What is the Difference Between a Grease Fitting and a Grease Zerk?
Table of Contents
What is the Difference Between a Grease Fitting and a Grease Zerk?
Both play crucial roles in keeping equipment running smoothly, but what’s the actual difference between them? In this article, we’ll break down the functions, types, and benefits of grease fittings and zerks, explore when each should be used, and provide practical tips on their maintenance and selection. This guide will be invaluable for anyone looking to optimize their lubrication process, prevent equipment breakdowns, and ensure the longevity of machinery.
Introduction to Grease Fittings and Zerks
Grease fittings, also known as “zerk fittings,” are vital in heavy equipment maintenance, allowing for direct injection of grease into specific machine parts. Despite the interchangeable use of these terms, grease fittings and zerks can refer to slightly different applications depending on context and region.
What Exactly is a Grease Zerk?
A grease zerk is a type of fitting designed with a unique ball check mechanism that opens to allow grease in but closes to prevent contaminants from entering. This one-way valve is particularly effective at delivering grease to bearings, hinges, fifth wheels, and other critical machinery parts that need consistent lubrication. Zerk fittings are known for their durability and ease of use.
Feature | Description |
Mechanism | Ball check valve that opens with pressure |
Common Use | Bearings, joints, high-contact surfaces |
Benefits | Prevents dirt and debris from contaminating lubricated parts |
Sizes | Available in various metric and SAE standards |
Understanding Standard Grease Fittings
While all zerks are grease fittings, not all grease fittings are zerks. Standard grease fittings can include push-in or press-on types that serve similar functions but may lack the ball check valve characteristic of zerks. These fittings allow for grease to be added but may vary in shape, size, and design depending on the machinery.
Type | Features | Common Applications |
Push-in Fitting | Fits with pressure | Light machinery, automotive joints |
Press-on Fitting | Snaps into place | Bikes, small engines, minimal usage |
Zerk Fitting | Threaded or press-fit with valve | Heavy machinery, industrial equipment |
Grease Zerks vs. Grease Fittings: Key Differences
Both grease fittings and grease zerks serve similar purposes but differ slightly in design and application adaptability.
- Grease Zerks: Feature a check valve, ideal for industrial use due to their dirt-prevention capabilities.
- Standard Grease Fittings: Come in multiple forms, with or without a check valve, providing more flexibility for different types of machinery.
Did you know? Zerk fittings are named after Oscar U. Zerk, the inventor, who patented them in the early 20th century for enhanced machinery lubrication.
How to Choose the Right Grease Fitting or Zerk for Your Machinery
Choosing the right grease fitting is crucial for optimal lubrication and longevity of equipment. Consider the following when selecting a fitting:
- Machine Requirements: Check if your machine requires metric or SAE fittings.
- Lubrication Needs: Heavy-duty equipment may need zerks due to their dirt-blocking valve.
- Fitting Size: Matching fitting size is key to ensuring a proper fit and function.
Criteria | Recommended Type |
High-Contact Surfaces | Zerk Fittings |
Light Machinery | Standard Grease Fittings |
Heavy-Duty Equipment | Zerks with high-pressure ratings |
Metric vs. SAE Fittings: How to Tell the Difference
In the United States, grease fittings are often standardized as SAE (Society of Automotive Engineers), while metric fittings are more common in European and Asian machinery. Understanding the difference is essential for maintenance and repair compatibility.
- Metric Fittings: Measured in millimeters (e.g., M6, M8).
- SAE Fittings: Measured in inches (e.g., 1/4″, 1/8″).
Pro Tip: Always double-check the manufacturer’s specifications for recommended fitting sizes and thread standards.
Safety Tips for Using Grease Fittings and Zerks
Safety is paramount when working with grease fittings and zerks, especially when using high-pressure grease guns.
- Wear Protective Gear: Gloves and eye protection are essential when dealing with grease to avoid contamination.
- Secure the Fitting: Ensure the grease fitting is fully engaged with the coupler to prevent leakage.
