference Between a Standard Grease Fitting and a Zerk Fitting?
A zerk fitting is a brand-specific name for a type of grease fitting, and it’s often used interchangeably with the term “grease fitting.” However, zerk fittings are typically equipped with a ball check valve, which helps prevent grease from leaking out once it’s been applied. In contrast, standard grease fittings may lack this feature and can sometimes result in more leakage.
Key Differences:
Feature | Standard Grease Fitting | Zerk Fitting |
Valve Mechanism | May or may not have a valve | Typically has a ball check valve |
Leakage | Higher chance of leakage | Retains grease, reduces leakage |
Use | General lubrication needs | More common in high-pressure areas |
How to Properly Lubricate Equipment with Grease Fittings
Lubricating equipment with grease fittings is simple, but there are best practices to ensure efficiency. First, check that the grease fitting is properly installed and clean before use. Then, use a grease gun to apply the right amount of grease to the fitting
Best Practices for Lubrication
- Check the Grease Fitting: Ensure it’s not clogged and that it is free of debris.
- Use the Right Type of Grease: Refer to the equipment’s manual to select the appropriate grease for the machinery.
- Apply the Right Amount: Apply enough grease to fill the internal parts, but avoid over-greasing, which can damage seals.
What Types of Grease Are Best for Grease Fittings?
Not all greases are suitable for every application. The type of grease you use depends on the operating conditions of the machinery, such as temperature, pressure, and exposure to contaminants.
Common Types of Grease
- Lithium-based Grease: Ideal for general-purpose lubrication in normal temperatures.
- Molybdenum Disulfide Grease: Used for high-pressure applications, like heavy-duty machinery.
- Synthetic Grease: Offers better performance in extreme temperatures or harsh conditions.
Selecting the Right Grease
Check the manufacturer’s recommendations for grease types to ensure compatibility with your grease fittings and machinery.
Why Is It Important to Maintain Your Grease Fittings?
Regular maintenance of your grease fittings is vital for optimal machinery performance. Grease fittings can become clogged over time due to hardened grease, dirt, or contamination, leading to insufficient lubrication. If left unchecked, this can cause increased friction, wear, and even mechanical failure.
Maintenance Tips
- Clean the Fittings: Regularly clean grease fittings to remove old grease and prevent blockages.
- Inspect for Wear: Look for signs of damage or wear, which may require replacing the fitting.
Common Issues with Grease Fittings and How to Fix Them
Grease fittings can sometimes malfunction or become clogged, causing issues in lubrication. Common problems include grease leakage, clogged fittings, or difficulty in applying grease.
How to Fix Common Issues
- Clogged Fittings: Use a grease fitting unblockeror needle to clear the clog.
- Leaking Grease: If the fitting is leaking, check for damaged seals or replace the fitting if necessary.
- Stiff Grease: If the grease is too thick, ensure you’re using the right grease for your equipment’s operating conditions.
Frequently Asked Questions (FAQ)
How do I know if my grease fitting is clogged?
A clogged fitting may not allow grease to flow in properly, or you may notice resistance when using the grease gun. Inspect the fitting for visible signs of grease buildup or blockages.
What should I do if my grease fitting is leaking?
First, check if the fitting is properly tightened. If the fitting is damaged, replace it. If the seal is worn, consider replacing the fitting with a new one.
Can I use any grease in all fittings?
No, you should always use the type of grease recommended by the equipment manufacturer to ensure compatibility with the grease fitting and machinery.
Key Takeaways
- Grease fittingsare essential for maintaining the smooth operation of machinery by providing lubrication to reduce friction.
- The grease gunplays a crucial role in efficiently applying grease to fittings.
- Regular maintenance and choosing the correct grease fittingand grease type are critical to ensuring optimal performance and longevity of your equipment.
- Issues like clogs, leaks, and incompatibilitycan be avoided with proper care and attention.
By understanding grease fittings and following these guidelines, you can ensure that your machinery stays well-lubricated and operates efficiently, reducing maintenance costs and extending the life of your equipment.
