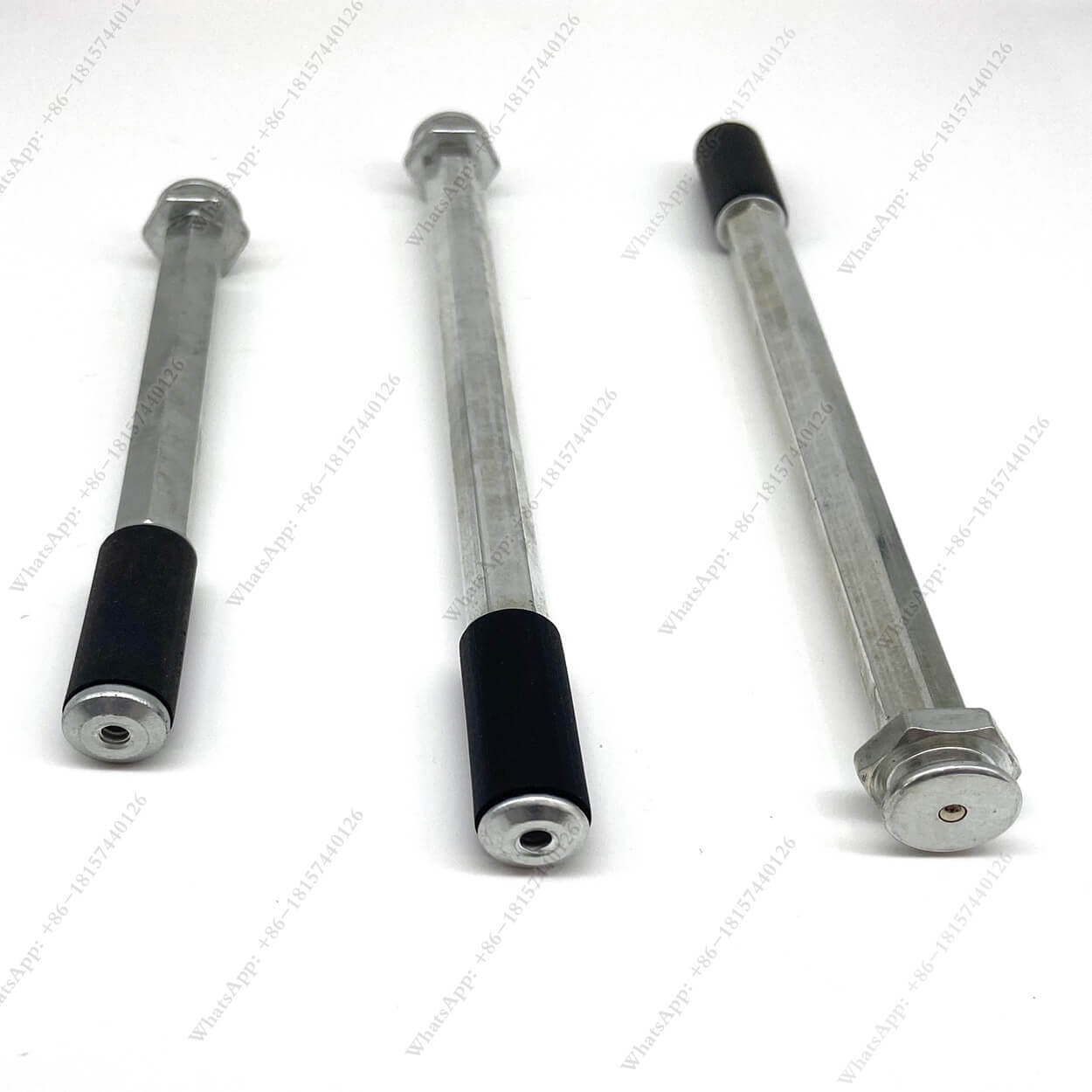
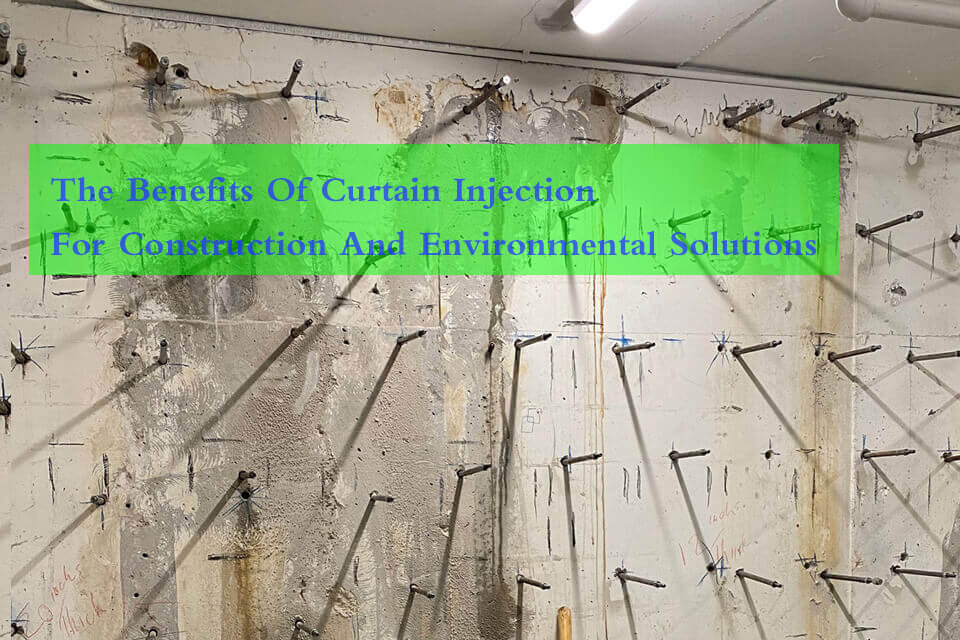
The Benefits of Curtain Injection for Construction and Environmental Solutions
Curtain injection, also known as curtain grouting or curtain wall injection, is an innovative technique widely used in construction, geotechnical engineering, and environmental protection.