- Check Pressure Ratings: Exceeding the recommended pressure can cause fittings to burst or detach unexpectedly.
“Always remember to depressurize your grease gun after use to maintain its longevity and avoid accidental discharge.”
Common Applications for Grease Zerks and Fittings
Grease zerks and fittings are used across multiple industries, including:
- Automotive: For lubrication of suspension components, joints, and wheel bearings.
- Industrial Machinery: In high-stress areas like fifth wheels, bearings, and hinges.
- Agricultural Equipment: For maintaining heavy-use parts such as axles, gears, and PTO shafts.
Maintaining Your Grease Zerks and Fittings
Proper maintenance of your grease fittings will extend their lifespan and ensure reliable lubrication.
- Regular Inspection: Check fittings for blockages or wear every 3-6 months.
- Use the Right Grease: Avoid mixing grease types to prevent chemical breakdown.
- Clean Before Application: Always wipe off the fitting before greasing to keep out dirt and debris.
Maintenance Task | Frequency |
Inspect for Blockages | Every 3-6 months |
Clean Fitting Before Use | Every Use |
Lubricate Parts | As Needed |
FAQs on Grease Zerks and Fittings
Can I use a zerk fitting in place of a standard grease fitting?
Yes, zerks are a type of grease fitting and can replace standard fittings where appropriate. However, verify compatibility with your machine.
What type of grease should I use with zerks?
Use grease specified by your machinery’s manufacturer. For heavy-duty equipment, high-viscosity grease is often preferred.
How do I know if my fitting is metric or SAE?
Check the fitting size and markings. Metric fittings are in millimeters (M6, M8), while SAE uses inches (1/8″, 1/4″).
Summary of Key Points
- Grease zerks and standard grease fittings serve similar functions but have distinct design features.
- Metric and SAE fittings differ in size standards; always check compatibility with your equipment.
- Safety is key when using high-pressure grease guns; always wear protective gear and check fitting integrity.
- Regular maintenance and proper grease selection will prolong the life of your fittings and machinery.
Grease fittings and zerks play a crucial role in the health and longevity of industrial and mechanical equipment. Knowing the differences, uses, and maintenance steps for each fitting type can help ensure your machinery operates efficiently for years to come.
Comments
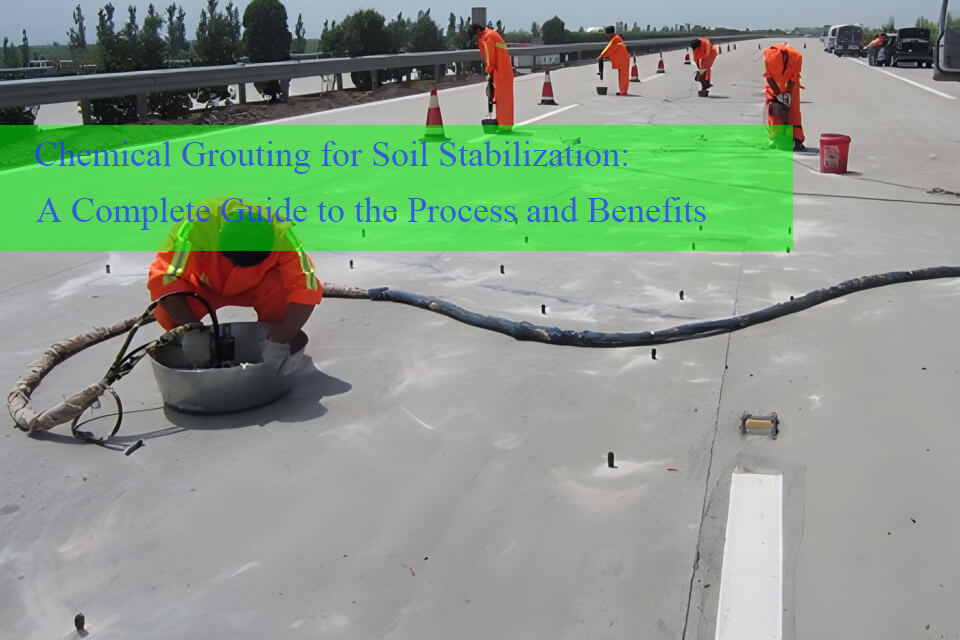
Chemical Grouting for Soil Stabilization: A Complete Guide to the Process and Benefits
Chemical grouting is an effective method for soil stabilization and strengthening structures in construction and civil engineering.