Comments
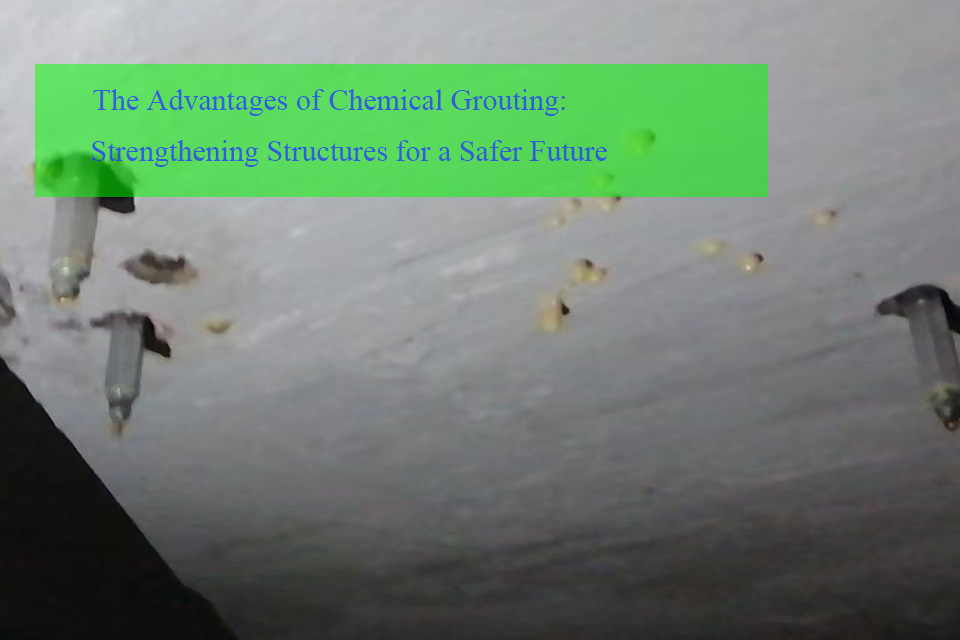
The Advantages of Chemical Grouting: Strengthening Structures for a Safer Future
Chemical grouting is a powerful and versatile solution for strengthening soil, sealing leaks, and stabilizing foundations in challenging construction environments.
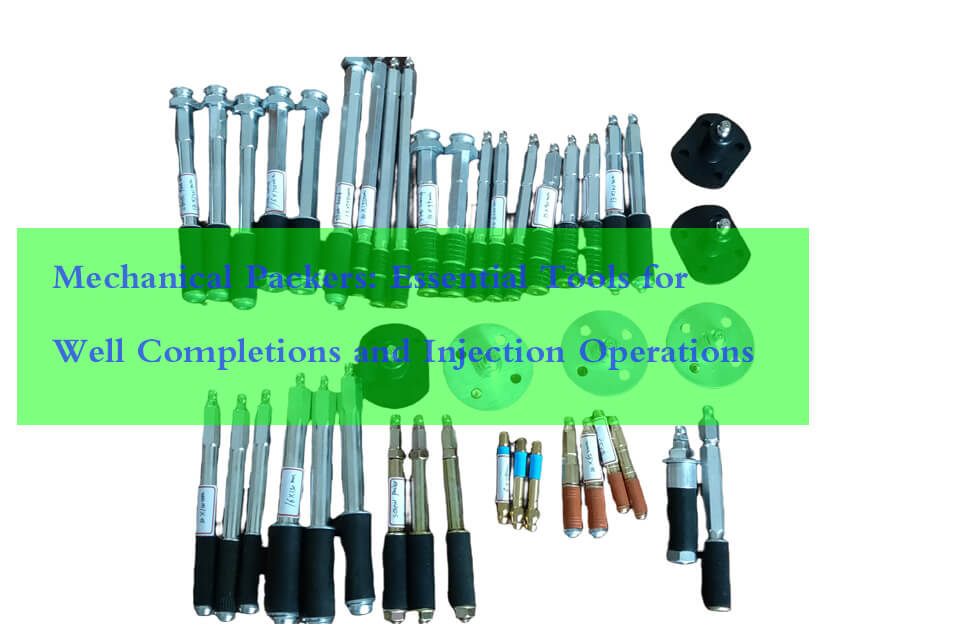
Mechanical Packers: Essential Tools for Well Completions and Injection Operations
Mechanical packers play a crucial role in well completions and injection operations across various industries.