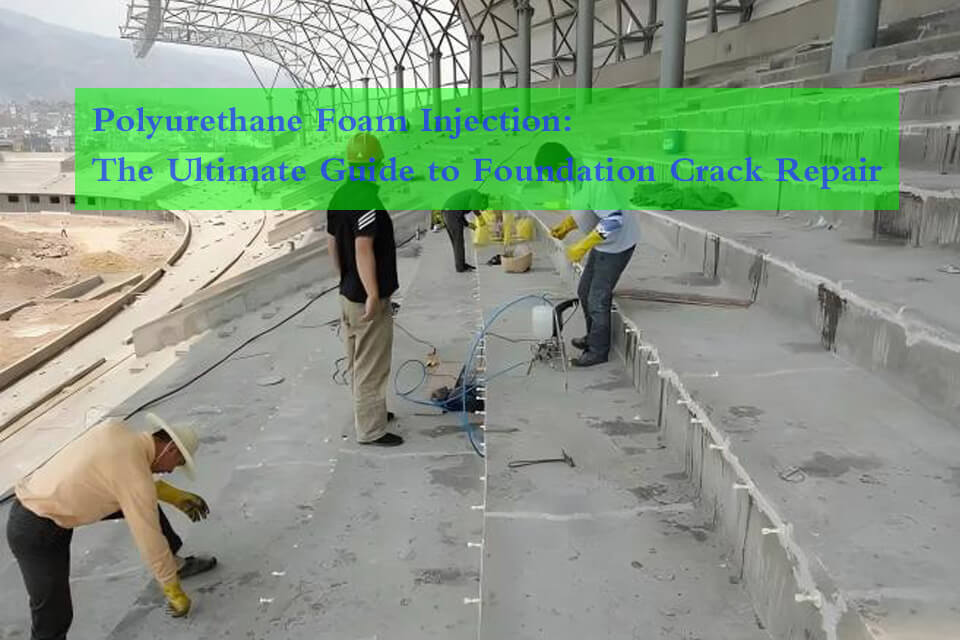
Polyurethane Foam Injection: The Ultimate Guide to Foundation Crack Repair
Are you dealing with pesky foundation cracks that just won’t go away? Look no further! This comprehensive guide will walk you through the innovative solution of polyurethane foam injection for crack repair.
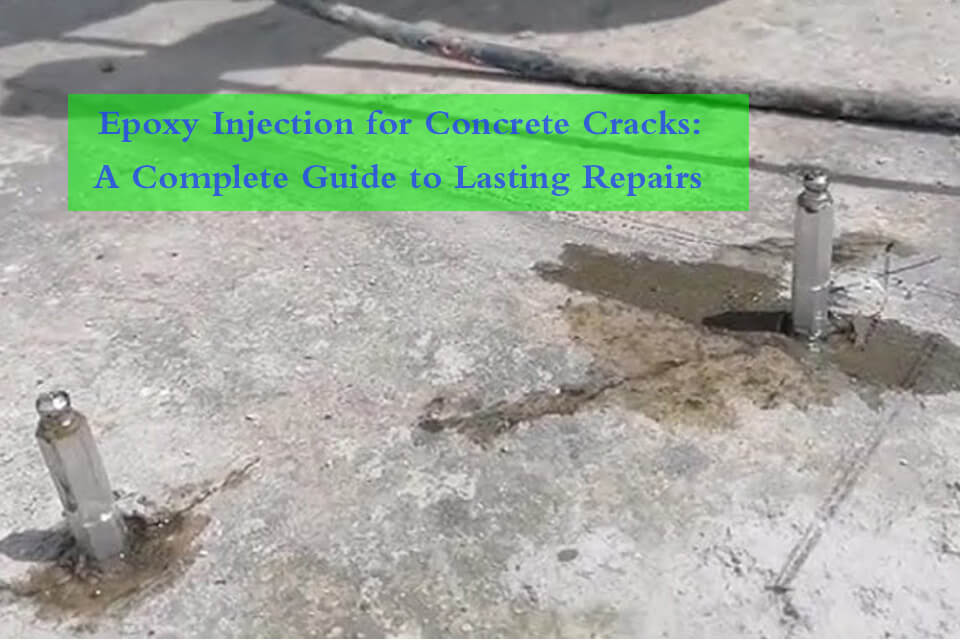
Epoxy Injection for Concrete Cracks: A Complete Guide to Lasting Repairs
In this article, learn how epoxy injection effectively restores structural integrity to cracked concrete, providing a durable, lasting solution.