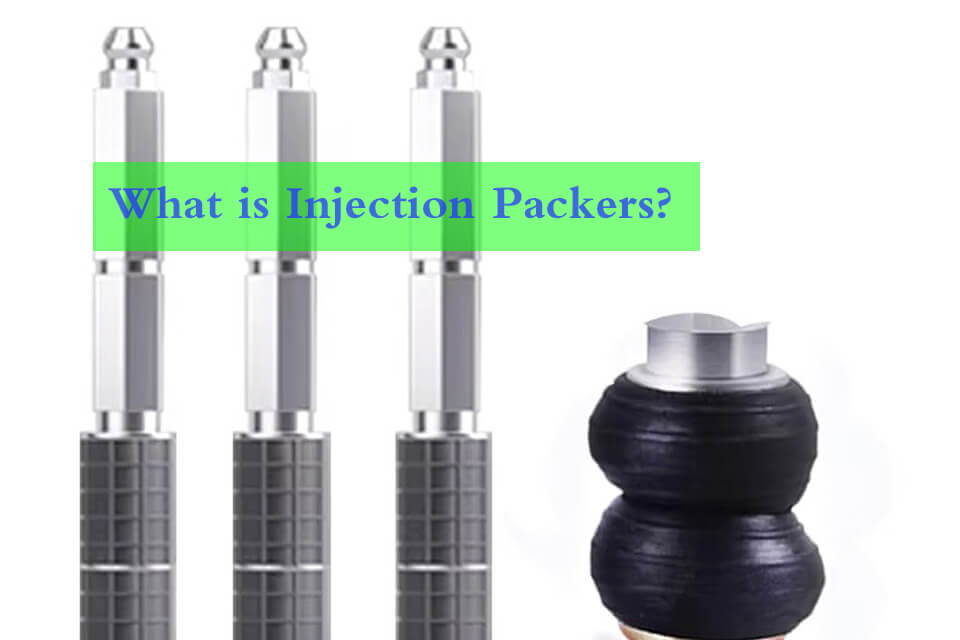
What Is Injection Packer
Injection packers are vital tools in both construction and maintenance sectors, designed to address critical issues related to sealing and waterproofing.
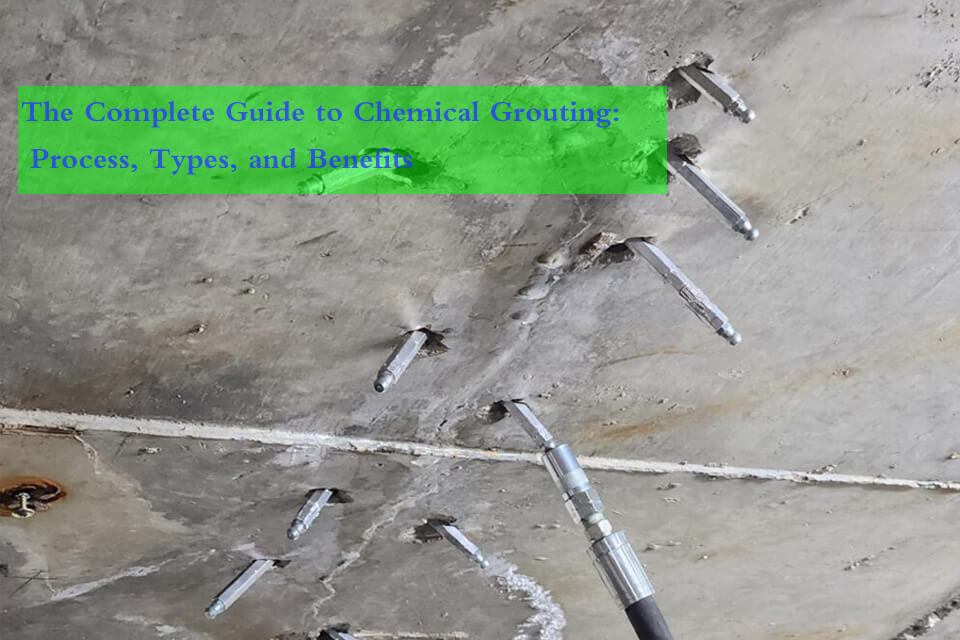
The Complete Guide to Chemical Grouting: Process, Types, and Benefits
Chemical grouting is a powerful and versatile technique used in construction and engineering projects to stabilize soil, control water flow, and enhance the structural integrity of various substrates.