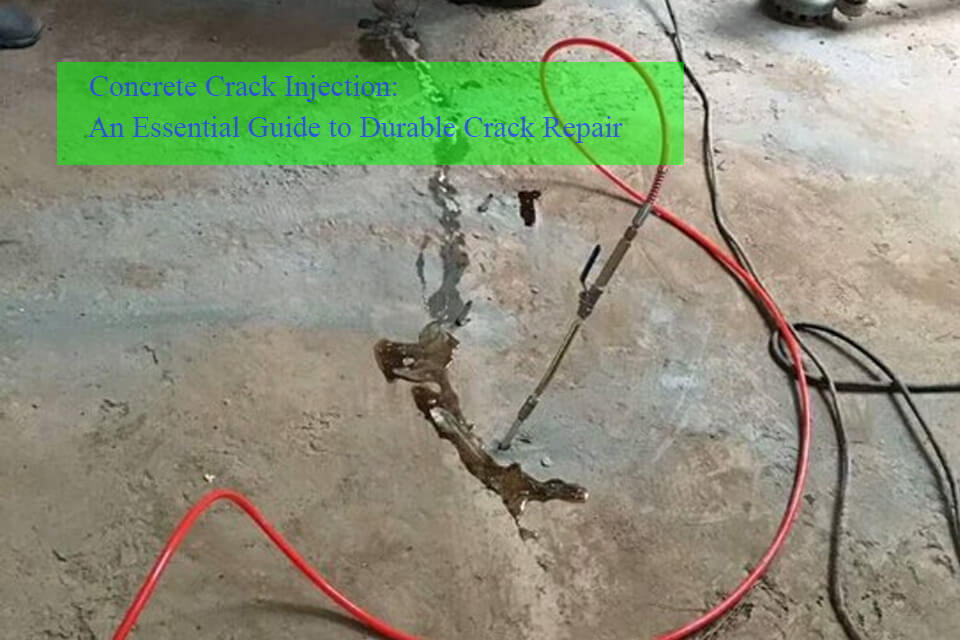
Concrete Crack Injection: An Essential Guide to Durable Crack Repair
Concrete structures are built to be strong and long-lasting, but even the best concrete can develop cracks over time.
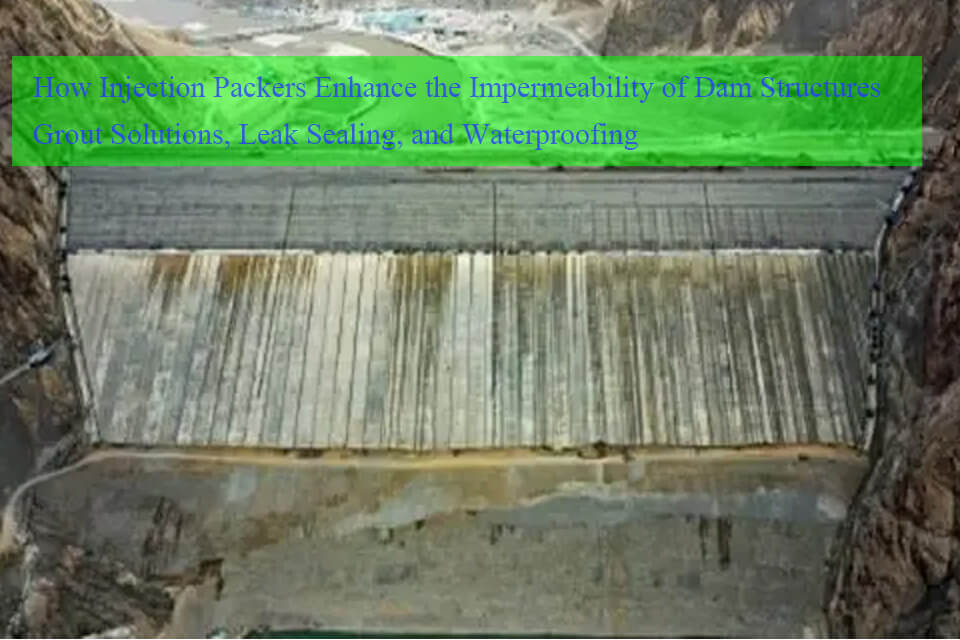
How Injection Packers Enhance the Dam Structures Impermeability
Keeping a dam waterproof is essential for maintaining its structural integrity and preventing water erosion.