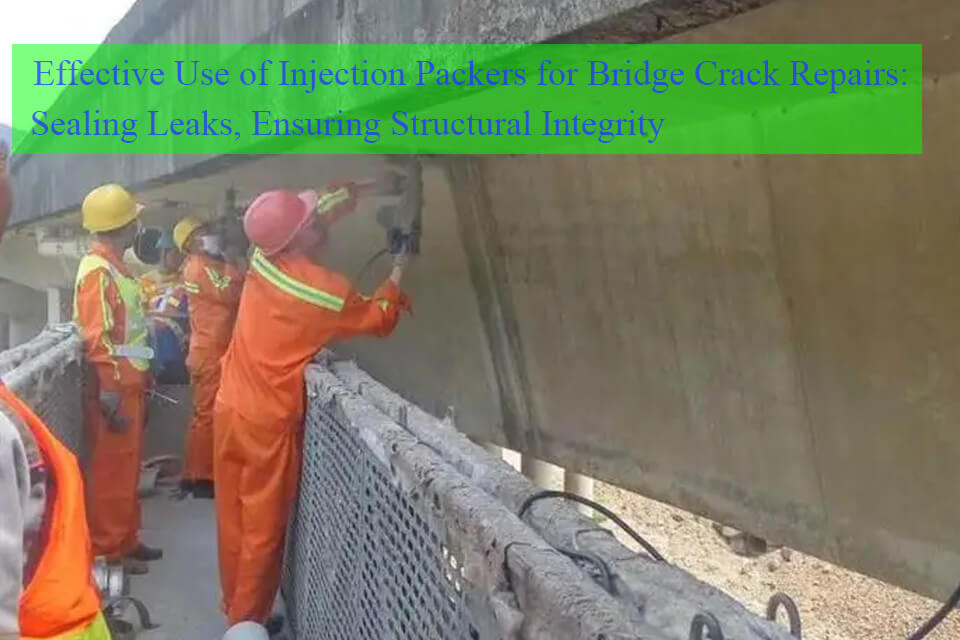
Effective Use of Injection Packers for Bridge Crack Repairs
Cracks in bridges can lead to leaks, structural weaknesses, and increased repair costs if not promptly addressed
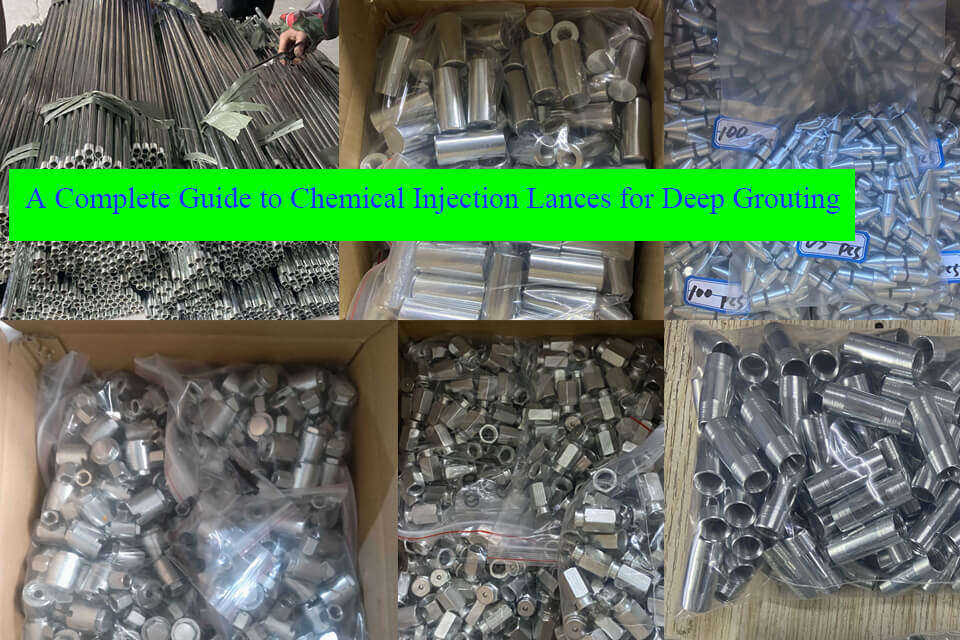
A Complete Guide to Chemical Injection Lances for Deep Grouting
Chemical injection lances, also known as grout injection