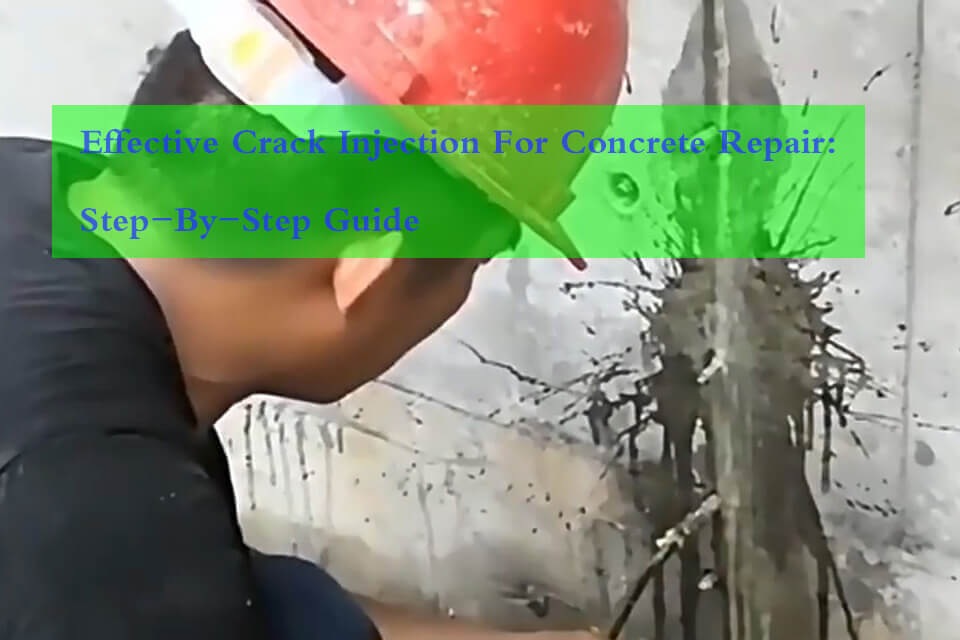
Effective Crack Injection for Concrete Repair: Step-by-Step Guide
Concrete cracks are a common issue in many structures, often leading to leaks that can cause significant damage if not properly sealed. Crack injection is a highly effective technique for repairing these cracks and stopping water infiltration.
- [email protected]
- +86 18157440126
- Mon-Sun 8:00-21:00
Tags
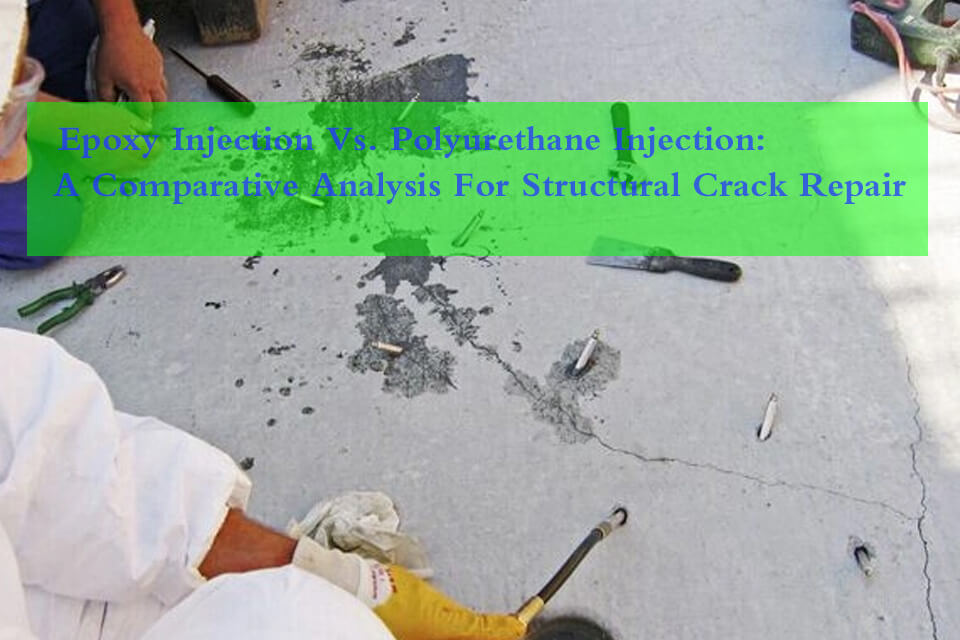
Epoxy Injection vs. Polyurethane Injection: A Comparative Analysis for Structural Crack Repair
Epoxy injection and polyurethane injection are two widely used methods for repairing cracks in concrete structures, each distinguished by its unique chemical properties and applications.
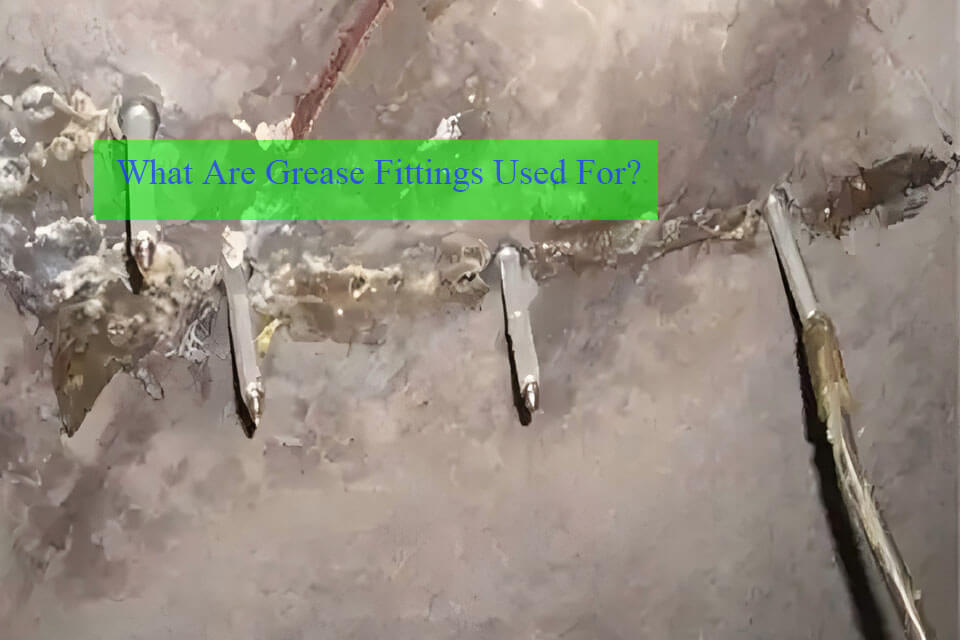
What Are Grease Fittings Used For?
Grease fittings, also known as zerk fittings, are small but critical components in the world of machinery maintenance and waterproof industry.
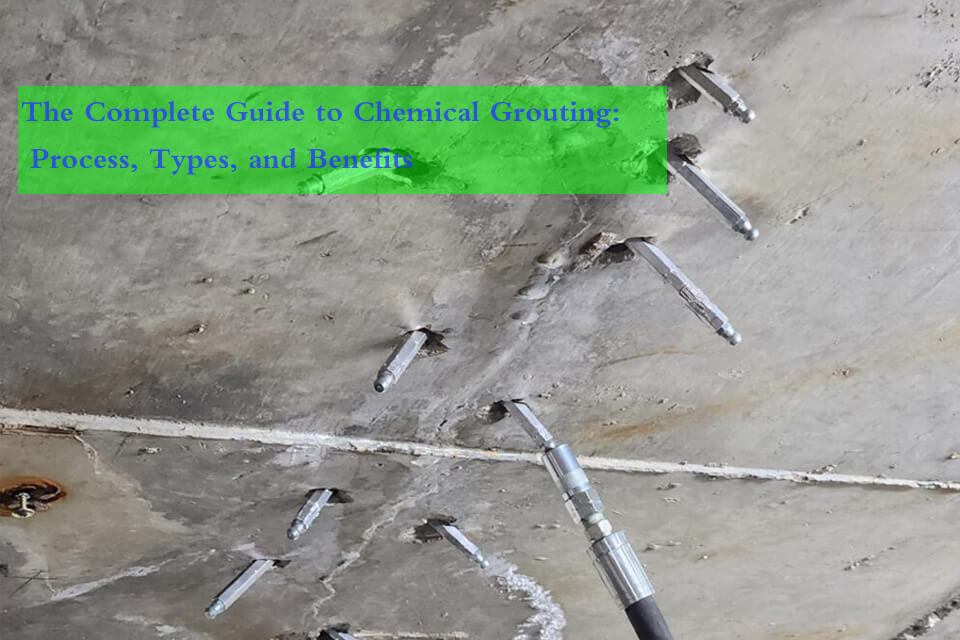
The Complete Guide to Chemical Grouting: Process, Types, and Benefits
Chemical grouting is a powerful and versatile technique used in construction and engineering projects to stabilize soil, control water flow, and enhance the structural integrity of various substrates.