lances, are an advanced solution for deep chemical grouting applications.
- [email protected]
- +86 18157440126
- Mon-Sun 8:00-21:00
Tags
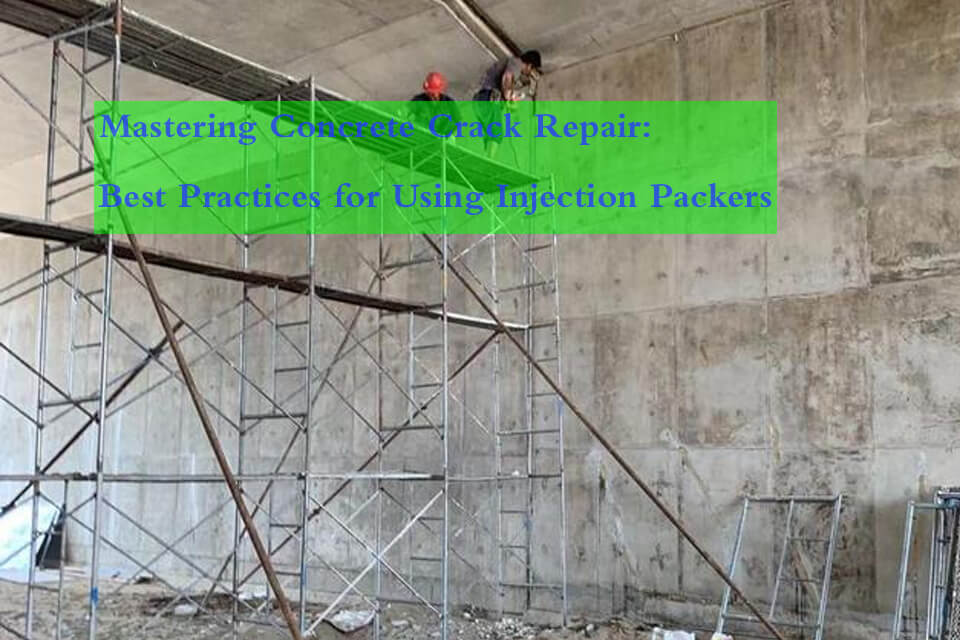
Mastering Concrete Crack Repair: Best Practices for Using Injection Packers
Concrete crack repair is a critical aspect of maintaining the structural integrity and longevity of buildings and infrastructure.
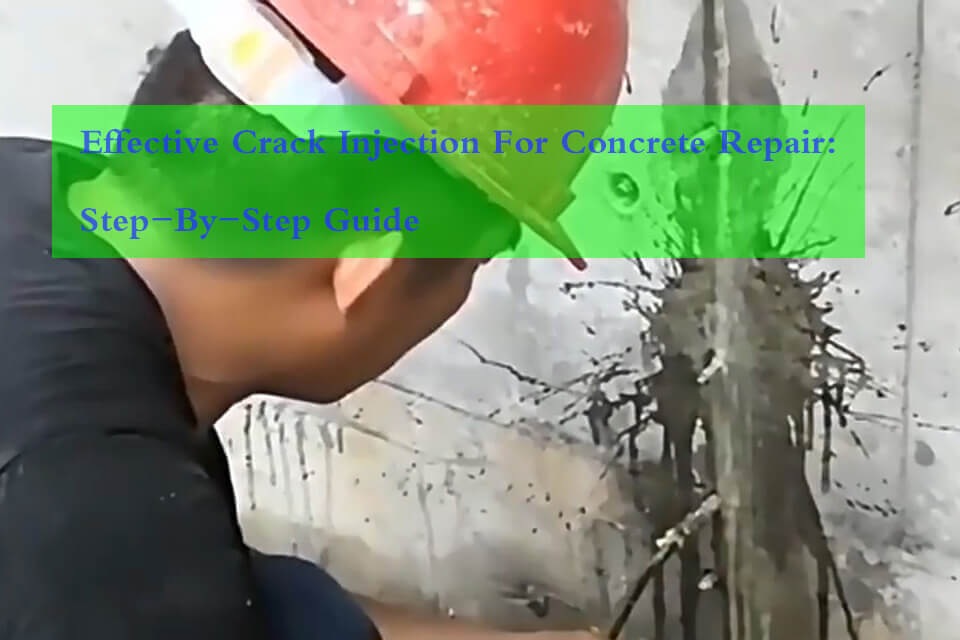
Effective Crack Injection for Concrete Repair: Step-by-Step Guide
Concrete cracks are a common issue in many structures, often leading to leaks that can cause significant damage if not properly sealed. Crack injection is a highly effective technique for repairing these cracks and stopping water infiltration.
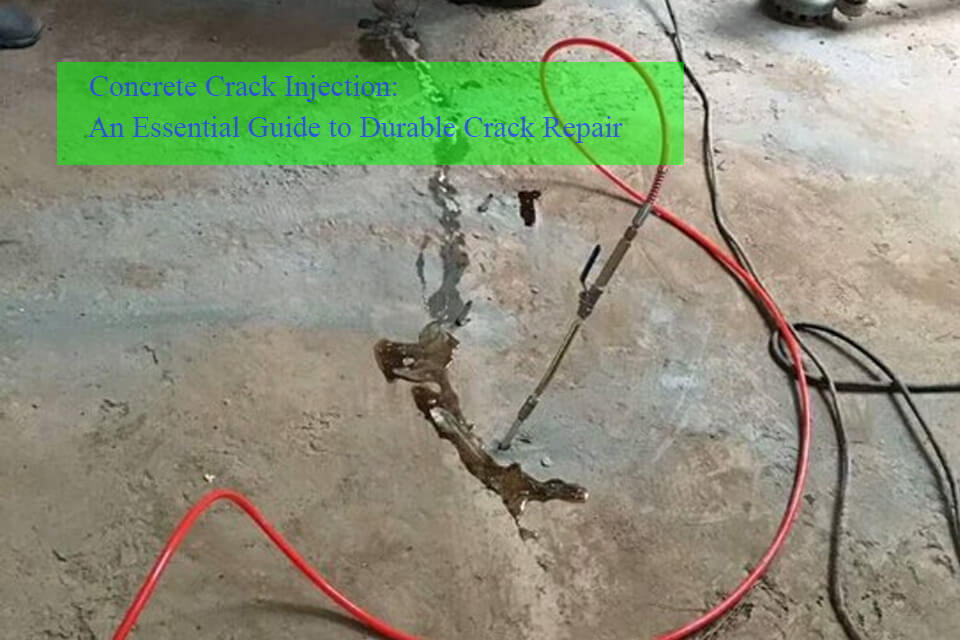
Concrete Crack Injection: An Essential Guide to Durable Crack Repair
Concrete structures are built to be strong and long-lasting, but even the best concrete can develop cracks over time.